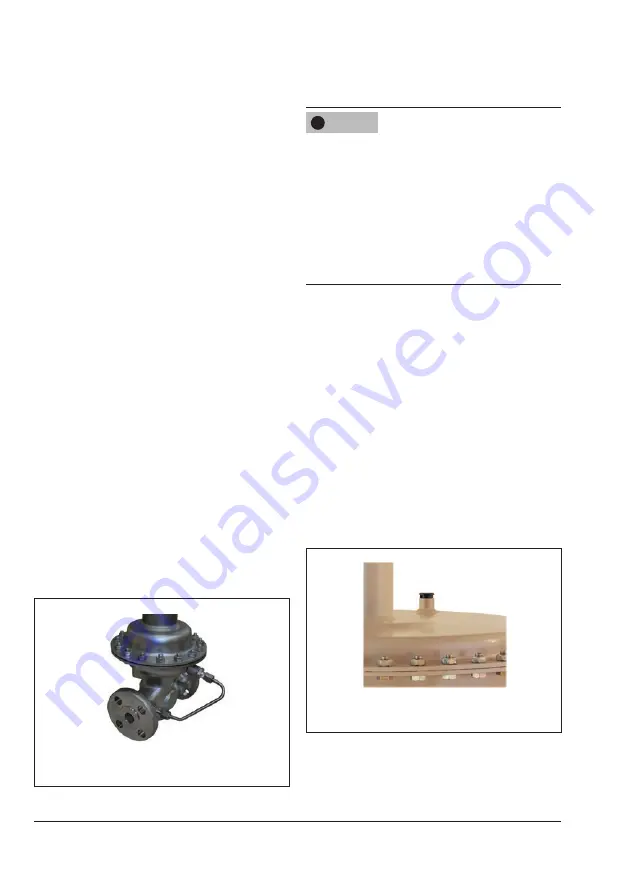
22
EB 2522 EN
Mounting and start-up
Control line
Fitting with G ¼ female thread (9) on the ac
-
tuator housing. Route the control line on site
preferably using a 6 mm or ¼“ (stainless)
steel pipe.
Always connect the control line connection
for pressure tapping (see Fig. 5) directly to
the tank or vessel as the medium is in the ex
-
panded state and no turbulence occurs at
this point.
If the pressure is to be tapped at a straight
pipeline section, the largest possible distance
to the regulator must be kept (at least 2 x
DN). Connect the control line at the side or
on top of the horizontally running main
pipeline. If possible, place the point of pres-
sure tapping in a pipe expansion.
Install any pipe fittings (e.g. restrictions,
bends, manifolds or branches), that may
cause turbulence in the flow, sufficiently far
away from the control line connection (at
least 3 x DN).
Optionally, a ready-mounted control line is
available. This option must be specified in
the order (see Fig. 8).
Fig. 8:
Control line
Regulator damage due to condensed water.
In applications in which the gas can liquefy,
condensate may form in the control line,
causing damage to the regulator. To allow
condensate to run back into the tank, install
the control line with an approximate 10 %
slope to the pressure tapping point at the
tank or pipeline (see
Leakage line connection
The regulator in the special version is deliv-
ered with a leakage line connection. In this
version, the opening to the set point adjust-
ment is additionally sealed by a cap.
Connect the leakage line to the G ¼ female
thread fitting on top of the actuator housing.
In the event of a defective diaphragm (dia-
phragm rupture) in the actuator, any process
medium that escapes is fed through a leak-
age line to a safe location.
Fig. 9:
Leakage line connection G ¼
NOTICE
!
Summary of Contents for 2406
Page 31: ...EB 2522 EN 31...