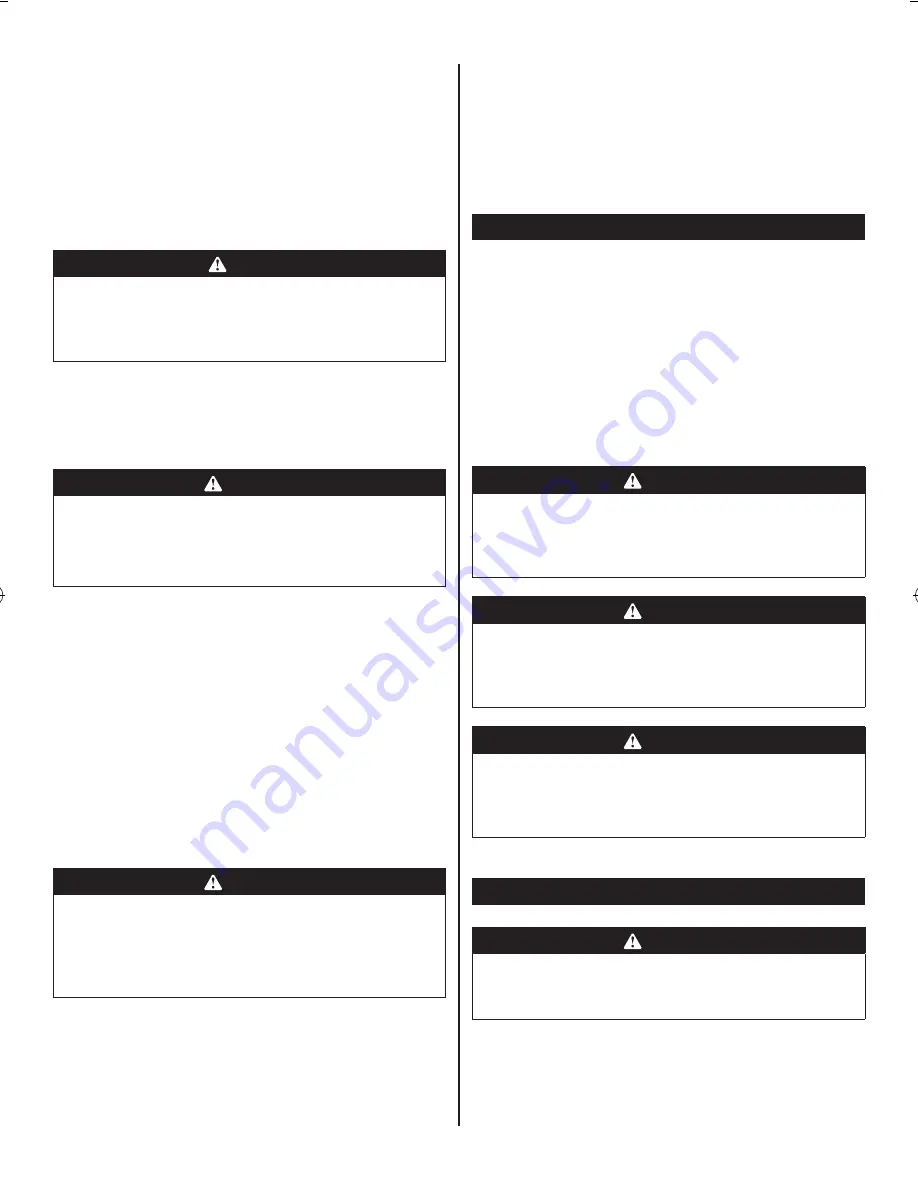
6
2. Pull the ring on the pressure relief valve to release until
pressure gauge reads less than 1.4 bar.
3. Release the ring.
4. Rotate drain valve counterclockwise to open and drain
the moisture.
note:
Condensate is a polluting material and should
be disposed of in compliance with local regulations.
5. If drain valve is clogged, release all air pressure.
Remove and clean the valve, then reinstall.
dAngeR
Unplug the air compressor and release all air from
the tank before servicing. Failure to depressurize tank
before attempting to remove valve may cause serious
personal injury.
6. Rotate drain valve clockwise until tightly closed.
cHeckIng tHe PRessURe ReLIef vALve
See figure 15.
wARnIng
Do not attempt to tamper with the safety valve.
Anything loosened from this device could fly up and hit
you. Failure to heed this warning could result in death
or serious personal injury.
The pressure relief valve will automatically release air if
the air tank pressure exceeds the preset maximum. The
valve should be checked before each day of use by pulling
the ring by hand.
1. Turn the air compressor on and allow the tank to
fill. The compressor will shut off when the pressure
reaches the preset maximum.
2. Turn the air compressor off.
3. Pull the ring on the safety valve to release air for three
to five seconds. Air should rapidly escape. Release the
ring and the air should stop.
4. The ring pin may need to be pushed back into position
to stop the flow of air at high pressure.
wARnIng
If air leaks after the ring has been released, or if the
valve is stuck and cannot be actuated by the ring,
do not use the air compressor until the safety valve
has been replaced. Use of the air compressor in this
condition could result in serious personal injury.
Reset BUtton
See figure 13.
When current into the air compressor motor exceeds the
specified limit, the air compressor will automatically shut
off.
to reset the air compressor:
1. Unplug the air compressor.
2. Turn the air compressor off.
3. Wait three minutes for the motor to cool.
4. Press the reset button.
5. Plug the air compressor into an approved outlet.
6. Turn the air compressor on.
stoRAge
1. Push the power switch to the OFF position to turn off
the compressor.
2. Unplug the compressor.
3. Run the air tool to relieve the air pressure in the hose,
then remove the air hose and the tool, or release the
air by the pressure relief valve.
4. Drain water from the tank as instructed in Draining
the Tank section. Leave the valve open until the next
usage.
5. Store the air compressor in its normal operating
position in a dry and protected area.
wARnIng
Water will condense in the air compressor tank when
the compressor is in operation. Water left in the tank
can cause the tank to weaken and corrode, increasing
the risk of tank rupture.
wARnIng
Always disconnect the air hose from tools whenever
not in use or while servicing. During maintenance, a
tool connected to air hose may operate accidentally,
causing serious personal injury!
wARnIng
Failure to unplug the air compressor before storage
may result in the compressor running continuously,
causing overheating, damage to the compressor, and
possibly a fire.
mAIntenAnce
wARnIng
When servicing use only original replacement parts.
Use of any other parts may create a hazard or cause
product damage.
Summary of Contents for RA-C2550
Page 3: ...Fig 2 Fig 4 Fig 6 Fig 5 1 1 11 16 5 15 18 19 10 16 17 17 16 13 12 11 4 5 Fig 3 15 14 ...
Page 4: ...Fig 7 Fig 11 Fig 10 Fig 12 25 23 Fig 8a Fig 8b Fig 9 7 4 24 20 22 23 7 3 9 26 21 ...
Page 5: ...Fig 13 Fig 16 Fig 14 Fig 15 28 27 4 29 16 33 32 31 30 ...
Page 6: ...Fig 17 34 ...
Page 17: ...11 Parts list ...