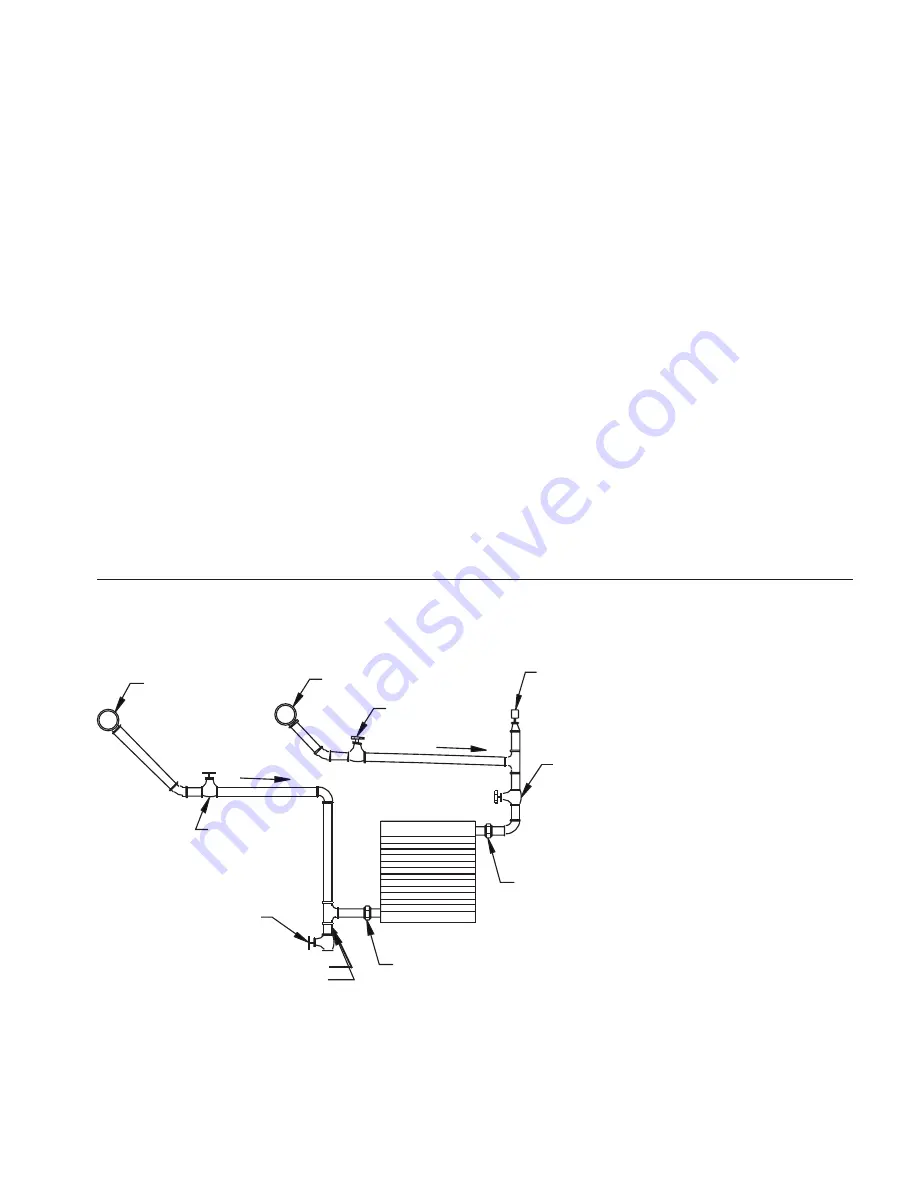
Owner’s Manual
Heat-Exchanger Unit Heaters
FR (Frost Resistant) & HP (High Pressure) Series Heaters
Warning
Please read all warnings and notices on page 2
Part No. 5347-8
Printed in Canada
ISO 9001:2000
CLASSIFICATION
All Ruffneck
TM
FR and HP heaters may be supplied with CSA or UL approved
explosion-proof motors for use in hazardous locations, Divisions 1 & 2, Class I, Groups
C & D and Class II, Groups E, F and G or TEFC (Totally Enclosed Fan Cooled) motors.
Ensure the motor meets the classification requirements.
This manual covers the installation, maintenance, repair
and parts for all FR and HP series heaters.
Ruffneck
TM
is a key brand of CCI Thermal Technologies Inc.
Copyright © 2007. All rights reserved
IMPORTANT NOTICES
WARNING
Read and adhere to the following.
Failure to do so may result in severe or fatal personal injury.
WARRANTY MAY BECOME VOID IF THESE WARNINGS ARE NOT FOLLOWED.
PLEASE SEE WARRANTY FOR FURTHER INFORMATION.
INSTALLATION
2
1. It is essential that any Ruffneck
TM
heater that will be used in a hazardous classified location be fitted with an electric motor that has
been approved for such service and that the fluid temperature is below the ignition temperature of the atmosphere.
2. Operate heater within the mounting guidelines set out in this manual.
3. For correct operation, the heater must be kept clean. Periodic checks to see if the unit is clean are required. If the unit is dirty, clean the
finned tubes, the fan, and the fan guard.
4. Never operate the heater with any or all louvers fully closed.
5. Do not operate in atmospheres which are corrosive to steel or aluminum.
6. Installation and wiring of the heater must adhere to all applicable codes.
7. For steam service use only single pass models (HP1 or FR1).
8. Heater is to be installed and serviced only by a person qualified and experienced with electrical and piping work.
9. Periodically inspect the cores for signs of corrosion and deformed headers. This must be done immediately after a suspected freeze up
or a steam system overpressure condition.
10. Cores that have deformed headers must be replaced as soon as possible.
11. When shutting down a Ruffneck
TM
steam heater, shut off the steam supply first then the heater fan.
WARNING
Disconnect heater from power supply before servicing or repairing heater. Lock the switch in the “OFF” (open)
position and/or tag the switch to prevent unexpected power application. This heater should only be serviced by
personnel with heating equipment experience. Some components of this heater are heavy and assistance will be
required to remove them.
DESCRIPTION
Two basic types of Ruffneck™ Heat Exchanger configurations are available from CCI Thermal Technologies Inc.:
FR (Frost Resistant) Series - for steam service only, up to 100 psi (690 kPa)
HP (High Pressure) Series - for steam and liquid service up to 400 psi (2,700 kPa) on select models
LOCATION OF HEATERS
The following guidelines have been established by CCI Thermal Technologies Inc. to ensure that you properly locate the heaters in
your building. These are only suggestions, and variations may be deemed necessary depending on application.
1.
When occupant comfort is the major objective, heaters should be positioned so that the airflow is directed to areas of
highest heat loss (i.e., doorways, windows and outside walls).
2.
For personnel comfort, a less turbulent and more even air distribution is required. To achieve this effect a larger quantity of
smaller unit heaters should be installed.
3.
When equipment protection is of utmost concern, heaters should be positioned so that the airflow is directed towards the
equipment.
4.
In very large areas, arrangement of heaters should be such that the air will exit from one heater and be projected towards
the inlet, or back, of another heater. A rotational airflow will result, with air circulation in the central area of the building.
Model
Motor HP
RPM
Throw in Feet
SOUND LEVEL dBA
MODEL
REAR
FRONT
3
5.
When arranging heaters, check the fan throws for the heaters being mounted (see table below).
Although it is not generally required that the fan throws reach the next heater, air circulation must be sufficient to prevent
cold spots from occuring.
6.
Do not install heaters such that airflow is blocked or impeded by equipment or walls.
7.
For warehouses or large workshops, it may be acceptable to use fewer, but larger, heaters mounted well above floor level.
it has to be recognized, however, that only the largest heaters have long fan throw distanced.
FAN THROWS FOR RUFFNECK
TM
HEAT-EXCHANGER UNIT AIR HEATERS
NOISE LEVELS
MEASURED SOUND LEVELS OF RUFFNECK
TM
HEAT-EXCHANGER AIR UNIT HEATERS
Where personnel inhabit a room or building for long periods of time, and local ambient noise levels are low,
the noise from the heaters has to be considered. Typically, the smaller the heater the lower the noise level will
be. The largest heaters that move large volumes of air are noticeably noisier than units handling low volumes
of air.
61
70
66
74
74
76
FR/HP - 12
FR/HP - 16
FR/HP - 20
FR/HP - 24
FR/HP - 30
FR/HP - 36
60
70
69
73
73
75
1/4
1/4
1/2
1/2
3/4
1 1/2
1725
1725
1725
1725
1140
1725
FR/HP - 12
FR/HP - 16
FR/HP - 20
FR/HP - 24
FR/HP - 30
FR/HP - 36
40
60
65
70
70
60
Note:
Sound levels were measured at a distance of 15 feet with louver blades horizontal and sound
meters on centreline of heater (i.e., in line with motor/fan shaft).
MOUNTING
Although Ruffneck™ Unit Heaters are designed to be installed in an upright and level position, they may be installed in
other positions. However, for steam service the inlet must be above the outlet and the bottom of the core must drain
toward the outlet. They are designed to be suspended from the top of the cabinet either with two or four (depending on
model) 5/8” NC bolts screwed into internally threaded holes provided in the cabinet top panel. It is essential that adequate
structural support be provided for installation.
Basic Mounting Kits (BMK), Hanging Mounting Kits (HMK), Swivel Hanging Mounting Kits (SHMK) or Wall Mounting Kits
(WMK) are available for Ruffneck™ heaters. If the strength of the structure is not adequate to support the units, a suitable
alternative such as the Ruffneck™ Pipe Mounting Kit (PMK) would be recommended to ensure safe and proper operation.
The HMK is the only suitable mounting kit for the 30” and 36” heater models.
Repair and Replacement Procedures
8
CORES
1. Remove the bottom cover which is attached with #10 screws and 1/4” bolts.
2. Take out the four 1/4” or 5/16” bolts on each side of the cabinet.
3. When removing the core assembly, it will usually be necessary to have assistance in order to handle it safely.
In some instances, dismounting the complete heater from support structure may be advisable to allow core
assembly removal at ground or bench level.
REMOVAL OF FAN, FAN GUARD OR MOTOR
(All models except FR/HP 36)
1. Remove the #10 screws that attach the fan guard to the cabinet.
2. Remove the motor, fan and fan guard together by removing the four 5/16” carriage bolts and nuts that attach
the motor to the motor bracket.
3. Before removing the fan from the motor shaft, measure the distance between the fan hub and the motor end
face. Make a note of this dimension to permit installation of the fan in the correct position at reassembly. The
fan guard must first be positioned over the motor shaft before the fan is installed on the shaft.
FR/HP 36
FAN GUARD
The fan guard consists of a removable upper panel and a frame bolted to the heater cabinet. For most service procedures
it is necessary only to remove the upper removable panel. In cases where the complete fan guard is to be removed,
assistance will be required due to its size and weight. To remove the complete fan guard:
1. Disconnect the wiring from the motor.
2. Remove the bolts fastening the fan guard to the cabinet and slide the fan guard past the motor.
V-BELT-SERVICE -- REMOVAL, INSTALLATION AND TENSIONING
1. Remove upper fan guard panel.
2. Slide motor mount up to relieve the tension to the v-belt and remove the v-belt.
3. Before installing a new v-belt, ensure that the sheaves are properly aligned. (See Drive Sheave Section)
4. Install the new v-belt and tension it by sliding the motor mount down until the v-belt will only move 10 to 16 mm
(3/8 to 5/8 in.) when 68N (15 lbs) of force are applied to the belt midway between the sheaves. Ensure that the
motor is level and then tighten the bolts fastening the motor mount to the drive frame.
5. Replace upper fan guard panel.
6. After a few days of operation the new v-belt will seat-in and may require adjustment.
WARNING
Disconnect heater from power supply before servicing or repairing heater. Lock the switch in the “OFF”
(open) position and/or tag the switch to prevent unexpected power application. This heater should only be
serviced by personnel with heating equipment experience. Some components of this heater are heavy
and assistance will be required to remove them.
9
FAN MOTOR - REMOVAL AND INSTALLATION
1. Remove bolts holding motor to the motor mount.
2. Remove the two piece fan guard assembly.
3. Lift the motor assembly off the motor mount.
4. Before removing the fan, measure and record the location of the fan hub on the motor shaft. If fan is difficult to
remove, use a gear puller on the fan hub.
5. To reassemble, position fan on motor shaft, and tighten set screws.
6. Place motor assembly onto motor mount, and fasten the fan guard to cabinet.
DRIVE SHEAVES - REMOVAL AND INSTALLATION
1. The sheaves on the fan motor and fan drive may be removed by removing the cap screws from the bushings.
2. Thread the cap screws into the threaded removal holes and progressively tighten the cap screws until the
sheave and bushing are loose and slide off the shaft.
3. To install; first slide the sheave with the bushing and cap screws in place onto the shaft. Align the sheaves.
4. Tighten the cap screws alternately until a torque of 10.8Nm (8ft.-lbs) is achieved. DO NOT over torque,
damage may result.
DRIVE FRAME - REMOVAL
1. Remove the complete fan guard assembly as described in the Fan Guard section.
2. Support the fan drives frame, then remove the bolts fastening it to the heater. Lower frame from the heater.
FAN SHAFT BEARINGS - REMOVAL AND INSTALLATION
The ball bearings used on the FR/HP-36 heaters are of the extended inner ring type, which use an eccentric
self-locking collar for a positive locking action of the shaft.
1. The fan shaft bearing may be serviced either on the heater by removing the upper fan guard panel or first
removing the whole drive frame from the heater.
2. Remove the v-belt and the drive sheave as described in the appropriate section.
3. Measure and record the distance from the end of the shaft to the bearing housing.
4. Loosen the set screws in the locking collars. Unlock the collars by placing a drift punch in the collar hole and hit
the punch opposite to the direction of shaft rotation.
5. Loosen and remove the bolts fastening the bearing to the bearing support and slide bearings off the shaft.
NOTE: It may be necessary to file the burr left by the bearings set screws on the shaft, in order to remove the
inner bearing.
6. To install new bearings; slide the bearings and locking collars onto the shaft with the locking collars facing each
other. Bolt bearings onto the bearing support. Position shaft using the measurement taken in Step 3.
7. Assemble locking collars to the bearing, turning them in the direction of shaft rotation and use a drift punch to
tighten the collar in place. Then tighten the set screws in the locking collars.
8. Reassemble the unit, ensuring the sheaves are aligned and the v-belt is tensioned as described in the
appropriate sections.
FAN - REMOVAL AND INSTALLATION
1. Remove the fan guard assembly as described in the Fan Guard Section.
2. Remove the drive frame as described in the Drive Frame Section.
3. Remove the set screws on the fan hub and remove the fan from the shaft. NOTE: if the shaft is corroded it may
be necessary to replace the shaft.
4. To reassemble, slide the shaft into the fan hub until the end of the hub. Ensure that the two flats on the shaft
align with the set screws in the fan hub. Then tighten the fan’s set screws.
10
ITEM
PART
FR, HP 12
FR, HP 16
FR, HP 20
FR, HP 24
FR, HP 30
NO.
DESCRIPTION
QTY NUMBER
QTY NUMBER
QTY NUMBER
QTY NUMBER
QTY NUMBER
1
FR1 CORE ASSEMBLY
1 2053
1 2054
1 2055
1 2056
1 2057
1
HP1 CORE ASSEMBLY
1 2051
1 1914
1 1986
1 2042
1 2043
1
HP3 CORE ASSEMBLY
1 2065
1 1936
1 1875
1 2045
1 2047
1
HP5 CORE ASSEMBLY
1 1983
1 1991
1 2046
1 2048
1
HP7 CORE ASSEMBLY
1 2190
1 2188
2
MOTOR BRACKET
1 1512
1 1217
1 1237
1 1219
1 1280
3
LOUVER BLADE KIT
1 4881
1 4882
1 4883
1 4884
1 4958
4
BOTTOM PANEL
1 7874
1 7868
1 7861
1 7960
1 8391
5
TOP PANEL
1 7875
1 7870
1 7865
1 7961
1 8395
6
RIGHT PANEL
1 7872
1 7866
1 9885
1 9057
1 8393
7
LEFT PANEL
1 7873
1 7867
1 9884
1 9058
1 8394
8
FAN SHROUD
1 7871
1 7869
1 7864
1 7962
1 8392
9
MOTOR
1
--
**
--
1
--
**
--
1
--
**
--
1
--
**
--
1
--
**
--
10
FAN BLADE
1 1513
1 1378
1 1382
1 1389
1 1386
11
FAN GUARD
2 5456
2 5457
2 5458
2 5459
2 5460
** Check motor name plate for voltage, phase, H.P., frame size, and service classification.
PARTS LIST
FR/HP 12, 16, 20, 24 and 30 models
1
8
15
16
7
10 11 14 17
12
5
13
9
2
6
4
3
11
PARTS LIST
FR/HP 36 models
ITEM
PART
FR, HP36
NO.
DESCRIPTION
QTY NUMBER
1
FR1 CORE ASSEMBLY
1 2058
1
HP1 CORE ASSEMBLY
1 2044
1
HP3 CORE ASSEMBLY
1 2049
1
HP5 CORE ASSEMBLY
1 2050
1
HP7 CORE ASSEMBLY
1 2189
2
MOTOR BRACKET
1 3426
3
LOUVER BLADE KIT
1 4959
4
BOTTOM COVER
1 1233
5
MOTOR
1
--
**
--
6
U-CLIPS
2 3444
7
FAN BLADE
1 1395
ITEM
PART
FR, HP36
NO.
DESCRIPTION
QTY NUMBER
8
FAN GUARD FRAME
1 3443
9
TAPER BUSHING, DRIVE
1
--
*
--
10
DRIVEN SHEAVE
1 1398
11
1” TAPER BUSHING, DRIVEN
1 1401
12
V-BELT
1 1402
13
DRIVE SHEAVE
1 1399
14
BEARING 1” PILLOW BLOCK
2 1396
15
FAN GUARD, UPPER PANEL
1 3455
16
FRAME, 36 FAN DRIVE
1 3424
17
SHAFT
1 1268
* Specify shaft diameter when ordering.
** Check motor name plate for voltage, phase, H.P., frame size, and service classification.
Maintenance Plan
5918 Roper Road
Edmonton, Alberta T6B 3E1
Canada
Phone: (780) 466-3178
Fax: (780) 468-5904
www.ccithermal.com
ISO 9001:2000
WARNING
Disconnect heater from power supply before servicing or repairing heater. Lock the switch in the “OFF”
(open) position and/or tag the switch to prevent unexpected power application. This heater should only be
serviced by personnel with heating equipment experience. Some components of this heater are heavy
and assistance will be required to remove them.
All terminal connections and wire installations should be inspected annually for damage, looseness, fraying defects, etc.
as applicable.
Keep the fins clear of any materials likely to plug or clog the fins. We suggest that cleaning of the cooling fins be
accomplished by use of an air nozzle.
The fan guard should be kept clear of any materials that may impede the air flow thereby reducing heater output capacity.
The unit’s fan should be inspected to ensure that the blades are not bent, dirty or running out of balance. If the blades are
dirty, they should be cleaned using water. The fan blades must not be allowed to operate in an unbalanced condition as
the fan blade(s) may fall from fatigue and possibly cause damage to the cooling fins of the heater cores.
If the output of the heater drops significantly, it is possible that the core tubes may have become partially blocked
internally. In such cases, the core should be flushed out with water or a suitable liquid. Flow should return to normal. but, in
extreme cases, reverse flow or flushing may be required (refer to Repair & Replacement Procedures for removal of core).
The bolts that attach the heater assembly and motor should be checked for tightness periodically. Please refer to Repair &
Replacement Procedures Section for further reference.
Warranty
CCI Thermal Technologies Inc. warrants all Ruffneck™ Unit Heaters against defects in materials and
workmanship; damage due to over-torquing of inlet/outlet connections; and for the FR Series units, damage
due to inadvertent freeze-up(s). CCI Thermal technologies Inc. will make good or replace any faulty equipment
within one year from date of purchase. Faulty equipment shall be returned to CCI Thermal Technologies Inc.
freight charges prepaid. This warranty shall be limited to the actual faulty equipment and under no
circumstances shall include or extend to installation costs or to consequential losses or damages.
PLEASE CALL BEFORE REPAIRING
It will save time and money. Failure to do so may be dangerous and may
void certain provisions of your warranty. For information regarding
installation, operation, repair, or purchase, please call our:
24 Hr. Hotline: 1-800-661-8529
(USA and Canada)
Please have model and serial numbers available before calling.
Phone: (780) 466-3178
Fax: (780) 468-5904
5
FIG.2
UNIT HEATER CONNECTION
FOR LOW-PRESSURE STEAM,
OPEN GRAVITY OR VACUUM
RETURN SYSTEM
NOTES:
1. For medium to high-pressure systems a bucket
or float trap must be used.
2. Do not use with fluids corrosive to steel.
3. Install using proper piping practices
4. In horizontal pipe runs, use eccentric reducers only.
5. Use a properly sized steam trap.
FIG.3
UNIT HEATER CONNECTIONS
TO OVERHEAD STEAM AND
RETURN MAINS
NOTES:
1. This piping arrangement is only for two-position-type
control. Modulating steam control may not provide sufficient
pressure to lift condensate to return main.
2. Do not use with fluids corrosive to steel.
3. Install using proper piping practices.
4. In horizontal pipe runs use eccentric reducers only.
5. Use a properly sized steam trap.
TAP INTO TOP OF MAIN
SHUT-OFF VALVE
UNION
PITCH DOWN
UNION
RETURN
MAIN
TAP INTO TOP OF MAIN
SHUT-OFF VALVE
PITCH DOWN
FULL SIZE DROP LEG
10.0 in. Min.
(254 mm)
SHUT-OFF VALVE
RETURN MAIN
PITCH
DOWN
LIFT NOT TO EXCEED 1 FT FOR
EACH POIND PRESSURE
DIFFERENCE BETWEEN STEAM
AND RETURN MAINS
THERMOSTATIC AIR
VENT OR PETCOCK.
(INSTALL IF TRAP DOES
NOT HAVE AIR VENT)
SHUT-OFF
VALVE
FLOAT AND
THERMOSTATIC
TRAP
STEAM
MAIN
UNION
UNION
UNION
UNION
SWING CHECK VALVE
STEAM TRAP WITH AIR VENT
STAINER AND DRAIN VALVE
6 in. (152mm) LONG
FULL SIZE
DIRT POCKET
STAINER
10 IN. Min.
(254 mm)
FULL SIZE DROP LEG
6 in. (152mm) LONG
FULL SIZE
DIRT POCKET
UNION
Electrical Wiring
7
Ruffneck
TM
fan-forced unit heaters and heat exchangers may be thermostatically controlled if required. Usually the flow of
heat transfer fluid is allowed to pass through the heat exchanger without interruption. The fan motor, in such cases, shuts
on and off by an electrical thermostat. Air flow through the heater is thus controlled. A small amount of heat will radiate
from the heat exchanger when the fan is inoperative but this is usually tolerable. Absolute control of heat output from the
heat exchanger would require that steam or flow of hot liquid to the heat exchanger be shut off. Such control of the heat
transfer medium is possible by thermostatic valve control, separately or in combination with thermostatic fan control.
Typically a manual shut-off valve is placed in the steam or liquid line for control purposes.
NOTES:
- Installation must comply with local electrical code.
- For internal wiring of control devices and starters, consult device manufacturer.
- The thermostat must have an electrical rating equal to or exceeding the HP, line voltage and current expected.
- For wiring of fan motor, refer to diagram on the motor name plate.
- Some motors may be equipped with external high-limit wires. These wires must be connected in series with the motor control circuit. (see
appropriate diagrams above)
SUPPLY VOLTAGE
208/230V
1PH
208/230 VOLT
CONTACTOR COIL
(NOT SUPPLIED)
EXTERNAL CONTROL PANEL
(NOT SUPPLIED)
230 VOLT
THERMOSTAT
THERMOSTATIC CONTROL FOR
208/230 VOLTS, 1 PHASE
THERMOSTATIC CONTROL FOR
115 VOLTS, 1 PHASE
THERMOSTATIC CONTROL FOR
208/230 VOLT, 3 PHASE MOTORS
C/W EXTERNAL HIGH-LIMIT WIRES
THERMOSTATIC CONTROL FOR
208/230 VOLTS, 3 PHASE
THERMOSTATIC CONTROL FOR
460/600 VOLTS, 3 PHASE
THERMOSTATIC CONTROL FOR
460/600 VOLT, 3 PHASE MOTORS
C/W EXTERNAL HIGH-LIMIT WIRES
FAN
MOTOR
FAN
MOTOR
FAN
MOTOR
FAN
MOTOR
SUPPLY VOLTAGE
115 VOLTS
1 PH
NEUTRAL
115 VOLT
THERMOSTAT
SUPPLY
VOLTAGE
208/230
VOLTS
3PH
SUPPLY VOLTAGE
208/230
VOLTS
3PH
208/230 VOLT
CONTACTOR COIL
3 POLE CONTACTOR RELAY
(NOT SUPPLIED)
EXTERNAL CONTROL PANEL
(NOT SUPPLIED)
3 POLE CONTACTOR RELAY
(NOT SUPPLIED)
SUPPLY
VOLTAGE
460/600
3PH
VOLTAGE
TRANSFORMER
(NOT SUPPLIED)
EXTERNAL CONTROL PANEL
(NOT SUPPLIED)
24 TO 230 VOLT
THERMOSTAT
230 VOLT
THERMOSTAT
208/230 VOLT
CONTACTOR COIL
MOTOR C/W EXTERNAL
HIGH-LIMIT WIRES
230 VOLT
THERMOSTAT
EXTERNAL CONTROL PANEL
(NOT SUPPLIED)
SUPPLY VOLTAGE
460/600
VOLTS
3PH
EXTERNAL CONTROL PANEL
(NOT SUPPLIED)
VOLTAGE
TRANSFORMER
(NOT SUPPLIED)
24 TO 230 VOLT
THERMOSTAT
3 POLE CONTACTOR RELAY
(NOT SUPPLIED)
MOTOR C/W EXTERNAL
HIGH-LIMIT WIRES
3 POLE CONTACTOR RELAY
(NOT SUPPLIED)
FAN
MOTOR
FAN
MOTOR
24 TO 230
VOLTS
24 TO 230
VOLTS
2" NPT FEMALE
CONNECTION
CONNECTION
5/8" UNC
K
D
G
H
L
F
B
I
A
E
C
J
CONNECTION
6
Physical Dimensions
DIM
FR/HP12
FR/HP 16
FR/HP 20
FR/HP 24
FR/HP 30
FR/HP 36
A
16 5/16 (415)
20 5/16 (516)
24 5/16 (618)
28 3/8 (720)
34 7/16 (874)
42 5/8 (1083)
B
16 3/8 (416)
20 5/16 (517)
24 5/16 (618)
28 1/4 (718)
34 5/16 (872)
42 5/8 (1083)
C
4 (102)
4 (102)
4 (102)
4 5/8 (118)
5 11/16 (145)
5 1/2 (140)
D
9 3/4 (248)
9 3/4 (248)
10 1/2 (267)
11 13/16 (300)
13 3/4 (350)
23 5/8 (600)
E
12 5/8 (320)
15 1/2 (394)
19 1/2 (495)
23 7/16 (596)
29 1/2 (750)
37 3/8 (950)
F
11 (280)
15 (381)
17 (432)
19 11/16 (500) 25 9/16 (650)
29 1/2 (750)
G
N/A
1 3/4 (44)
2 1/2 (63)
2 3/4 (70)
3 1/8 (80)
3 1/8 (80)
H
6 3/4 (172)
5 3/4 (147)
5 3/4 (146)
6 11/16 (170)
7 1/2 (190)
9 7/16 (240)
I
2 5/8 (68)
2 5/8 (68)
3 5/8 (93)
4 5/16 (109)
4 3/8 (111)
6 7/16 (163)
J
1 7/8 (48)
2 3/4 (70)
2 7/8 (73)
3 (76)
3 1/8 (80)
3 (76)
K*
(MAX)
21 1/4 (540)
21 1/4 (540)
22 7/16 (570)
23 5/8 (600)
25 3/16 (640)
34 5/8 (880)
L
(MAX)
1 5/8 (42)
1 5/8 (42)
1 5/8 (42)
1 5/8 (42)
1 7/8 (47)
1 3/4 (45)
Core weight
lbs (Kg)
27 (12)
38 (17)
48 (22)
91 (41)
121 (55)
175 (79)
Unit weight
lbs (Kg)
80 (36)
100 (45)
126 (57)
191 (87)
286 (130)
534 (242)
Shipping weight
lbs (Kg)
132 (60)
148 (67)
174 (79)
214 (97)
321 (146)
526 (239)
*May vary with motor used.
Note: The FR/HP12 has only
two mounting holes on
the top of the unit.
4
SHUT-OFF VALVE
PITCH DOWN
UNION
6 in. (152 mm) LONG
FULL SIZE
DIRT POCKET
RETURN
SUPPLY
PITCH DOWN
DRAIN VALVE
AUTOMATIC
AIR VENT
OR
PETCOCK.
SHUT-OFF VALVE
BALANCING
VALVE
UNION
Where heaters are installed in applications that are of a relocatable or transportable nature such as land or offshore drilling
rigs, an adequate mounting structure should be supplied to withstand all probable load conditions. Such load conditions
should recognize abuse situations such as truck off-loading impacts, etc. It is recommended that lock washers be used
beneath the bolt heads for these installations.
Heaters may be mounted at any reasonable height above floor level depending on the purpose of the heater. When
equipment is placed in a seldomly occupied building, the heaters may be placed at a low level. When heaters are required
to ensure personnel comfort, they should be mounted overhead. Typically, mounting heights range from 7 1/2 feet to 12
feet. All Ruffneck™ heaters have louvers installed that allow air flow to be directed from horizontal to 60 degrees or greater
downward deflection. Louvers should never be set to within less than 15 degrees of the closed position.
CLEARANCES FOR MAINTENANCE
It is important to provide adequate clearance around the heater for servicing. Allow enough space to permit easy fan or
motor replacement. Do not position the back of the fan motor against a surface, as air for the cooling fan will be blocked. It
is advisable to leave at least 2” clearance between the rear of the motor and the nearest obstruction. For easy removal of
the heat exchanger core assembly, it is important to leave clearance beneath the heater equal to the height of the heater
cabinet plus two inches.
PIPING APPLICATIONS
The following piping application and arrangements are only suggestions. Since it is impractical to cover all possible
applications, please refer to detailed piping references for more information.
Below are suggested piping arrangements.
FIG.1
UNIT HEATER
CONNECTIONS TO
OVERHEAD
FLUID MAINS
NOTES:
1. Do not use with fluids corrosive to steel
2. Install using proper piping practices.
CABINET MATERIAL
EPOXY POWDER COATED CARBON STEEL
A
HERESITE® PHENOLIC COATED CARBON
STEEL
B
STAINLESS STEEL
C
FRHP Heat-Exchanger Unit Heaters
Model Coding
HEATER SIZES AVAILABLE
MODEL & SIZE
HP1-12 THRU HP1-36
1 - Pass
HP1
HP3-12 THRU HP3-36
3 - Pass
HP3
HP5-16 THRU HP5-36
5 - Pass
HP5
HP7-24 THRU HP7-36
7 - Pass
HP7
FR1-12 THRU FR1-36
1 - Pass
FR1
MOTOR ENCLOSURE
1
TOTALLY ENCLOSED
2
X-PROOF, GR C, D, E , F & G
MOTOR ELECTRICAL
VOLTS
PHASE
HERTZ
A
115
1
60
B
208
1
60
C
208
3
60
D
230
1
60
E
230
3
60
F
460
1
60
G
460
3
60
H
575
3
60
I
220
1
50
J
380
3
50
K
440
3
50
Note: CCI units utilize a standard motor. Specifying any
other O.E.M. motor may result in longer lead times.
Heresite
®
coated exchangers and cabinets: contact
factory for quote.
Louvres and fan blades are also Heresite
®
coated.
Contact factory for shipping lead time.
Motor designed to be used at rated voltage with
tolerances of ±15%.
Motor may be marked 230 volts, but is suitable for 208
volt operation.
460 1 phase motors are only certified for groups D, F & G
Only available in 16” and larger units
Only available in 24” and larger units
TUBE MATERIAL
W
ALL
T
HIC
KNESS
R
OWS
FINNING
TUBING
FINS/
INCH
MATERIAL TYPE
A
.065"
3
10
AL
TW
5/8"
TW = Tension Wound
EX = Extruded
AL = Aluminum
SERIES
FAN
SIZE
CABINET
MATERIAL
EXCHANGER
COATINGS
CONNECTIONS
TUBE
MATERIAL
MOTOR
EXCHANGER COATINGS
HEAT RESISTANT ALUMINUM PAINT
1
HERESITE® PHENOLIC COATING
2
CONNECTIONS
2” NPT FEMALE
A
2” NPT MALE, SCH. 80
B
2” 300# RF FLANGE
C
FAN SIZE
12” DIA
12
16” DIA
16
20” DIA
20
24” DIA
24
30” DIA
30
36” DIA
36
HP1
12
A
1
A
1
1
A
12
13
NOTES