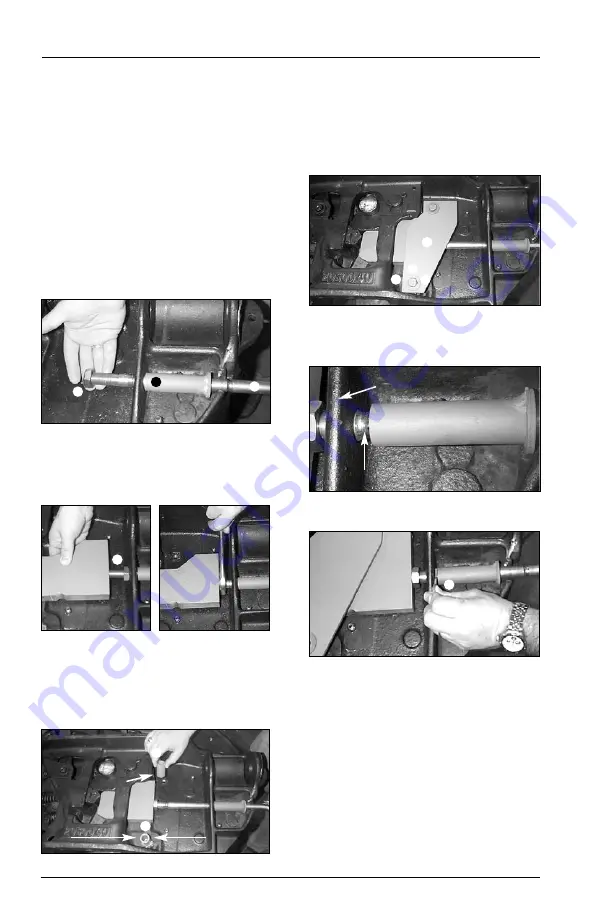
20
XL-FW503 Rev B
MANUAL SLIDING SECONDARY LOCK
Rebuilding Instructions
If your fifth wheel is equipped with the
manual sliding secondary lock, then
rebuild per standard FleetMaster
Rebuilding Instructions (XL-FW355-XX),
but replace the Manual Secondary Lock
Installation (as stated on Page 7 of
XL-FW355-XX) with the following:
Note:
During assembly, use threadlocker
(Permalok MM118, Loctite No. 243, or
equivalent on all threads.
1. Insert handle through guide sub-
assembly and install jam nut on
handle rod (
Figure 3 – Items 1, 2 & 11
).
2. Screw handle into threaded safety
bar making sure handle grip is
oriented towards ramps of wheel and
tighten jam nut (
Figure 4 & Figure 5
)
(
Item 3
).
3. Position spacer tubes over threaded
holes in casting. These spacers come
in two different lengths, so be sure to
place shorter spaced on the raised
portion of casting (
Figure 6
) (
Items 4
& 5
).
4. Position cover on spacers and use
two 1/2˝ washer, two 1/2˝ lock
washer, and two 1/2˝ x 2-3/4˝ bolts,
to fasten cover to casting (
Figure 7
)
(
Items 6, 7, 8, & 9
). Tighten fasteners.
5. Pull secondary lock handle out so
that detent on handle is between
casting rib and guide tube (
Figure 8
).
6. Install spring clip on handle (
Figure
9
) (
Item 10
).
7. Check the manual sliding secondary
lock for proper operation by
pulling/pushing handle to engage
secondary locking bar. Handle
should engage detent when
secondary locking bar is behind
primary lock and also engage detent
when pulled out to allow
uncoupling.
Figure 4
Figure 5
Figure 6
Figure 7
Figure 8
Figure 9
Detent
Raised
Portion
➂
➍
➎
➐
➏
➇
➓
Long Spacer
Short Spacer
Rib
➒
Figure 3
➊
➁
11
Summary of Contents for FleetMaster LowLube Series
Page 21: ...XL FW503 Rev B 21...
Page 22: ...22 XL FW503 Rev B...