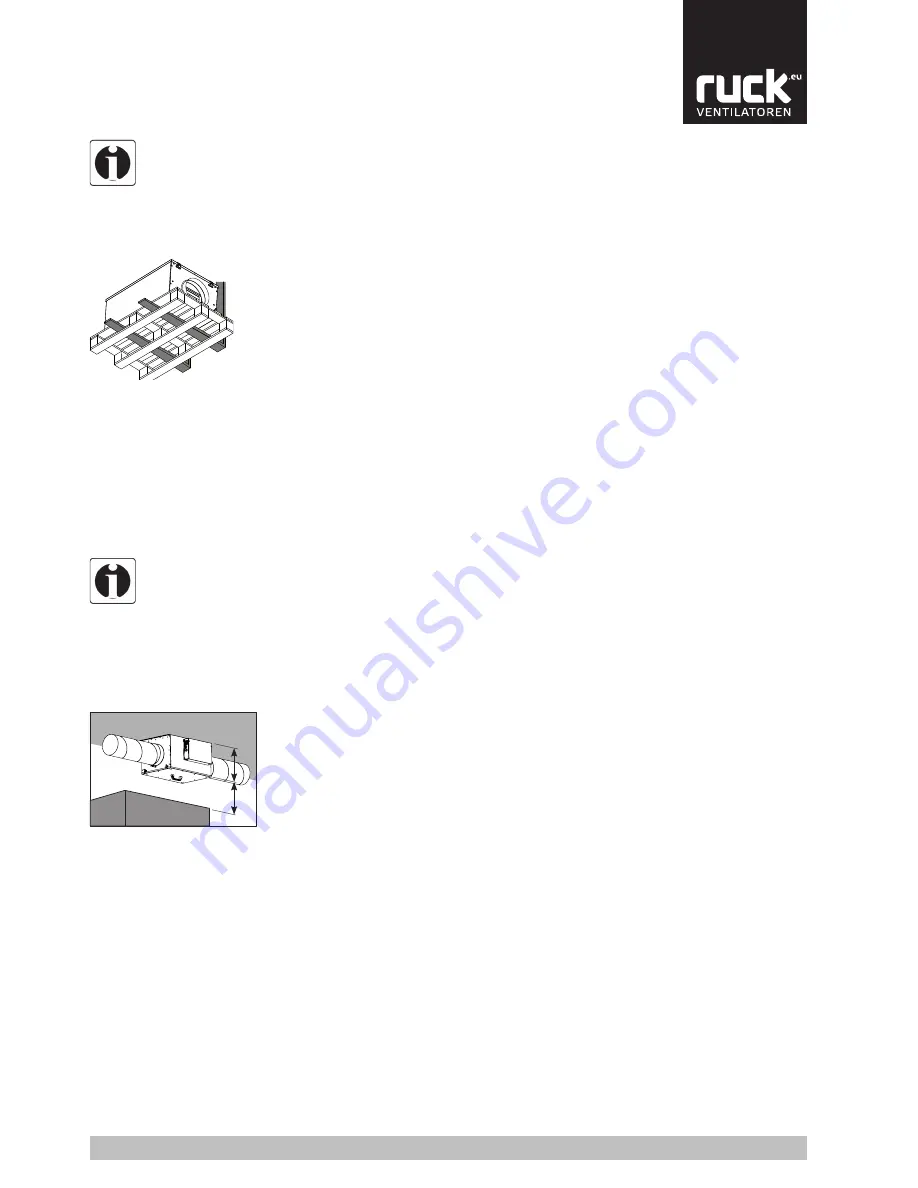
English
5. Transport and storage
6. Assembly
Transport and storage should only be performed by specialist personnel in accordance with the installation
and operating manual and regulations in force.
The following points should be noted and followed:
•
Check the delivery according to the delivery note to ensure it is complete and correct and check for
any damage. Any missing quantities or damage incurred during transport should be confirmed by the
carrier. No liability is accepted if this is not observed.
•
The product weighs approx. 17 - 32 kg (depending on the product type in question).
•
It should be transported with suitable lifting equipment in the original packaging or on the transport
equipment indicated.
•
If transported with a forklift it should be ensured that the product is resting with the basic profile or
base frame completely on the forks or on a pallet and the product‘s centre of gravity is between the
forks (see Fig. 4).
•
The driver must be authorized to drive a forklift truck.
•
Do not go beneath the suspended load.
•
Only lift and transport the machine by its base plate, never by the cover handle!
•
Avoid damage or deformation of the housing.
•
The product must be stored in a dry area and protected from the weather in the original packaging.
Open pallets should be covered with tarpaulins. Even weatherproof modules should be covered
because their weather resistance is only guaranteed after complete installation.
•
Storage temperature between –10 °C and +40 °C. Avoid severe temperature fluctuations.
•
If the product has been in storage for more than a year, check the smooth running of impellers and
valves by hand.
Assembly work may only be performed by specialist personnel in accordance with the installation and
operating manual and the regulations and standards in force.
The following points should be noted and followed:
•
The product should only be installed on ceilings with the cover on the bottom (installation height: min
1.8 m above the ground). Alternative installation positions are given in Section 6.1 „Permitted installa
-
tion positions“.
•
Only install in dry rooms with no condensation.
•
Installation accessories should be provided by the client.
•
Only suitable installation aids, in accordance with regulations, should be used.
•
The installation should be easily accessible for maintenance and cleaning and should be easy to
dismantle. Leave a space of at least the height of the unit + 5 cm from other units, shelves or cabinets
to facilitate maintenance work such as changing the filter (see Fig. 5).
•
The unit should only be installed with authorized and suitable fastening materials at all fastening
points.
•
It must be fastened with screws or threaded rods, minimum diameter 8 mm.
•
The unit should only be installed on ceilings with adequate load-bearing capacity. Wall installations
are only permitted in the positions shown in Section 6.1 „Permitted installation positions“.
•
Do not distort the unit when installing.
•
The unit should be suitably secured.
•
No holes should be made in the housing, or any screws screwed into it.
•
The duct system must not be supported on the housing.
•
It is recommended that the duct system is attached with flexible connections in order to isolate any
structure-borne noise.
•
Make sure that the duct system cannot be closed.
•
Make sure that the intake duct has direct access to the intake air.
•
Warning: branches in the intake duct, to other fan units for example, may, if the dimensions are too
small, lead to low pressure in the duct and therefore malfunction of the unit.
•
The pressure loss in the duct system must not be more than the capacity of the unit! The pressure
loss in the duct should not be more than 2/3 the unit‘s maximum pressure so that an adequate air
output can still be achieved. This will prevent malfunction.
•
Pressure losses in the duct system are adversely affected by: the length of the duct system, small
pipe or duct cross-section, elbows, additional filters, valves, etc.
Fig. 4:
Unit transported on a pallet with
a forklift.
Fig. 5:
Minimum distance for
maintenance work.
9
H
H+5 cm
00
137771
www.ruck.eu
Summary of Contents for FFH 125 EC 10
Page 33: ...English Notes 33 www ruck eu...