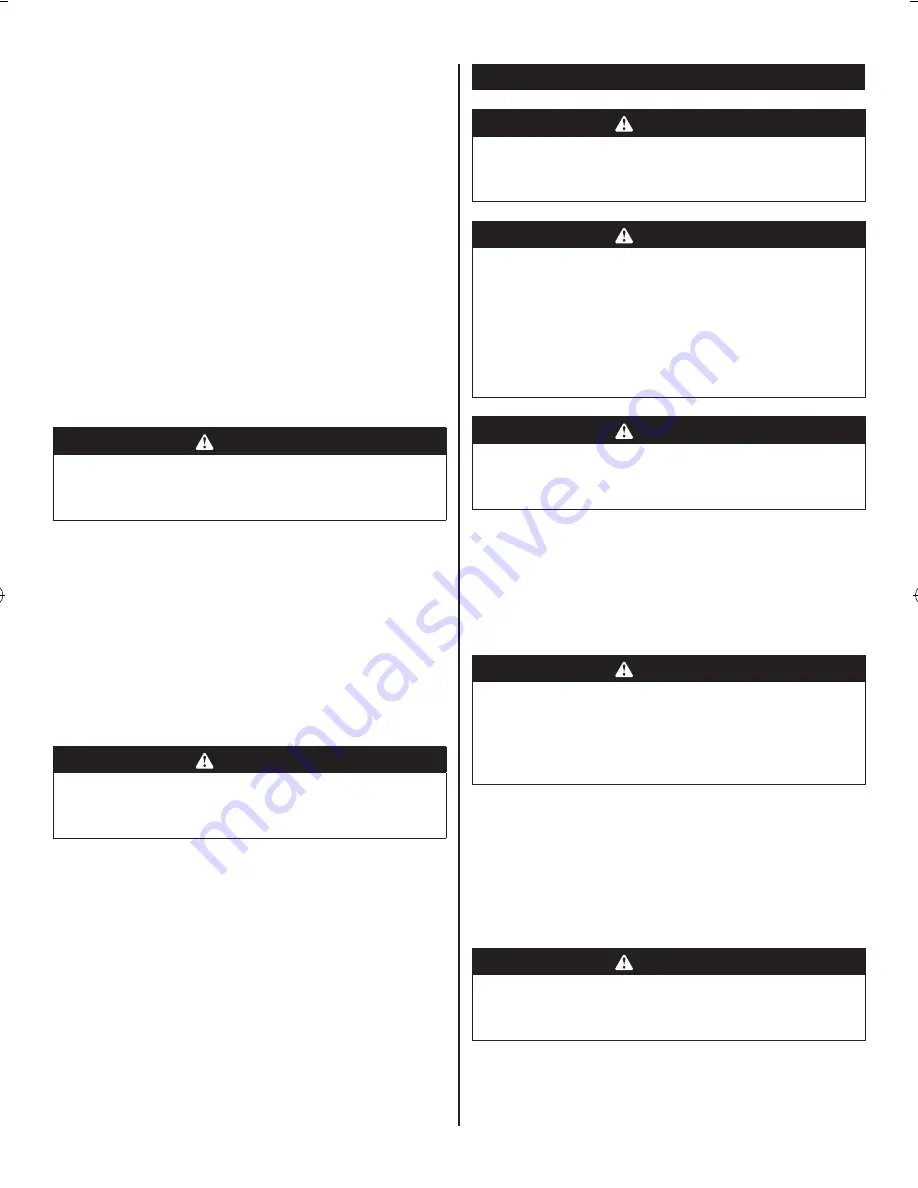
7
2. Less noise will be produced,
3. A reduction in fastener driving tool wear will be
achieved.
The amount of air pressure required will depend on the
size of the fastener and the workpiece material.
Begin testing the depth of drive by driving a test fastener
into the same type of workpiece material used for the
actual job.
Drive a test fastener with the air pressure set at 6.2 - 6.5
bar (90 - 95 psi). Raise or lower the air pressure to find
the lowest setting that will perform the job with consistent
results.
It may be possible to achieve the desired depth with air
pressure adjustments alone.
REMOVINg FAStENERS FROM thE tOOl
See figure 6.
1. Disconnect the tool from the air supply.
WARNINg
Disconnect the tool from the air supply and empty the
magazine before performing maintenance. Failure to do
so could result in serious personal injury.
2. To remove a strip of fasteners from the tool, release
the magazine lock and slide open the magazine.
3. Remove the fasteners from the magazine.
NOtE:
Always keep fingers clear of fastener track of
magazine to prevent injury from unintended release of the
pusher.
4. Close the magazine.
clEARINg A jAMMED FAStENER
See figure 7.
WARNINg
Disconnect the tool from the air supply and empty the
magazine before clearing a jammed fastener. Failure to
do so could result in serious personal injury.
If a fastener becomes jammed in the tool, disconnect the
air hose and keep the tool pointed away from you while
clearing the jam.
1. Disconnect the tool from the air supply.
2. Remove fasteners from the tool.
3. Insert a flat blade screwdriver into the driving
mechanism and push the driver mechanism back,
freeing the fastener jam.
4. Remove the jammed fastener.
5. Close the magazine.
6. Reconnect the tool to the air supply.
7. Reinstall fasteners.
MAINtENANcE
WARNINg
When servicing use only identical replacement parts.
Use of any other parts may create a hazard or cause
product damage.
WARNINg
Always wear eye protection with side shields marked to
comply with one of the following standards:
● Australian Standard – AS/NZS 1337
● European Standard – CE EN166
● American Standard – ANSI Z87.1
Failure to do so could result in objects being thrown into
your eyes resulting in possible serious injury.
WARNINg
Disconnect the tool from the air supply and empty the
magazine before performing maintenance. Failure to do
so could result in serious personal injury.
gENERAl MAINtENANcE
Avoid using solvents when cleaning plastic parts. Most
plastics are susceptible to damage from various types of
commercial solvents and may be damaged by their use.
Use clean cloths to remove dirt, dust, oil, grease, etc.
WARNINg
Do not at any time let brake fluids, gasoline, petroleum-
based products, penetrating oils, etc., come in contact
with plastic parts. Chemicals can damage, weaken or
destroy plastic which may result in serious personal
injury.
cOlD WEAthER OpERAtION
For cold weather operation, near and below freezing,
the moisture in the air line may freeze and prevent tool
operation. We recommend the use of air tool lubricant or
permanent antifreeze (ethylene glycol) as a cold weather
lubricant.
WARNINg
Do not store tools in a cold weather environment to
prevent frost or ice formation on the tools’ operating
valves and mechanisms that could cause tool failure.
NOtE:
Some commercial air line drying liquids are harmful
to “O” rings and seals. Do not use these low temperature
air dryers without checking compatibility.