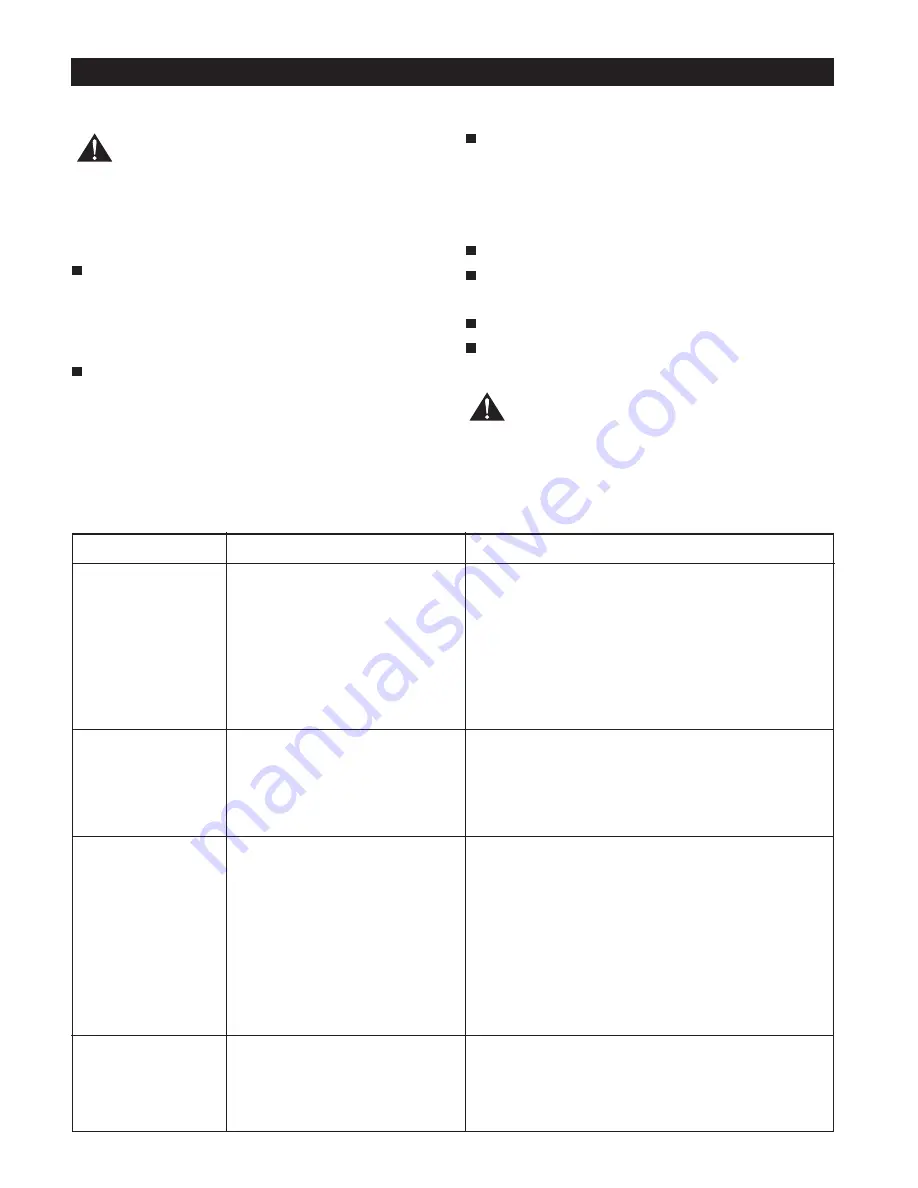
ADJUSTMENTS
MAINTENANCE
WARNING:
For your own safety, turn power switch
“OFF” and remove plug from power source
outlet before maintaining or lubricating
your scroll saw.
GENERAL
Frequently blow out any dust that may
accumulate inside the motor. An occasional
coat of paste wax on the table will allow the
wood being cut to glide smoothly across the
work surface.
CAUTION: Certain cleaning agents and
solvents damage plastic parts. Some of
these are: gaso-line, carbon tetrachloride,
chlorinated cleaning solvents, ammonia and
household detergents that contain ammonia.
Avoiding use of these and other types of
cleaning agents minimises the probability of
damage.
Page 10
LUBRICATION
Arm Bearings - Lubricate the arm bearings
with oil after 10 hours of use. Re-oil after
every 50 hours of use or whenever there is a
squeak coming from the bearings.
To Lubricate(Fig. 12)
Turn saw on its side.
Squirt a generous amount of SAE 20 oil
around the shaft end and bronze bearing.
Let the oil soak in overnight in this condition.
Next day repeat the above procedure for the
opposite side of the saw.
TROUBLE SHOOTING
WARNING:
Turn switch “OFF” and always remove
power cord from the power source before
trouble shooting.
TROUBLE
Breaking Blades
Motor Will Not Run
Vibration
NOTE: There will
always be some
vibration present
when the saw is
running because of
motor operation.
Blade runout-
Blade not in-line
with arm motion.
REMEDY
1. Adjust blade tension. See “REMOVING &
INSTALLING BLADES”.
2. Reduce feed rate.
3. Use narrow blades for cutting thin
wood, wide blades for thicker wood.
4. Avoid side pressure on blade.
5. Blade should have minimum 3 teeth in
contact with workpiece.
1. Replace defective parts before using saw
again.
2. Consult local service agent. Any attempt to
repair this motor may create a hazard unless
repair is done by a qualifi ed service technician.
1. See “MOUNTING YOUR SCROLL SAW TO
A BENCH ”
2. The heavier your workbench is, the less
vibration will occur.A plywood workbench will
not be as good a work surface as the same size
solid timber. Use common sense in choosing a
mounting surface.
3. Tighten table lock knob.
4. Tighten motor mounting screws.
1. Loose cap screws holding blade to upper and
lower arms.Adjust position of blade holders-
retighten holders.
PROBLEM
1. Wrong Tension.
2. Over working blade.
3. Wrong blade application.
4. Twisting blade in wood.
5. Incorrect teeth per inch.
1. Defective cord or plug.
2. Defective motor.
1. Improper mounting of saw.
2. Unsuitable mounting surface.
3. Loose table or table resting
against motor.
4. Loose motor mounting.
1. Blade holders not aligned