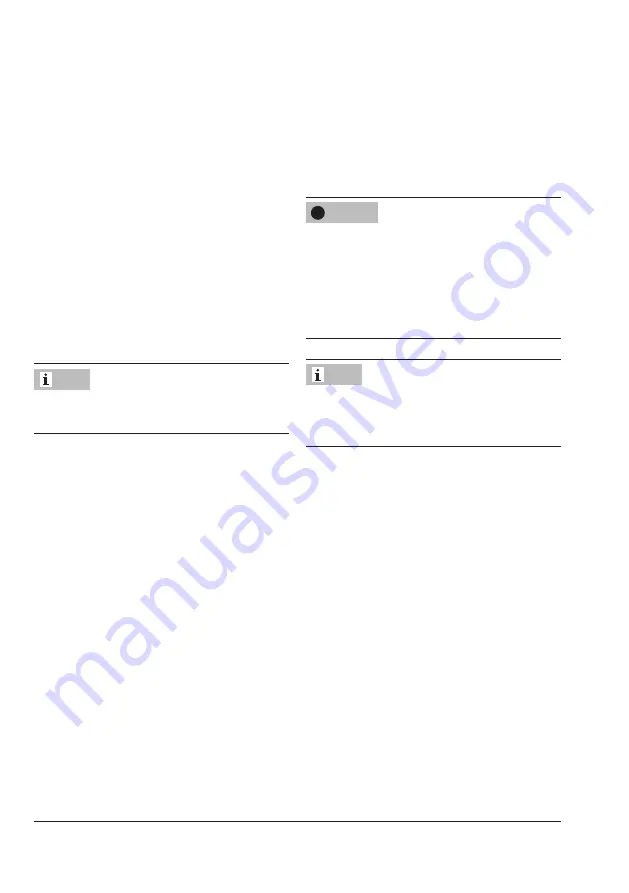
22
EB 2185 EN
Measures for preparation
4 Measures for preparation
After receiving the shipment, proceed as fol-
lows:
1. Check the scope of delivery. Compare
the shipment received with the delivery
note.
2. Check the shipment for transportation
damage. Report any damage to
SAMSON and the forwarding agent
(refer to delivery note).
4.1 Unpacking
Do not remove the packaging until immedi
-
ately before mounting it onto the valve.
Proceed as follows to lift and mount the de-
vice:
1. Remove the packaging from the device.
2. Dispose of the packaging in accordance
with the valid regulations.
4.2 Transporting and lifting
Due to the low service weight, lifting equip-
ment is not required to lift and transport the
safety temperature limiter (e.g. to mount it
onto the valve).
Transport instructions
−
Protect the device against external influ
-
ences (e.g. impact).
−
Protect the device against moisture and
dirt.
Note
−
Observe the permissible ambient tem-
peratures (see section 3.2).
4.3 Storage
Risk of damage to the safety temperature
limiter due to improper storage.
−
Observe storage instructions.
−
Avoid long storage times.
−
Contact SAMSON in case of different stor-
age conditions or long storage periods.
We recommend regularly checking the de
-
vice and the prevailing storage conditions
during long storage periods.
Storage instructions
−
Protect the safety temperature limiter
against external influences (e.g. impact).
−
Protect the device against moisture and
dirt. Store it at a relative humidity of less
than 75 %. In damp spaces, prevent
condensation. If necessary, use a drying
agent or heating.
−
Make sure that the ambient air is free of
acids or other corrosive media.
−
Observe the permissible ambient tem-
peratures (see section 3.2).
−
Do not place any objects on the device.
NOTICE
!
Note
Summary of Contents for 2439
Page 39: ...EB 2185 EN 39...