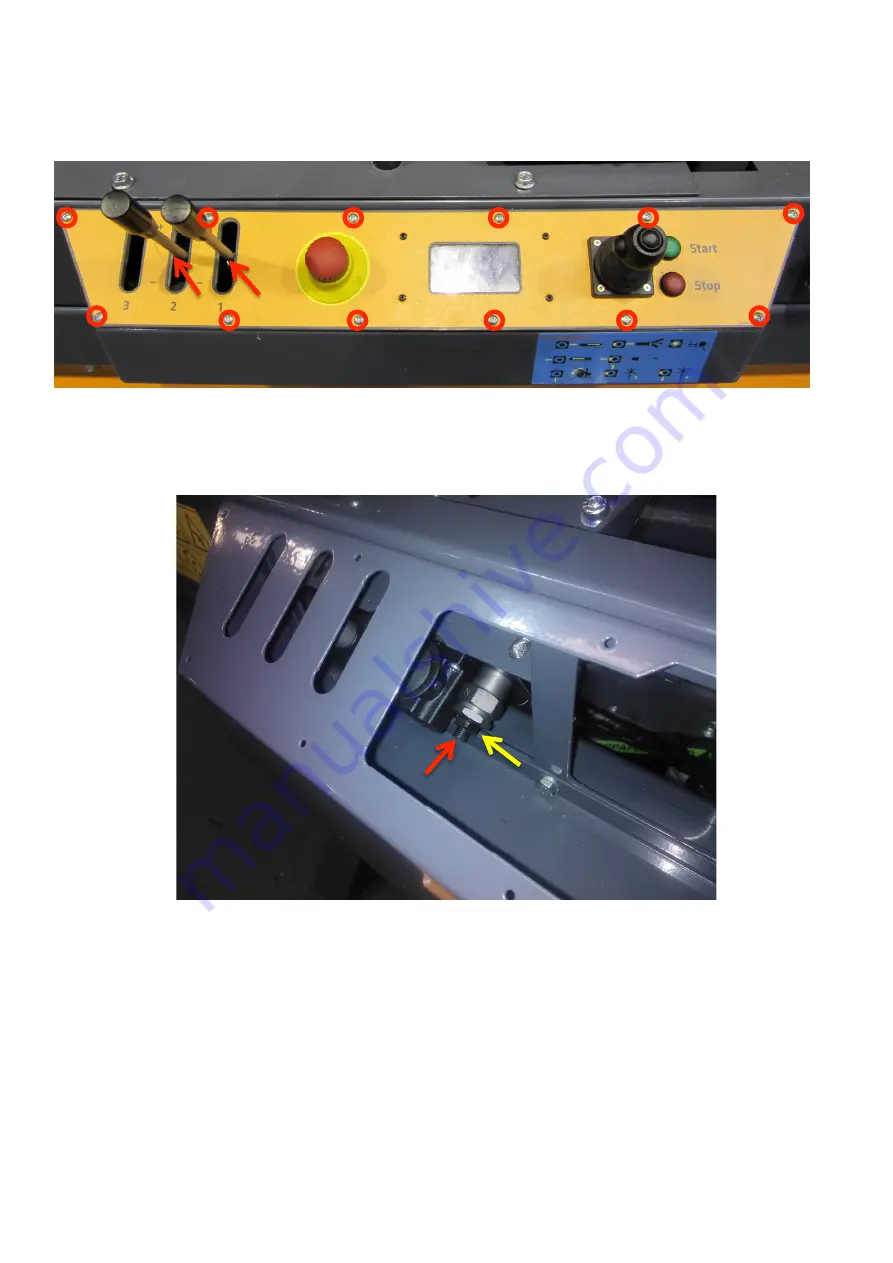
www.reikalevy.fi
12
5.2
Splitting circuit pressure adjustment
•
Unscrew control panel screws (Phillips screwdriver) and manual control valve levers.
•
Move control panel to the side.
•
Connect pressure gauge (0-‐250 bar) to the pressure test coupling marked with yellow
arrow (M16x2 thread).
•
Loosen the locknut marked with yellow arrow (13 mm wrench).
•
The adjustment screw (4 mm hex key) is marked with red arrow.
•
Turning the adjustment screw clockwise increases the pressure. Turning
counterclockwise reduces the pressure.
•
Tighten locknut after adjustment.