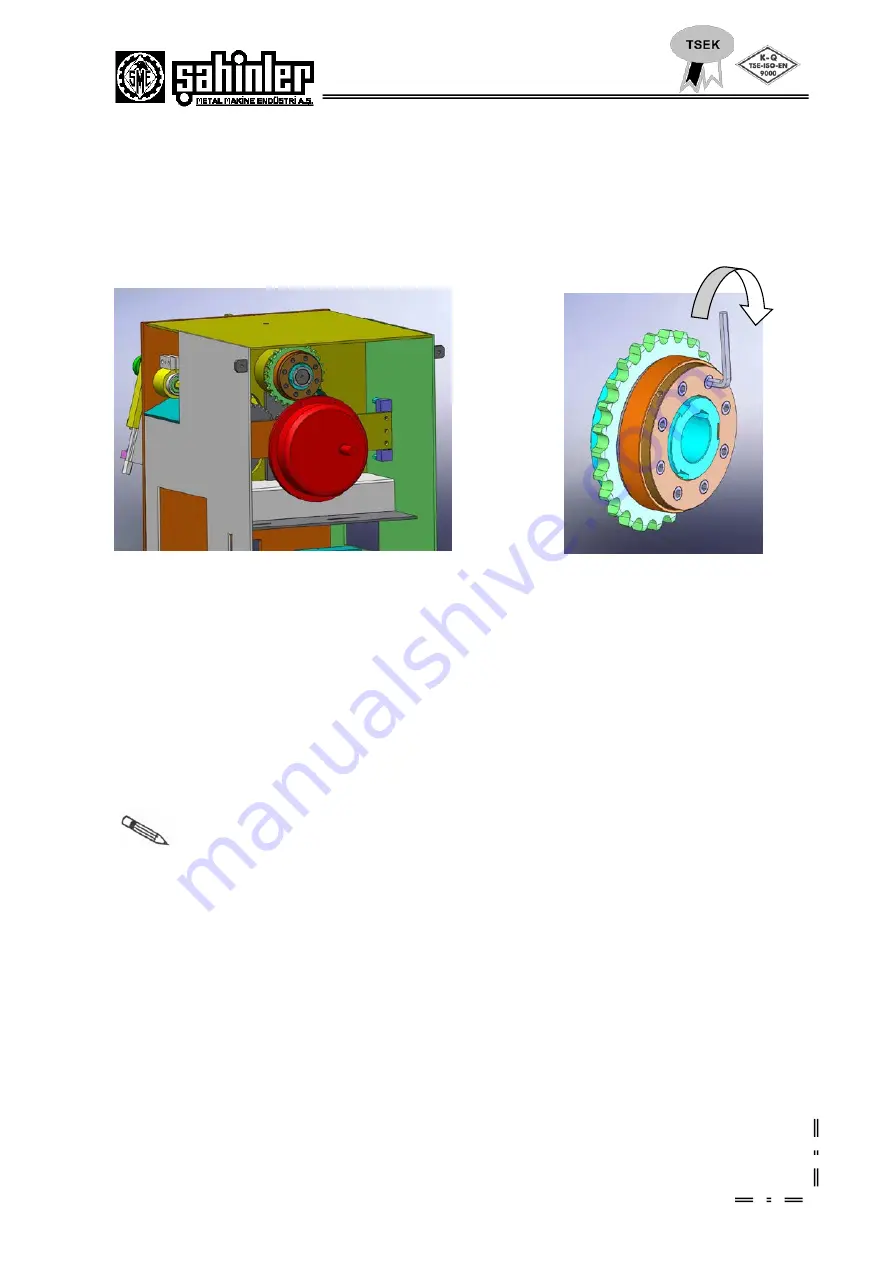
16
Clutch System;
If the top roll stops, while lower rolls are turning, than the pressure springs must be tightened a
bit. To make this you have to screw the setscrews shown in Step2.
The balance of the clutch system is shown below step by step.
Step1
Step2
1.
Open the back cover.
2.
Screw them through arrow direction with an ally key.(6)
Note : Keep to tighten it until top roll begins to turn.
Summary of Contents for HPK 665
Page 11: ...9 Note Always leave necessary safety distance Figure 3 Figure 4...
Page 29: ...26...
Page 30: ......
Page 31: ...26 HYDRAULIC PLAN FOR HPK 65...
Page 32: ......
Page 34: ......
Page 36: ......
Page 38: ......
Page 41: ......
Page 43: ......