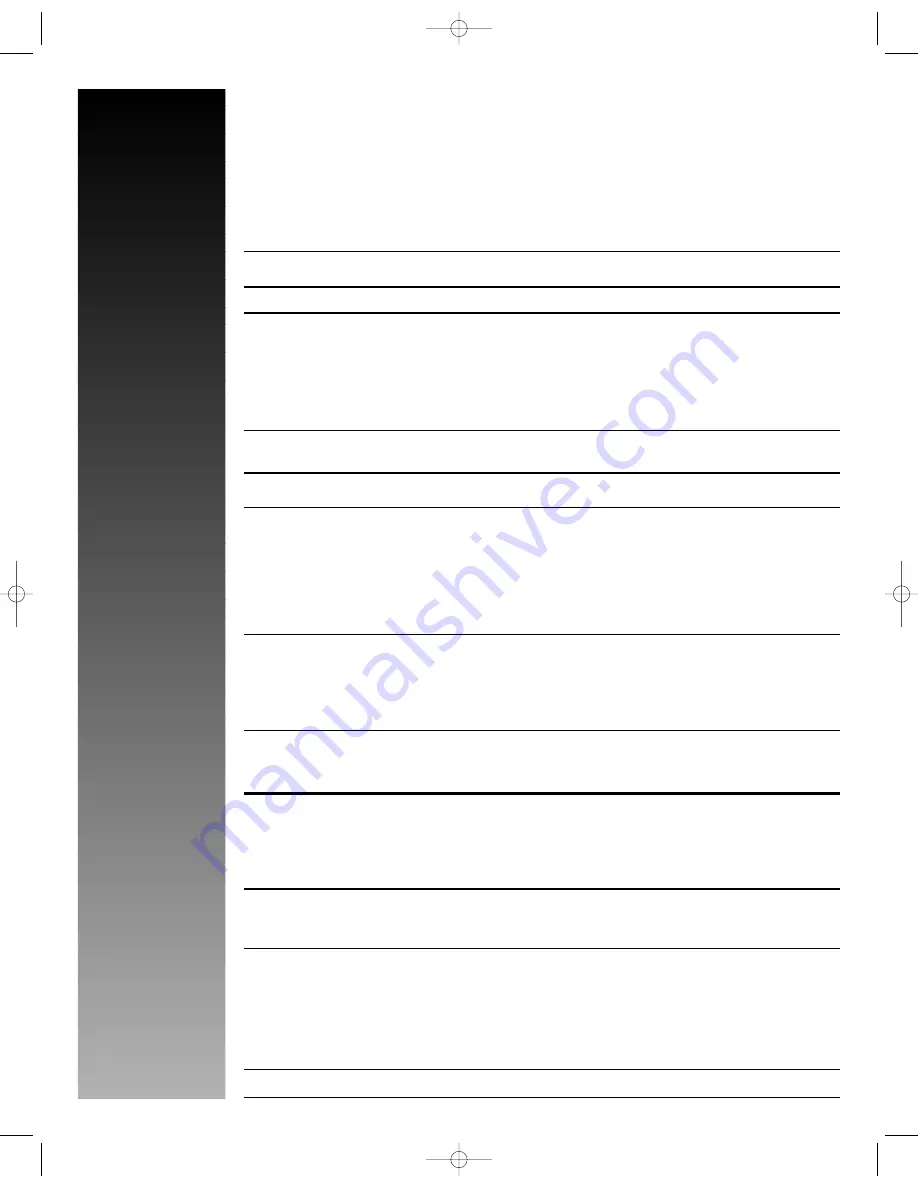
Vacuum System
Problem
No electrical power.
Switch is turned on. Power is
intermittent to all motors.
Electrical shock.
Machine on. Little or no
vacuum at machine or hand
tool vacuum slot.
Machine on, vacuum motor not
working or runs intermittently.
Loss of water pressure
Machine on, spray button
depressed, no spray at
spray tip
Machine on, hand tool lever
squeezed, no spray.
Uneven or weak spray
from tips.
Excessive foaming.
Carpet Discoloration (Yellowing)
Carpet Discoloration (Stained
areas appearing after cleaning)
Streaking
Possible Cause/Remedy
1. Make sure the electrical cord is plugged in. If electrical outlet is connected to a
wall switch, be sure the wall switch is “on.”
2. Check and, if needed, press the “Power Reset” button on machine.
3. Wall circuit breaker off or fuse blown. Turn circuit breaker on or replace fuse.
Unplug any equipment using the same circuit.
4. Fuse in plug blown. (U.K./Ireland BS 1363 plug only.) Replace fuse.
5. Defective Power Cord. (Service must be performed by a qualified repair center
or agent.)
1. Faulty electrical cable, defective switches, or loose terminal connections. (Service
must be performed by a qualified repair center or agent.)
1. Equipment not earthed. Locate and use an earthed outlet.
1. Dome is not sealed. Secure with upper tank restraining wire.
2. Loose or no vacuum hose connection. Check the hose connection at back of
machine and secure if necessary.
3. Accumulated dirt on dome filter screen. Clean filter inside dome.
4. Lint & dirt buildup at vacuum slot. Remove any accumulated debris and clean.
5. Defective vacuum hose assembly inside the machine.
1. Loose wiring connection.
1. Low solution level. Check level and refill if necessary.
1. Solution line not connected. Check the small hose at the back of machine and
reconnect securely at quick coupler.
2. Check Quick Dry/Deep Clean knob at the back of the machine. It should be set
fully on one or the other selection.
3. Clogged spray tip. Remove with wrench. Rinse clean and replace.
4. Clogged solution tank line strainer. Check screen inside lower tank (see
maintenance section). Clean if necessary.
1. Solution line not connected. Check the small hose at the back of machine and
reconnect securely at quick coupler.
2. Clogged spray tip on hand tool. Clean.
3. Clogged solution tank line strainer. Check screen inside lower tank (see
maintenance section). Clean if necessary.
1. Clogged or dirty spray tips. Clean.
2. Accumulated dirt on solution tank line strainer. Check screen inside lower tank
(see maintenance section). Clean if necessary.
Foam caused most often by Upholstery Cleaning Solution or cleaning carpets where
spray foams or shampoo have been used previously.
1. Add 60 to 120 mL Anti-Foam to the white UPPER tank for carpet cleaning.
2. Add 60 to 120 mL Anti-Foam to the white UPPER tank and small amounts at the
hand tool vacuum slot periodically when cleaning upholstery.
1. Carpet may have been overwet or an excessive amount of cleaning product was
used. Spray a light application of Rug Doctor Pro Pet Stain Remover directly on
affected area and brush it in. Allow to dry.
1. Old, very deep spills in carpet padding “wicking” up to surface as carpet dries.
Allow to finish drying. Spray a light application of Rug Doctor Pro Pet Stain
Remover directly on the affected area and brush it in. Allow to dry.
2. Old, deep spills in the carpet padding “wicking” up to surface as carpet dries.
Allow to finish drying. Make one light pass over area with machine using normal
cleaning solution avoiding deep wetting (stain may continue to appear in
subsequent cleanings if overwet). Always avoid overwetting.
1. Clogged spray tip. Remove with wrench. Rinse clean and replace.
Solution System
Foaming
Carpet
Discoloration
Trouble-
shooting
Electrical System
6
76801h-UK-Manual-Warranty.qxd 3/18/08 8:31 AM Page 6