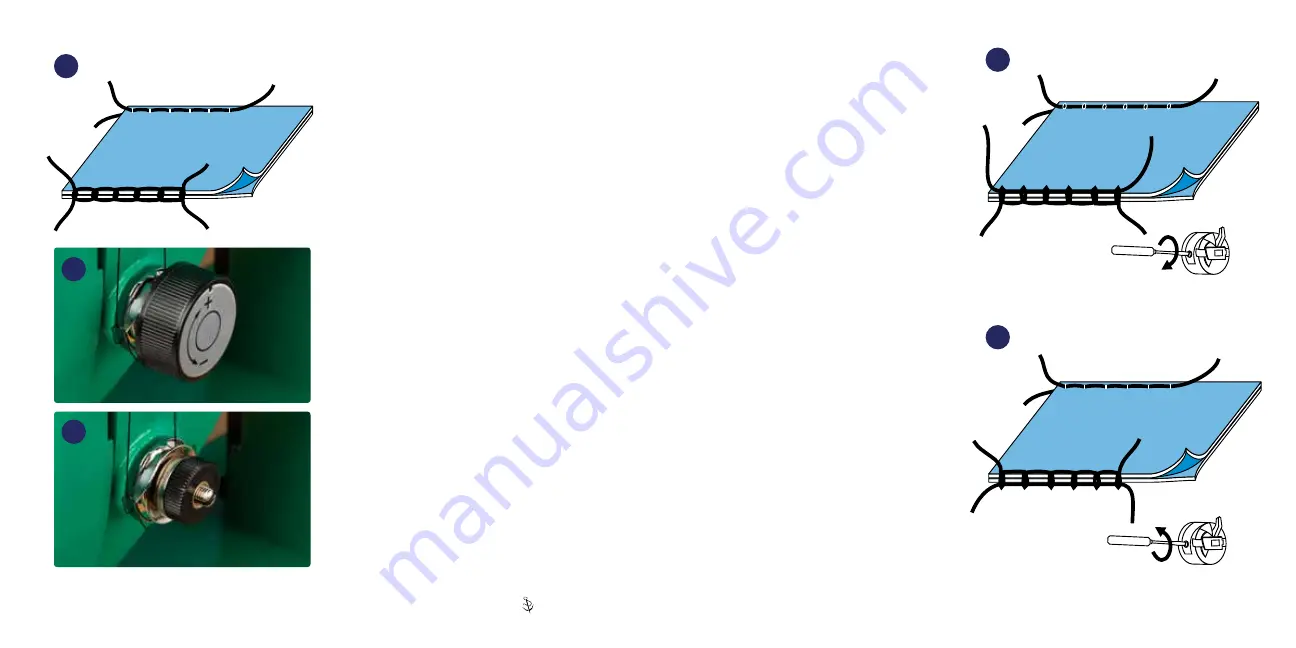
19 |
Sailrite�com
Leatherwork
®
Guidebook
| 20
Thread Tension Adjustment
The correct combination of thread tension (
21
)
results in a stitch that looks identical on both sides of
the material (i�e�, the knots of the stitches are pulled
into the fabric and are no more visible on the top
than on the bottom)�
If knots are visible on both the top and bottom
material surfaces, this is an indication that the thread
size is too large for the material being sewn�
The upper tension knob (
22
) can be loosened
or tightened to adjust tension� Rotating the knob
clockwise or toward the “+” will increase upper
tension, pulling the knot to the top of the sewn
application (
24
)� Rotating the knob counterclockwise
or toward the “-” will decrease upper tension,
allowing the knot to be pulled to the bottom of the
sewn application (
25
)�
When the presser foot is lifted, the upper tension
disks are pushed apart� This releases the top thread
tension so leather can be removed from under the
machine foot without fighting thread tension.
DO NOT
lift the presser foot when the upper tension
knob is less than a 1/2 turn from maximum (turned
snugly clockwise) (
23
)� This amount of tension
should never be required�
If upper tension is tightened all the way down,
raising the presser foot may bend the lever inside
the machine that separates the disks, preventing the
disks from opening correctly�
Knots centered — PERFECT STITCH
22
23
21
NOTE: Decorative cap removed�
Knots visible on bottom
Knots pulled to top
24
25
Advanced Thread
Tension Adjustment
Before moving on, please reference
p� 6 to ensure proper needle and
thread size are being used for your
application�
Tension changes to the bobbin thread should
only be made when upper tension changes alone
do not solve stitch tension� In general, bobbin
tension requires just about a 2 ounce drag on
the thread (similar to what you feel when pulling
dental floss off a spool).
If knots are pulled to the top (
24
) and you can’t
loosen the upper tension knob (
22
) any more,
remove the bobbin case from the machine and
increase the bobbin case tension by tightening
the tension adjustment screw (p� 14,
I
)� Tighten
in 1/4 increments, testing the drag on the
thread after each 1/4 turn until proper tension
is achieved�
If the knots are pulled to the bottom (
25
) and
you can’t tighten the upper tension knob (
22
)
any more, remove the bobbin case from the
machine and decrease the bobbin case tension by
loosening the tension adjustment screw (p� 14,
I
)�
Loosen in 1/4 increments, testing the drag on the
thread after each 1/4 turn until proper tension is
achieved�
Summary of Contents for Leatherwork
Page 1: ......