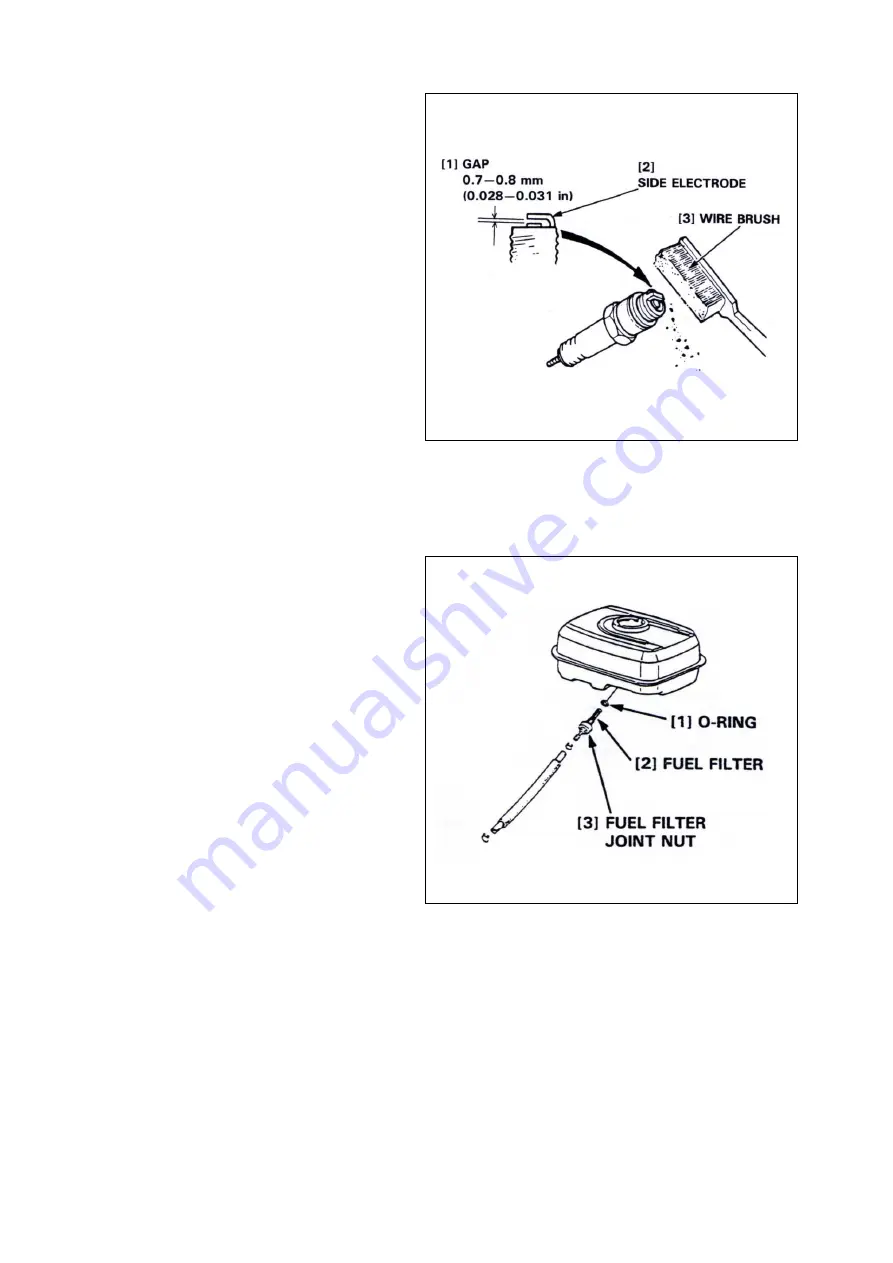
VERS.2017.06.12 C51_MAN_EN
22
Spark plug
To service the spark plug, follow these
instructions:
Visually inspect the spark plug.
Discard the plug if the insulator is
cracked or chipped.
Remove carbon or other deposits with
a stiff wire brush.
Measure the plug gap with a wire-type
feeler gauge. If necessary, adjust the
gap by bending the side electrode.
Make sure the sealing washer is in
good condition; replace the plug if
necessary.
Install the plug fingertight to seat the washer, then tighten with a plug wrench (an additional
½ turn if a new plug) to compress the sealing washer. If you are reusing a plug, tighten 1/8-
1/4 turn after the plug seats.
Fuel line
To service the fuel line, follow these
instructions:
Drain the fuel into a suitable container,
and remove the fuel tank.
Disconnect the fuel line, and unscrew
the fuel filter from the tank.
Clean the filter with solvent, and
check, that the filter screen is
undamaged.
Place the O-ring on the filter and
reinstall. Tighten the filter to 2N.m.
After reassembly, check for fuel leaks.
Further maintenance
For further maintenance, please contact the nearest engine maintenance centre.