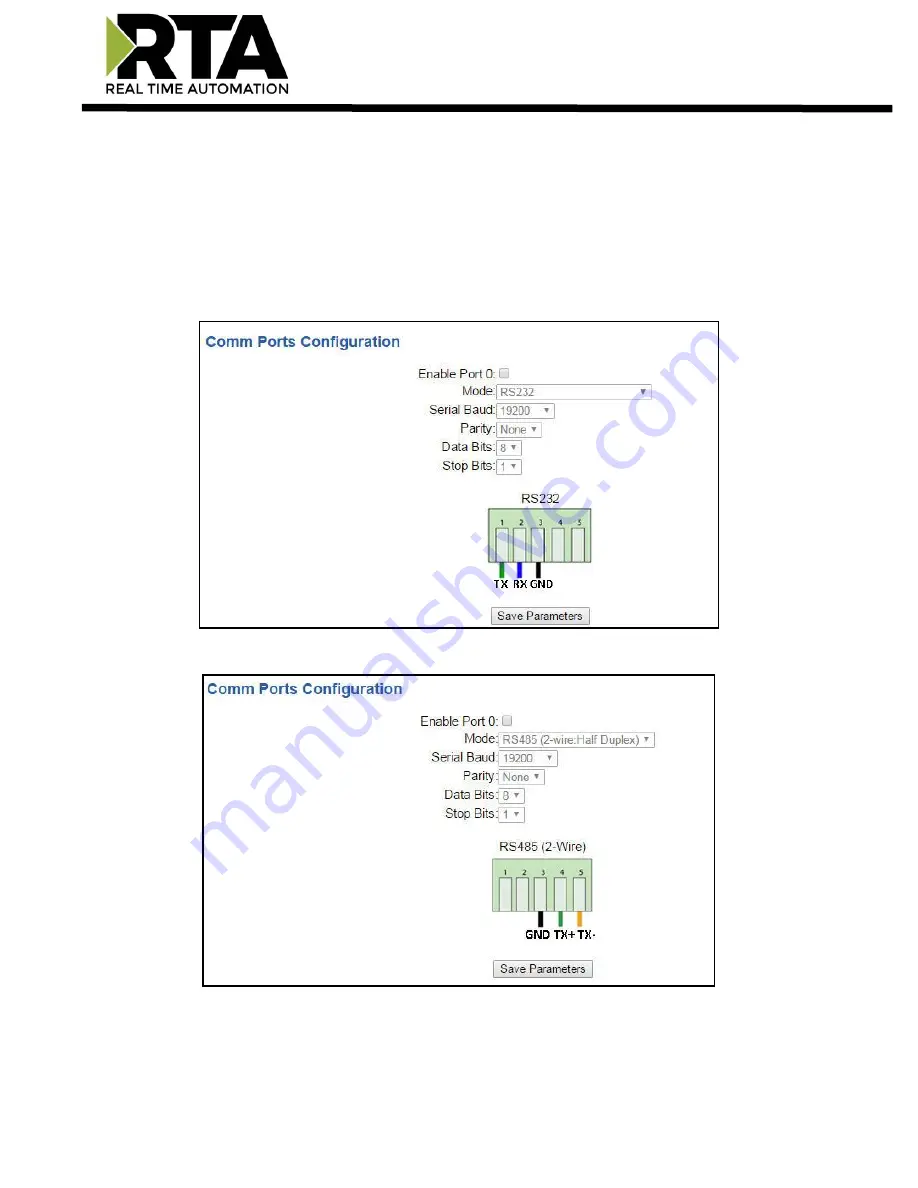
Real Time Automation, Inc.
10
1-800-249-1612
Port Configuration
The Port Configuration page is where you set port specific parameters. These settings must match the
settings of the device(s) that you are connecting to.
Only 1 mode can be configured for this hardware. Below are the wiring pinouts for each mode.
When you have completed your port configuration, click the
Save Parameters
button.
RS232 pinouts:
RS485 pinouts: