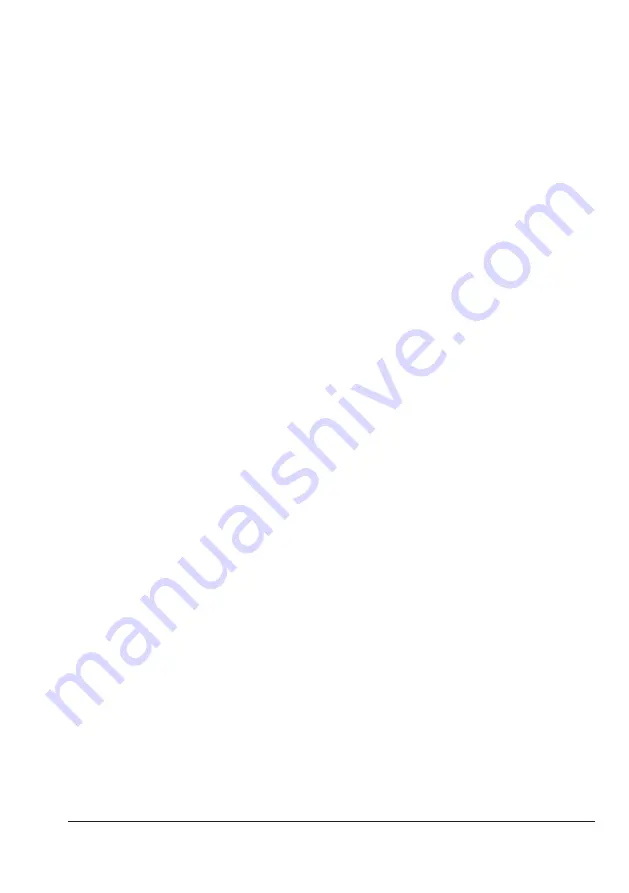
EB 5840 EN
3-1
Design and principle of operation
3
Design and principle of oper-
ation
The pneumatic actuators are used especially
for attachment to Type 3222 and Type 3213
Valves. In this case, force‑locking attachment
is used.
The actuators mainly consist of two dia‑
phragm cases, the actuator stem (A2/A5),
rolling diaphragm (A48) and springs (A25‑
29). The housings have an actuator area of
120 cm² and are made of die‑cast alumi‑
num.
The signal pressure creates a force at the di‑
aphragm surface, which is opposed by the
springs in the actuator. The direction of ac‑
tion of the actuator stem depends on how the
springs are installed in the actuator. The
springs may be fitted into one another.
The Type 2780‑2 Actuator is designed for
the direct attachment of a positioner as stan‑
dard. A yoke is located on the bottom dia‑
phragm case for attachment of a pneumatic
or electropneumatic positioner.
3.1 Direction of action
The direction of action is determined by how
the springs and diaphragm plate are ar‑
ranged in the actuator.
With direction of action "actuator stem ex‑
tends", the compressed air is applied to the
signal pressure connection on the bottom di‑
aphragm case.
With direction of action "actuator stem re‑
tracts", the compressed air is applied to the
signal pressure connection on the top dia‑
phragm case.
The actuator's direction of action can be re‑
versed (see the 'Operation' section).
3.2 Signal pressure routing
In the "actuator stem extends" version, the
signal pressure is routed through the bottom
signal pressure connection (S
FA
) to the bot‑
tom diaphragm chamber. In the "actuator
stem retracts" version, the signal pressure is
routed through the top signal pressure con‑
nection (S
FE
) to the top diaphragm chamber.
Type 2780-2x (see Fig. 3-2 and Fig. 3-3)
In the Type 2780‑2 Actuator, the signal pres‑
sure is transmitted to the diaphragm cham‑
ber through the holes (S
FA
, S
FE
) on the left or
right side of the yoke and over a
switchover
plate
. The fail‑safe action of the actuator
("actuator stem extends" or "actuator stem
retracts") determines how the positioner must
be attached and the switchover plate must
be aligned.
The switchover plate needs to be turned to
align the correct symbol for the fail‑safe ac‑
tion with the marking. The attachment either
on the left or right side of the actuator is de‑
termined by the required direction of action
of the positioner (>> or <>).
If the actuator is operated without a position‑
er, a
connecting plate
is required instead of
the switchover plate. In this case, the signal
pressure is routed directly over the signal
Summary of Contents for 2780-1
Page 12: ...2 2 EB 5840 EN...
Page 18: ...3 6 EB 5840 EN...
Page 22: ...4 4 EB 5840 EN...
Page 38: ...9 2 EB 5840 EN...
Page 42: ...11 2 EB 5840 EN...
Page 44: ...12 2 EB 5840 EN...
Page 46: ...13 2 EB 5840 EN 51 54 52 42 53 38 39 48 40 46 23 1 9 55 25 20 59 65 Type 2780 1 Actuator...
Page 49: ......
Page 50: ......
Page 51: ......