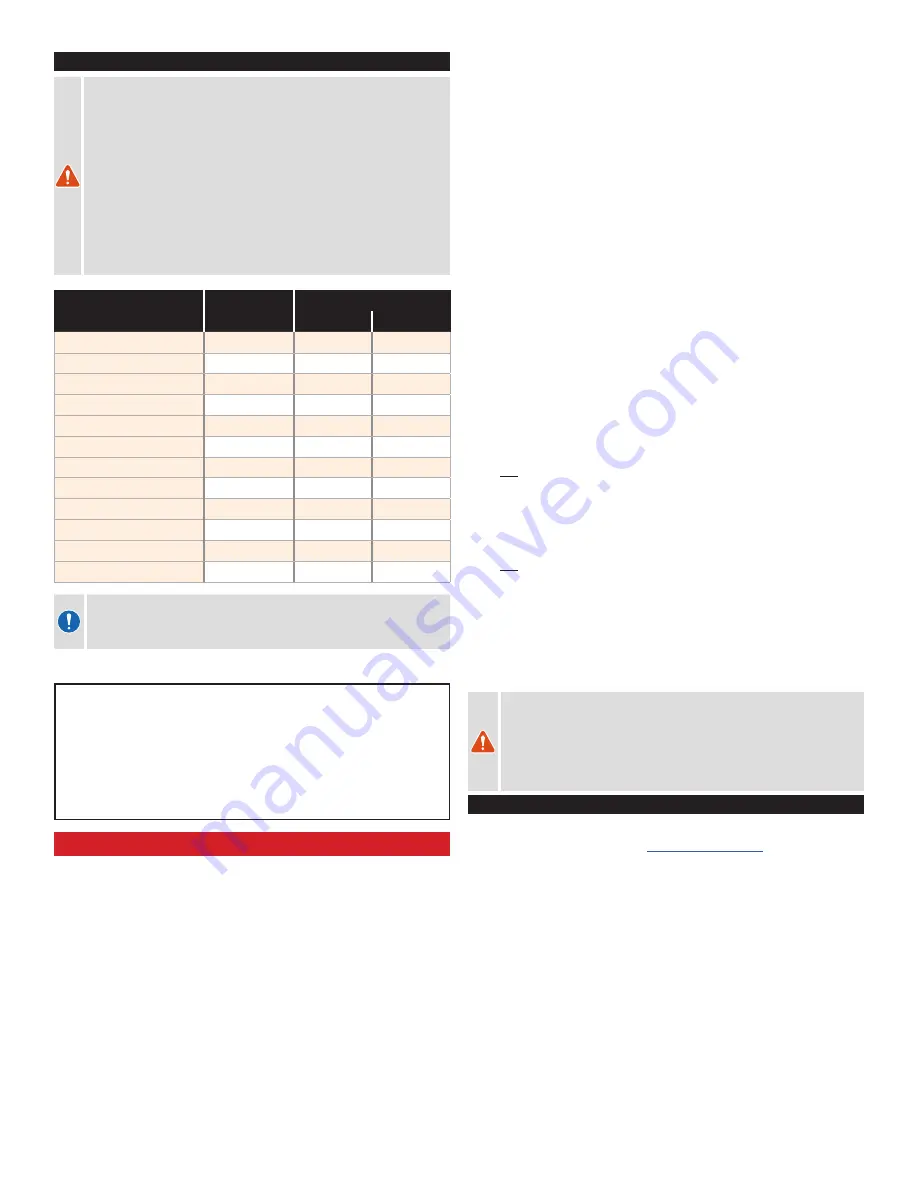
2
TOOLS / TORQUE SPECS
WARNING! Correct tightening force on fasteners (nuts, bolts,
screws) on your bicycle is important for your safety. If too
little force is applied, the fastener may not hold securely. If
too much force is applied, the fastener can strip threads,
stretch, deform or break. Either way, incorrect tightening force
can result in component failure, which can cause you to lose
control and fall.
Where indicated, ensure that each bolt is torqued to
specification. After your first ride, and consistently thereafter,
recheck the tightness of each bolt to ensure secure attachment
of the components. The following is a summary of torque
specifications in this manual:
LOCATION
ALLEN KEY
TORQUE
in-lbf
Nm
SADDLE @ RAIL CLAMP
5
120
13.5
SEAT COLLAR
4
55
6.2
STEM
4
44
5.0
STEM COVER
2
1
0.12
DERAILLEUR HANGER
4
40
4.5
FRONT/REAR AXLE
6
133
15
SEATPOST Di2 COVER
2.5
7
0.8
WATER BOTTLE
3
25
2.8
STACK BOLTS
5
44
5.0
EXTENSION SOCKET
2.5
22
2.5
ARMREST CUPS
3
26.5
3.0
BLIP BOX
2.5
9
1.0
CAUTION: Ensure that all contact surfaces are clean and bolt
threads are greased or have a threadlocking compound (refer
to the instructions for each bolt) prior to installation.
The following tools are required for installation of this product:
2, 2.5, 3, 4, 5, 6mm socket-style Allen keys
Torque wrench
High-quality grease
Cable housing cutters
Carbon assembly compound (fiber paste)
Blue threadlocker
GENERAL NOTES ABOUT MAINTENANCE
The Shiv TT is a high performance bicycle. All regular maintenance,
troubleshooting, repair and parts replacement must be performed by
an Authorized Specialized Retailer. For general information regarding
maintenance of your bicycle, please refer to the Owner’s Manual. In addition,
routinely perform a mechanical safety check before each ride, as described in
the Owner’s Manual.
Great care should be taken to not damage carbon fiber or composite
material. Any damage may result in a loss of structural integrity, which
may result in a catastrophic failure. This damage may or may not be
visible in inspection. Before each ride, and after any crash, you should
carefully inspect your bicycle for any fraying, gouging, scratches through
the paint, chipping, bending, or any other signs of damage. Do not ride
if your bicycle shows any of these signs. After any crash, and before you
ride any further, take your bicycle to an Authorized Specialized Retailer
for a complete inspection.
While riding, listen for any creaks, as a creak can be a sign of a problem
with one or more components. Periodically examine all surfaces in bright
sunlight to check for any small hairline cracks or fatigue at stress points,
such as welds, seams, holes, and points of contact with other parts. If
you hear any creaks, see signs of excessive wear, discover any cracks,
no matter how small, or any damage to the bicycle, immediately stop
riding the bicycle and have it inspected by your Authorized Specialized
Retailer.
Lifespan and the type and frequency of maintenance depends on
many factors, such as frequency and type of use, rider weight, riding
conditions and/or impacts. Exposure to harsh elements, especially salty
air (such as riding near the ocean or in the winter), can result in galvanic
corrosion of components such as the crank spindle and bolts, which
can accelerate wear and shorten the lifespan. Dirt can also accelerate
wear of surfaces and bearings. The surfaces of the bicycle should
be cleaned before each ride. The bicycle should also be maintained
regularly by an Authorized Specialized Retailer, which means it should be
cleaned, inspected for signs of corrosion and/or cracks and lubricated.
If you notice any signs of corrosion or cracking on the frame or any
component, the affected item must be replaced.
Regularly clean and lubricate the drivetrain according to the drivetrain
manufacturer’s instructions.
Do
not
use a high pressure water spray directly on the bearings. Even
water from a garden hose can penetrate bearing seals and crank
interfaces, which can result in increased bearing and crank wear, which
can affect the normal function of the bearings. Use a clean, damp cloth
and bicycle cleaning agents for cleaning.
Do
not
expose the bicycle to prolonged direct sunlight or excessive heat,
such as inside a car parked in the sun or near a heat source such as a
radiator.
When placing the frame and/or bicycle in a repair stand, clamp the
stand to the seatpost and not the frame. Clamping the frame can cause
damage to the frame that may or may not be visible, which may impair
the structural integrity of the frame.
WARNING! Failure to follow the instructions in this section may
result in damage to the components on your bicycle and will
void your warranty, but, most importantly, may result in serious
personal injury or death. If your bicycle exhibits any signs of
damage, do not use it and immediately bring it to your Authorized
Specialized Retailer for inspection.
WARRANTY
Warranty information is available from your Authorized Specialized Retailer.
It is also available for download at