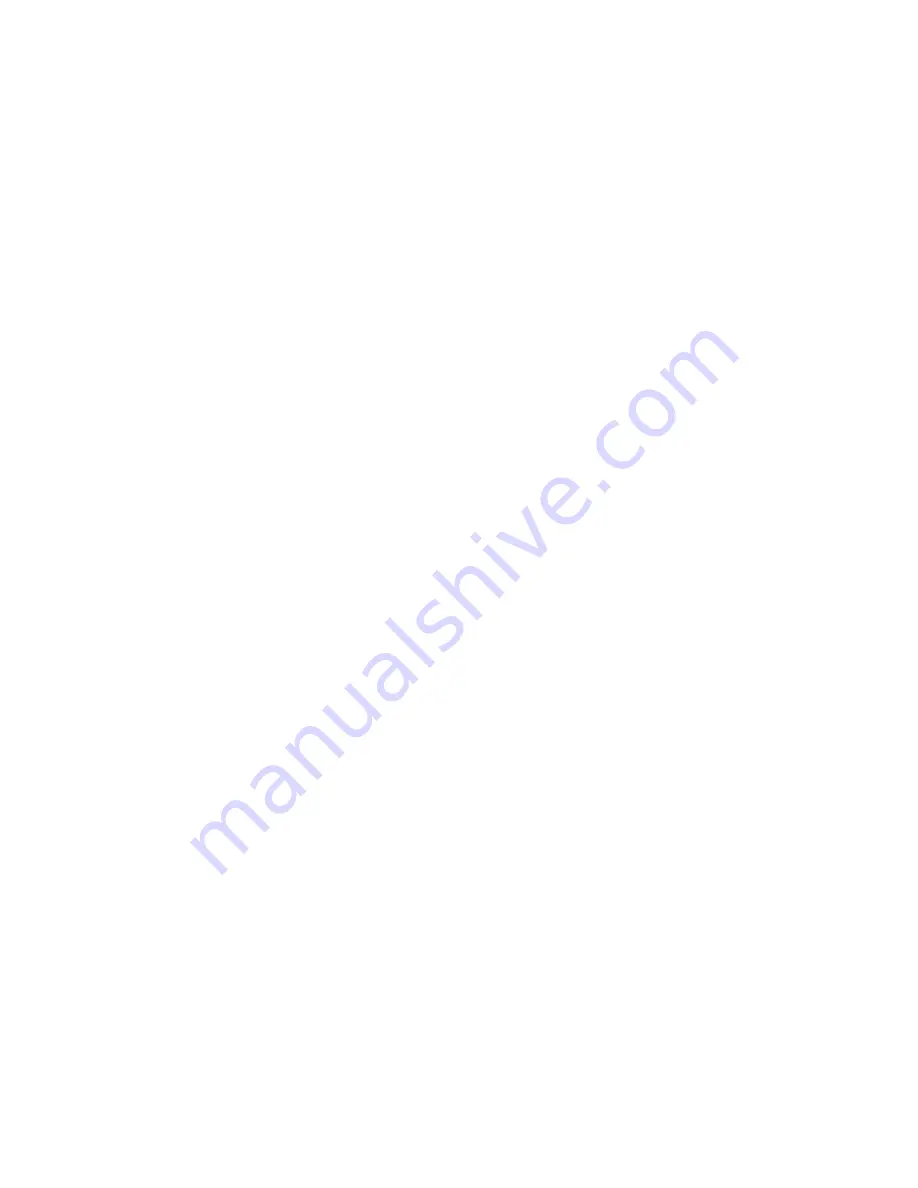
23
4.1 Power
The machine is designed to operate on a 240
+/- 15% input single phase AC outlet.
Ensure that there is adequate ventilation
around the machine when it is connected to
the mains power supply.
4.2 Shielding Gas
When working the machine in the TIG mode
of welding the process requires a shielding gas.
The shielding gas can be supplied via a pressure
regulator to the machine from either a fixed
installation or single cylinder of gas.
If a cylinder of gas is used, please ensure that
the cylinder is securely fastened (refer to the
section on cylinder handling and safety), before
starting any welding operation.
Refer to the application section for the
selection of the correct shielding gas.
4.3 TIG Torch Connection
The R-Tech TIG200DC PFC
machine is rated at 200A, 35% duty cycle.
The matching TIG torch for this machine is the
Wp26 torch.
1 The WP26 TIG torch is fitted to
the machine by means of the dinse back end.
For DC (-) TIG operation fit the torch back end
to the negative dinse connection (similarly for
DC (+) fit the torch
backend to the positive dinse connection).
2 The gas hose is fitted to the gas fitting (GAS)
located on the front bottom panel of the
machine.
4.4 MMA Operation
The R-Tech TIG200DC PFC can
be used as a MMA welding machine by fitting a
electrode holder and a work return lead to the
respective dinse connectors (dependant on the
type of electrodes being used. Please consult
the packaging supplied by the manufacturer for
the correct polarities).
4.0 Connecting your R-Tech TIG200DC PFC
welding machine
Summary of Contents for Tig200
Page 9: ...7 2 4 Shielding Gas Selection...
Page 12: ...10...
Page 13: ...11...
Page 14: ...12...
Page 15: ...13 2 9 Joint Preparation...
Page 16: ...14...
Page 17: ...15...
Page 18: ...16...
Page 19: ...17 3 0 TIG Welding of Materials 3 1 Application Summary...
Page 26: ...24 TIG ARC 200MP TIG ARC 200MP 1 2 3 4 5 6 7 8 10 11 12 16 38 37 29 24 22 23 34 32 27 9 25 26...
Page 27: ......
Page 33: ...31 Notes...
Page 34: ...33 Notes...