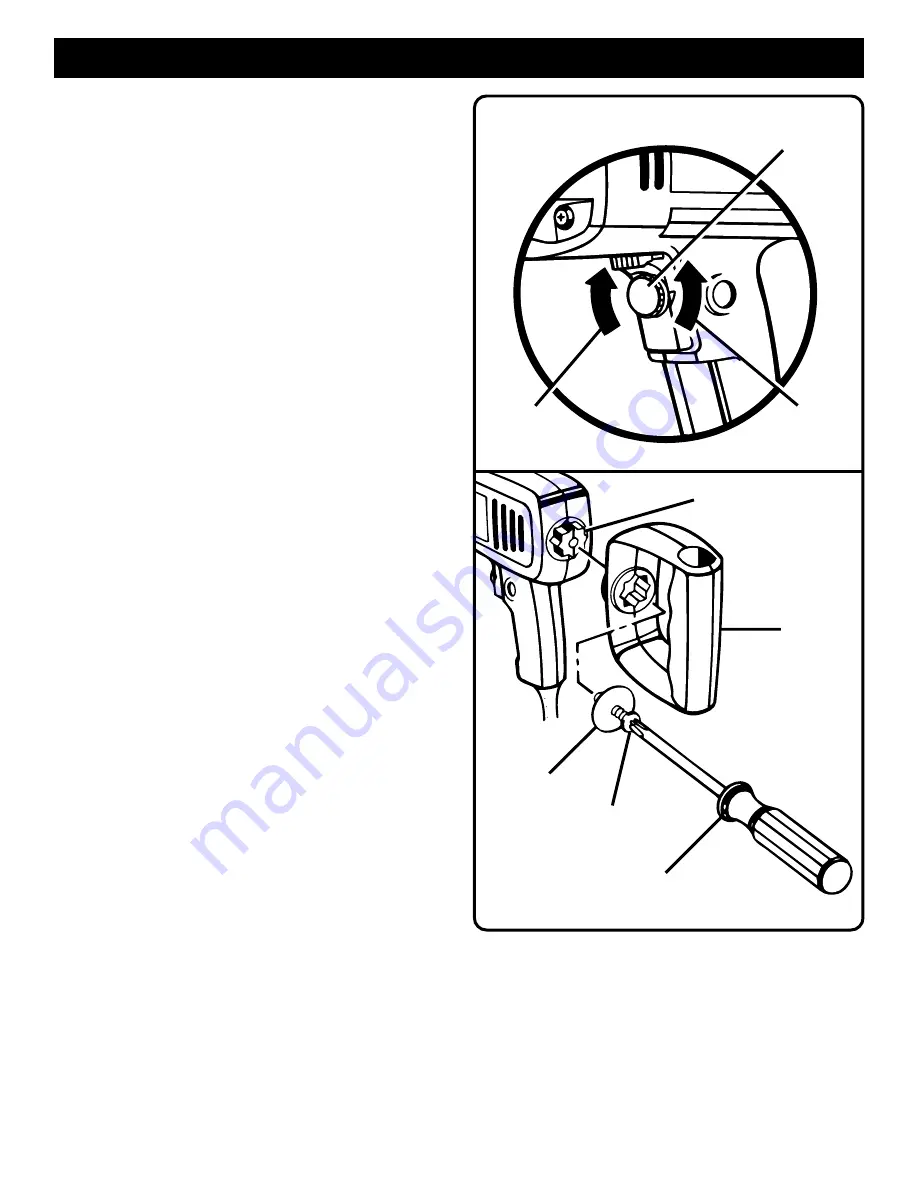
Page 7
VARIABLE SPEED
See Figure 5.
Your drill has a variable speed control selector designed to
allow operator control and adjustment of speed and torque
limits. The speed and torque of your drill can be increased or
decreased by rotating the variable speed control selector in
the direction of the arrows shown in figure 5.
NOTE: Hold your drill in normal operating position and turn
the variable speed control selector clockwise to increase the
speed and torque of your drill. Turn counterclockwise to
decrease the speed and torque of your drill.
If you desire to lock the switch on at a given speed, depress
the switch trigger, push in and hold the lock-on button, and
release the switch trigger. Next, adjust the variable speed
control selector until the desired speed is reached.
NOTE: If the variable speed control selector is fully
turned in the counterclockwise direction (zero setting)
your drill may not run.
If you desire not to use the variable speed control
selector, turn it in the full clockwise direction. This will
allow the speed of your drill to be fully controlled by the
amount of switch trigger depression.
Avoid running your drill at low speeds for extended periods of
time. Running at low speeds under constant usage may
cause your drill to become overheated. If this occurs, cool
your drill by running it without a load and at full speed.
The following guidelines may be used in determining correct
speed for various applications:
LOW speed is ideal when minimum speed and power is
required. For example: starting holes without center punch-
ing, driving screws, mixing paint, and drilling in ceramics.
MEDIUM speed is suitable for drilling hard metals, plastics,
and laminates.
HIGH speed produces best results when maximum power is
required. For example: drilling in wood; soft metals such as
aluminum, brass, and copper; and when using driving acces-
sories.
INSTALLING AUXILIARY HANDLE
See Figure 1, Page 5.
An auxiliary handle is packed with your drill for ease of
operation and to help prevent loss of control. To install, start
the screw threads into the threaded hole in the gear housing
and tighten securely.
NOTE: For convenience the screw has been trapped inside
the auxiliary handle.
To prevent thread damage and possible loss of control,
auxiliary handle should be checked periodically for tightness.
DO NOT operate drill with handle loose.
Fig. 6
Fig. 5
OPERATION
INSTALLING "D" SHAPED HANDLE
See Figure 6.
A multi-position "D" shaped handle is also packed with your
drill. It is used for maintaining proper balance and control of
your drill. To install, place handle in desired position on star
shaped mounting boss. Mounting boss is located on the end
of your drill. Add washer then insert screw. To tighten screw,
insert screwdriver through side of the handle as shown in
figure 6. Tighten screw securely, then remove screwdriver.
VARIABLE SPEED
CONTROL SELECTOR
TO
INCREASE
SPEED
TO
DECREASE
SPEED
STAR SHAPED MOUNTING BOSS
"D" SHAPED
HANDLE
WASHER
SCREW
SCREWDRIVER