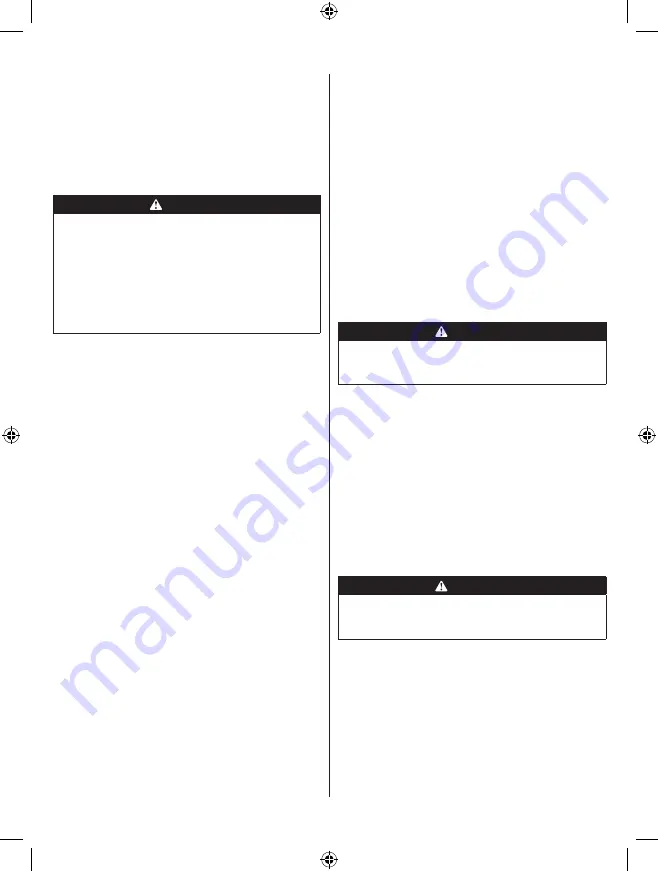
7
2. Grip the tool firmly to maintain control. Position the
safety yoke of the tool onto the work surface.
3. Push the tool against the work surface to depress the
safety yoke.
4. Squeeze the trigger to drive a fastener.
5. Allow the tool to recoil away from the work surface as
the fastener is driven.
6. Always remove your finger from the trigger after the
fastener has been driven.
wARNINg
During normal use the tool will recoil immediately
after driving a fastener. this is a normal function of
the tool.
Do not attempt to prevent the recoil by holding
the tool against the work. Restriction to the recoil can
result in a second fastener being driven from the tool.
Grip the handle firmly, let the tool do the work, and do
not place second hand on top of tool or near exhaust
at any time. Failure to heed this warning can result in
serious personal injury.
settINg the AIR pRessURe
Having checked that the fastener driving tool is functioning
correctly, apply the tool to a work piece and actuate the
trigger.
Check whether the fastener has been driven into the work
piece in accordance with the requirements.
● If the fastener is protruding, increase the air
pressure in increments of 0.5 bar, checking the
result after each new adjustment;
● If the fastener is driven into an excessive depth,
reduce the air pressure in increments of 0.5 bar
until the result is satisfactory.
● It is preferred to adjust the depth adjustment knob
to reach the good fastening effect.
Work with the lowest possible air pressure. This will give
you three significant advantages;
1. Energy will be saved,
2. Less noise will be produced,
3. A reduction in fastener driving tool wear will be
achieved.
The amount of air pressure required will depend on the
size of the fastener and the workpiece material.
Begin testing the depth of drive by driving a test fastener
into the same type of workpiece material used for the
actual job.
Drive a test fastener with the air pressure set at 6.2 - 6.5
bar (90 - 95 psi). Raise or lower the air pressure to find
the lowest setting that will perform the job with consistent
results.
It may be possible to achieve the desired depth with air
pressure adjustments alone. If finer adjustments are
needed, use the drive depth adjustment on the tool.
DRIve Depth ADjUstMeNt
See figure 7.
The driving depth of the fastener may be adjusted. It
is advisable to test the depth on a scrap workpiece to
determine the required depth for the application.
To determine depth of drive, first adjust the air pressure
and drive a test fastener. To achieve the desired depth,
use the drive depth adjustment on the tool.
1. Disconnect the tool from the air supply.
2. Turn the depth adjustment knob left or right to change
the driving depth.
3. Reconnect the tool to the air supply.
4. Drive a test fastener after each adjustment until the
desired depth is set.
ReMOvINg FAsteNeRs FROM the tOOl
See figure 8.
1. Disconnect the tool from the air supply.
wARNINg
Disconnect the tool from the air supply and empty the
magazine before performing maintenance. Failure to do
so could result in serious personal injury.
2. To remove a strip of fasteners from the tool, retract the
pusher until it reaches the end of the magazine. Hold
the pusher in place.
NOte:
Always keep fingers clear of fastener track of
magazine to prevent injury from unintended release of the
pusher.
3. Holding your left hand underneath the rear of the
magazine, tilt the tool up so that the hose connector
faces down. The fasteners will slide back and exit the
rear of the magazine.
cleARINg A jAMMeD FAsteNeR
See figure 9.
wARNINg
Disconnect the tool from the air supply and empty the
magazine before clearing a jammed fastener. Failure to
do so could result in serious personal injury.
If a fastener becomes jammed in the tool, disconnect the
air hose and keep the tool pointed away from you while
clearing the jam.
1. Disconnect the tool from the air supply.
2. Remove fasteners from the tool.
3. Pull up on the latch and open the jam release.
4. Insert a flat blade screwdriver into the driving
mechanism and push the driver mechanism back,
freeing the fastener jam.
5. Remove the bent fastener.
6. Close the jam release and latch.