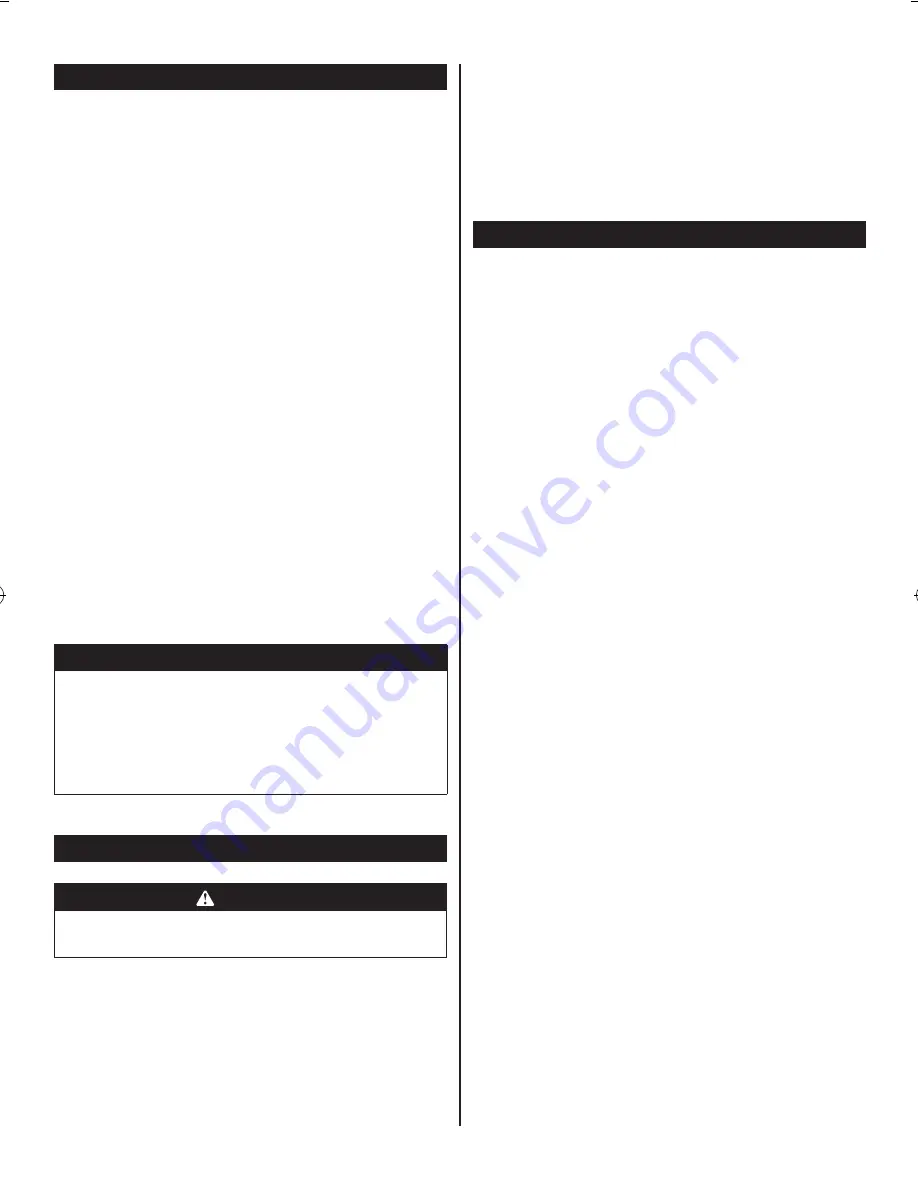
4
LUBRICATION
An automatic in-line filter-regulator-lubricator is
recommended (Fig. 7) as it increases product life and
keeps the product in sustained operation. The in-line
lubricator should be regularly checked and filled with air
tool oil.
Proper adjustment of the in-line lubricator is performed by
placing a sheet of paper next to the exhaust ports and
holding the throttle open for approximately 30 seconds.
The lubricator is properly set when a light stain of oil
collects on the paper. Excessive amounts of oil should be
avoided.
If it becomes necessary to store the product for an extended
period of time (overnight, weekend, etc.), it should receive
a generous amount of lubrication at that time. The product
should be run for approximately 30 seconds to ensure oil
has been evenly distributed throughout the product. The
product should be stored in a clean and dry environment.
●
It is most important that the product be properly
lubricated by keeping the air line lubricator filled
and correctly adjusted. Without proper lubrication
the product will not work properly and parts will
wear prematurely.
●
Use correct lubricant in the air line lubricator. The
lubricator should be of low air flow or changing air
flow type, and should be kept filled to the correct
level. Use only recommended lubricants, specially
made for pneumatic applications. Substitutes
may harm the rubber compounds in the product's
O-rings and other rubber parts.
IMPORTANT!
See Figure 7.
If a filter/regulator/lubricator is not installed on the air
system, air operated tools should be lubricated at least
once a day or after 2 hours of work with 2 - 6 drops
of oil, depending on the work environment, directly
through the male fitting in the tool housing.
LOADING AND OPERATION
WARNING
Drain the air tank daily. Water in the air line will damage
the tool.
■
Air tools should not be used in a potentially explosive
environment.
■
Only polishing and sanding inserted tools as
recommended by the manufacturer of the product are
used.
■
Clean the air inlet filter weekly.
■
Line pressure should be increased to compensate for
unusually long air hoses (over 8 metres). The minimum
hose diameter should be 6.35 mm (1/4”) I.D. and the
fittings must have the same inside dimensions.
■
Keep hose away from heat, oil and sharp edges. Check
hose for wear, and make sure that all connections are
secure.
■
Use the tool only for its intended purpose.
MAINTENANCE
■
Keep the product safe by regular maintenance.
■
Check that the maximum operating speed of the
accessories is higher than the rated speed of the tool.
■
Personal protective safety glasses shall be used;
gloves and protective clothing are recommended.
■
Personal protection and dust collection device shall be
chosen with regard to the material being worked upon.
■
Release the start and stop device in case of energy
supply failure.
■
No spare parts are to be used when these affect the
health and safety of operators.
■
Always keep your air tool clean and lubricated. Daily
lubrication is essential to avoid internal corrosion and
possible failure.
■
Lubricate the tool daily with a few drops of air tool oil
dripped into the air inlet.
■
Maintenance shall be performed weekly.
■
Drain the air tank daily. Water in the air line will
damage the product.
■
If the product cannot be used anymore, make sure to
dispose of it so as not to impose hazards on people
and the environment.
■
Air tool white oil is recommended for lubrication.
■
Only lubricants recommended by the manufacturer
should be used.
■
Loss of power or erratic action may be due to the
following:
– Excessive drain on the air line. Moisture or
restriction in the air pipe. Incorrect size or type of
hose connectors. To remedy check the air supply.
– Grit or gum deposits in the tool may also reduce
performance. If your model has an air strainer
(located in the area of the air inlet), remove the
strainer and clean it.
■
When not in use, disconnect from air supply, clean
tool and store in a safe, dry, childproof location. If the
tool cannot be used anymore, make sure to dispose
of it so as not to impose hazards to people and the
environment.
■
Check the speed after each service in relevant cases.