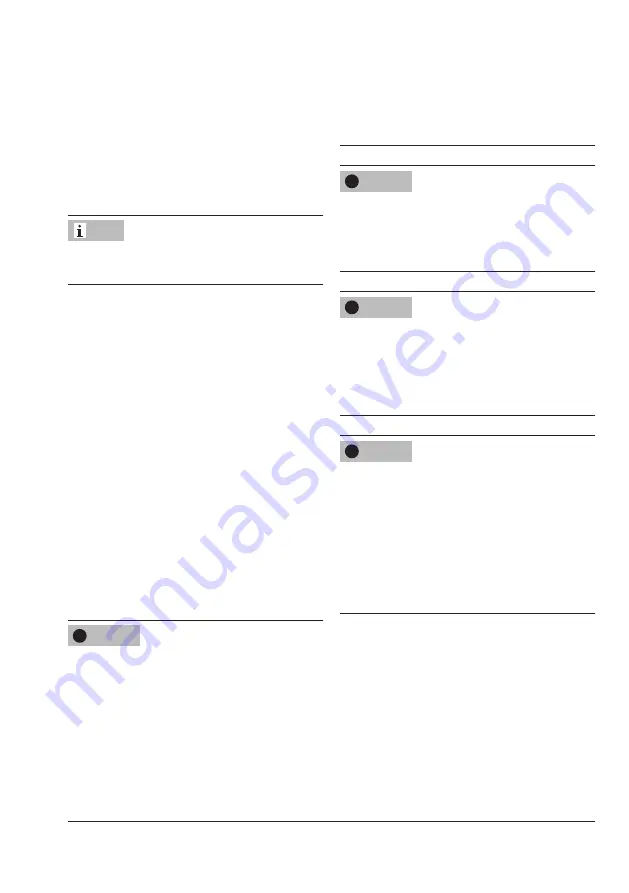
EB 8115 EN
5-3
Installation
Proceed as follows:
Î
Lay out the necessary material and tools
to have them ready during installation
work.
Î
Flush the pipelines.
The plant operator is responsible for clean-
ing the pipelines in the plant.
Î
For steam applications, dry the pipelines.
Moisture will damage the inside of the
valve.
Î
Check any mounted pressure gauges to
make sure they function properly.
Î
When the valve and actuator are al
-
ready assembled, check the tightening
torques of the bolted joints (see the
'Tightening torques' section in Annex).
Components may loosen during trans-
port.
5.3 Mounting the device
The activities listed below are necessary to
install the valve and before it can be started
up.
Risk of valve damage due to excessively
high or low tightening torques.
Observe the specified torques when tighten
-
ing control valve components. Excessive
tightening torques lead to parts wearing out
more quickly. Parts that are too loose may
cause leakage.
Î
Observe the specified tightening torques
(see 'Tightening torques' in Annex).
Risk of valve damage due to the use of un-
suitable tools.
Î
Only use tools approved by SAMSON
(see the 'Tools' section in Annex).
Risk of valve damage due to the use of un-
suitable lubricants.
Î
Only use lubricants approved by
SAMSON (see the 'Lubricants' section in
Annex).
Risk of the process medium being contami-
nated through the use of unsuitable lubri-
cants and/or contaminated tools and com-
ponents.
Î
Keep the valve and the tools used free
from solvents and grease.
Î
Make sure that only suitable lubricants
are used.
Note
NOTICE
!
NOTICE
!
NOTICE
!
NOTICE
!
Summary of Contents for 3321CT
Page 12: ...1 8 EB 8115 EN...
Page 14: ...2 2 EB 8115 EN...
Page 34: ...5 8 EB 8115 EN...
Page 38: ...7 2 EB 8115 EN...
Page 50: ...9 10 EB 8115 EN...
Page 54: ...11 2 EB 8115 EN...
Page 56: ...12 2 EB 8115 EN...
Page 58: ...13 2 EB 8115 EN...
Page 64: ...14 6 EB 8115 EN...
Page 68: ...14 10 EB 8115 EN...
Page 77: ......
Page 78: ......
Page 79: ......