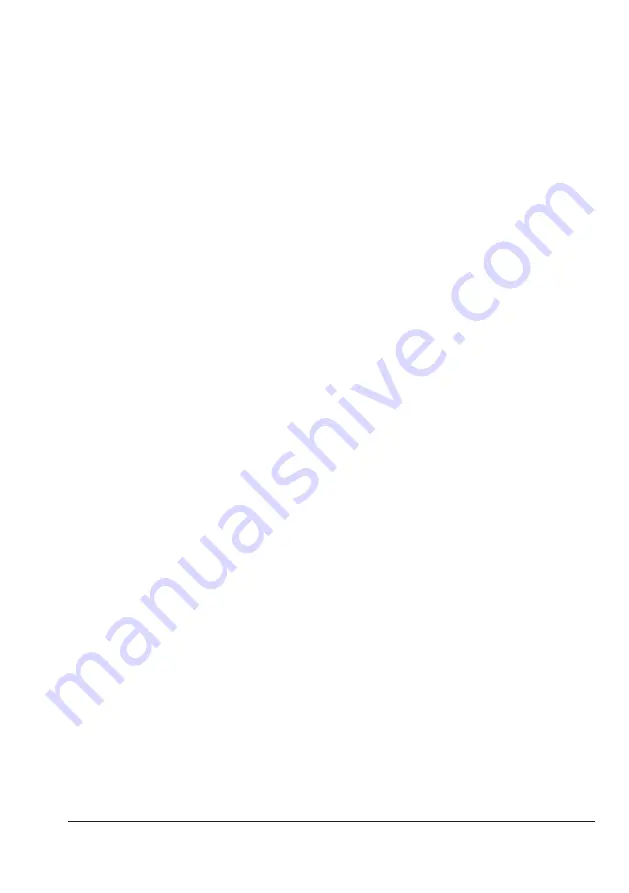
EB 8359-2 EN
3-1
Design and principle of operation
3
Design and principle of oper
-
ation
The electropneumatic positioner is used to
assign the valve position (controlled variable)
to the input signal (set point). The positioner
compares the control signal of a control sys-
tem to the travel of the control valve and is-
sues a signal pressure (output variable) for
the pneumatic actuator.
The positioner consists of an electropneumat-
ic converter unit (21) and a pneumatic unit
equipped with a lever (1), shaft (1,1) and
range spring as well as the pneumatic con-
trol system with nozzle, flapper plate and
booster. The DC control signal, e.g. 4 to
20 mA, issued by the controller, is transmit
-
ted to the electropneumatic converter unit
(i/p converter) where it is converted into a
proportional pressure signal p
e
.
Any change of the input current signal caus-
es a proportional change of the air pressure
p
e
fed to the pneumatic control system.
The air pressure p
e
produces a force which
acts on the surface of the measuring dia-
phragm (8) and is compared to the force of
the range spring (6).
The motion of the measuring diaphragm (8)
is transferred to the flapper plate (10.2) over
the feeler pin (9.1) and the nozzle (10.1) re
-
leases pressure. Any change of either the air
pressure p
e
or the valve stem position causes
the pressure to change in the booster (12)
connected downstream of the nozzle. The
signal pressure p
st
which is released causes
the plug stem to assume a position based on
the set point.
The adjustable volume restriction Q (14) and
Xp (gain) restriction (13) are used to opti-
mize the control loop of the positioner.
The range spring (6), which can be ex-
changed, is assigned to both the rated valve
travel and the span of the set point.
Legend for Fig. 3-1 and Fig. 3-2
1
Lever for valve travel
1.1
Shaft
2
Pin
2.1
Nut
3
Sleeve
4
Zero point adjustment
5
Fastening screw
6
Range spring
6.1
Bracket
7
Fastening screw
8
Measuring diaphragm
9
Diaphragm plate
9.1
Feeler pin
10
Nozzle block
10.1
Nozzle
10.2 Flapper plate
11
Cover plate
12
Booster
13
Xp restriction
14
Volume restriction Q
15
Hole for fastening screw
20
Plate
21
i/p converter
Summary of Contents for 4763
Page 10: ...1 6 EB 8359 2 EN...
Page 20: ...3 6 EB 8359 2 EN...
Page 36: ...5 14 EB 8359 2 EN...
Page 38: ...6 2 EB 8359 2 EN...
Page 40: ...7 2 EB 8359 2 EN...
Page 46: ...9 4 EB 8359 2 EN...
Page 48: ...10 2 EB 8359 2 EN...
Page 50: ...11 2 EB 8359 2 EN...
Page 52: ...12 2 EB 8359 2 EN...
Page 54: ...13 2 EB 8359 2 EN...
Page 56: ...14 2 EB 8359 2 EN...
Page 57: ...EB 8359 2 EN 14 3...
Page 58: ...14 4 EB 8359 2 EN...
Page 59: ...EB 8359 2 EN 14 5...
Page 60: ...14 6 EB 8359 2 EN...
Page 61: ...EB 8359 2 EN 14 7...
Page 62: ...14 8 EB 8359 2 EN...
Page 63: ...EB 8359 2 EN 14 9...
Page 64: ...14 10 EB 8359 2 EN...
Page 65: ...EB 8359 2 EN 14 11...
Page 66: ...14 12 EB 8359 2 EN...
Page 67: ...EB 8359 2 EN 14 13...
Page 68: ...14 14 EB 8359 2 EN...
Page 69: ...EB 8359 2 EN 14 15...
Page 70: ...14 16 EB 8359 2 EN...
Page 71: ...EB 8359 2 EN 14 17...
Page 72: ...14 18 EB 8359 2 EN...
Page 75: ......
Page 76: ......
Page 77: ......