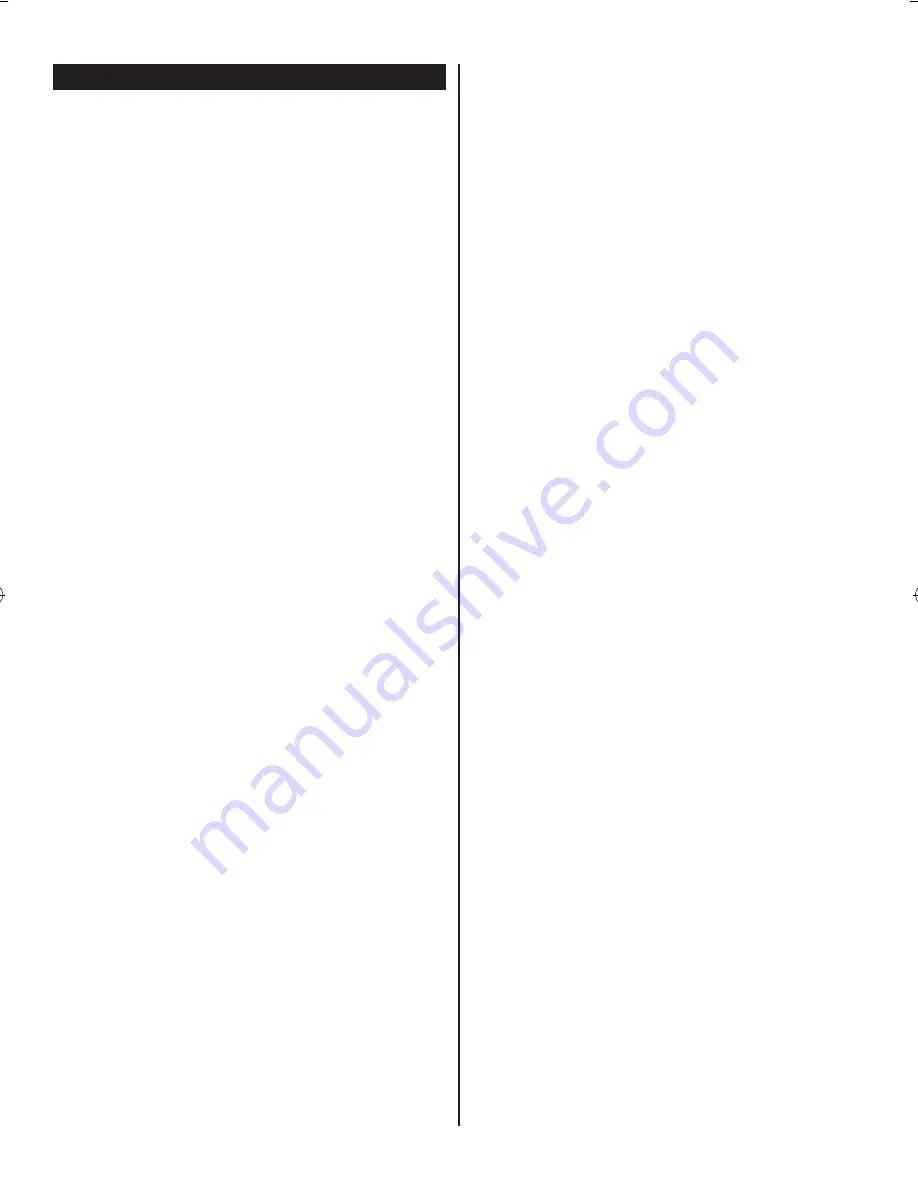
1
GENERAL SAFETY RULES
■
For multiple hazards, read and understand the safety
instructions before installing, operating, repairing,
maintaining, changing accessories on, or working
near, the drill or tapper. Failure to do so can result in
serious bodily injury.
■
Only qualified and trained operators should install,
adjust or use the drill or tapper.
■
Do not modify this drill or tapper. Modifications can
reduce the effectiveness of safety measures and
increase the risks to the operator.
■
Do not discard the safety instructions; give them to the
operator.
■
Do not use the drill or tapper if it has been damaged.
■
Tools shall be inspected periodically to verify that the
ratings and markings required by this part of ISO 11148
are legibly marked on the tool. The employer/user
shall contact the manufacturer to obtain replacement
marking labels when necessary.
PROJECTILE HAZARDS
■
Be aware that the failure of the work piece, or
accessories, or even of the inserted tool itself, can
generate high-velocity projectiles.
■
Always wear impact-resistant eye protection during the
operation of the drill or tapper. The grade of protection
required should be assessed for each use.
■
Remove the chuck key before drilling starts.
■
Ensure that the work piece is securely fixed.
ENTANGLEMENT HAZARDS
Choking, scalping and/or lacerations can occur if loose
clothing, personal jewelry, neck wear, hair or gloves are
not kept away from the tool and accessories.
OPERATING HAZARDS
■
Use of the tool can expose the operator’s hands to
hazards, including cuts, abrasions and heat. Wear
suitable gloves to protect hands.
■
Operators and maintenance personnel shall be
physically able to handle the bulk, weight and power
of the tool.
■
Hold the tool correctly; be ready to counteract normal
or sudden movements and have both hands available.
■
Maintain a balanced body position and secure footing.
■
High-reaction torque can be developed in the case
of stalling, which can be caused by excessive loads
being applied to the drill bit, by the drill bit snagging on
the material being drilled into or by the drill bit breaking
through the material being drilled.
■
In cases where the means to absorb the reaction
torque are requested, it is recommended to use a
suspension arm whenever possible. If that is not
possible, side handles are recommended for straight
case tools and pistol-grip tools. In any case, it is
recommended to use a means to absorb the reaction
torque above 4 Nm for straight tools and above 10 Nm
for pistol-grip tools.
■
Keep hands away from the rotating chuck and drill bit.
■
Release the start-and-stop device in the case of an
interruption of the energy supply.
■
Use only lubricants recommended by the manufacturer.
■
Personal protective safety glasses shall be
used; suitable gloves and protective clothing are
recommended.
REPETITIVE MOTIONS HAZARDS
■
When using a drill or tapper to perform work-related
activities, the operator can experience discomfort in
the hands, arms, shoulders, neck or other parts of the
body.
■
While using a drill or tapper, the operator should
adopt a comfortable posture while maintaining a
secure footing and avoiding awkward or off-balanced
postures. The operator should change posture during
extended tasks, which can help avoid discomfort and
fatigue.
■
If the operator experiences symptoms, such as
persistent or recurring discomfort, pain, throbbing,
aching, tingling, numbness, burning sensations or
stiffness, these warning signs should not be ignored.
The operator should tell the employer and consult a
qualified health professional.
ACCESSORY HAZARDS
■
Disconnect the drill or tapper from the energy
supply before fitting or changing the inserted tool or
accessory.
■
Use only sizes and types of accessories and
consumables that are recommended by the drill or
tapper manufacturer; do not use other types or sizes
of accessories and consumables.
■
Avoid direct contact with the inserted tool during and
after use, as it can be hot or sharp.
WORKPLACE HAZARDS
■
Slips, trips and falls are major causes of workplace
injury. Be aware of slippery surfaces caused by the
use of the tool and also of trip hazards caused by the
air line or hydraulic hose.
■
Proceed with care in unfamiliar surroundings. There
can be hidden hazards, such as electricity or other
utility lines.
■
The drill or tapper is not intended for use in potentially
explosive atmospheres and is not insulated against
coming into contact with electric power.
■
Ensure that there are no electrical cables, gas pipes,
etc., that can cause a hazard if damaged by use of
the tool.