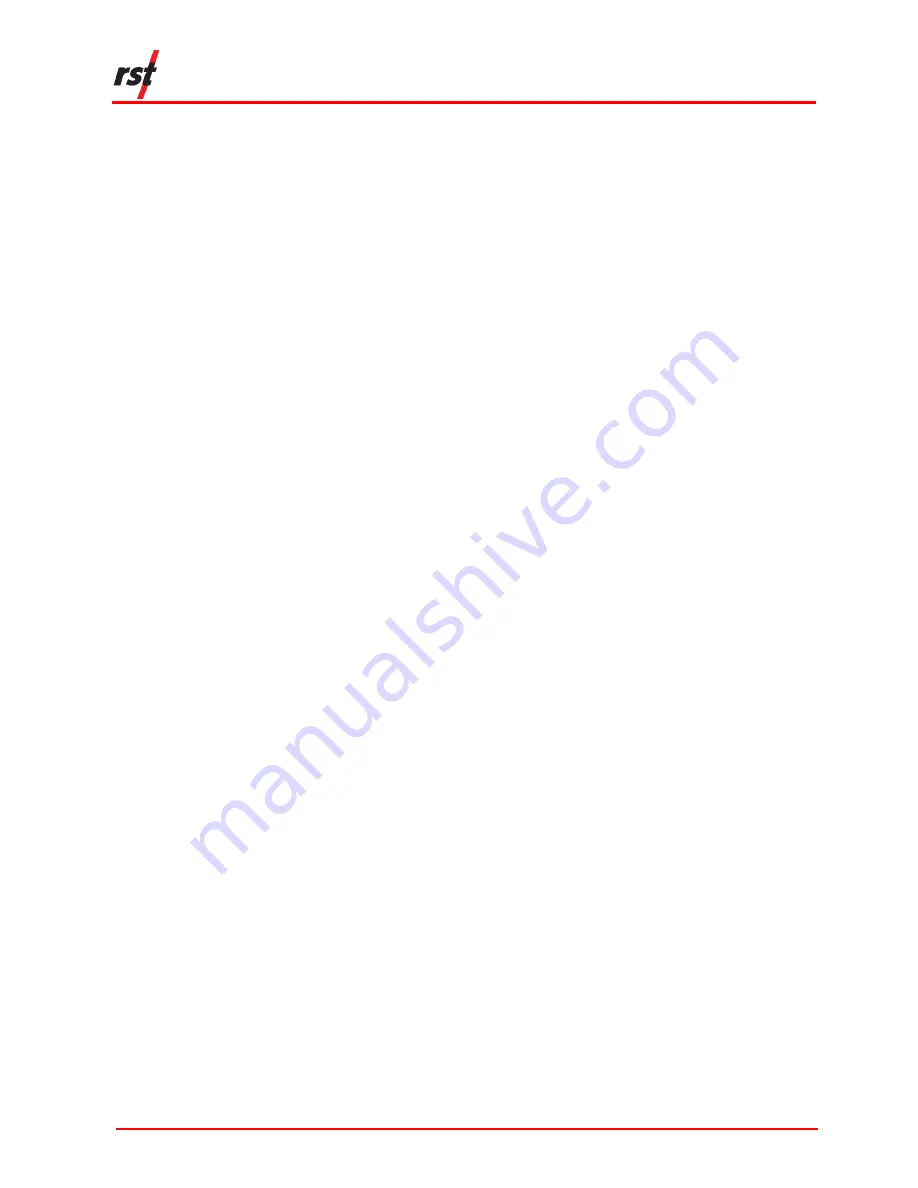
VW2100 Vibrating Wire Piezometer
RST Instruments Ltd.
Page 20
9
Take a second reading on the piezometer.
10
Lift the casing in 15 cm increments and backfill with bentonite chips until a
minimum four-foot seal has been placed. Keep the piezometer cable taut to
prevent the bentonite chips from adhering to the wall of the drill casing during the
bentonite chip placement. Drop the bentonite chips into the hole one at a time to
avoid bridging.
◼
If more than one piezometer is to be installed in the drill hole, the intervening
distance between the top of the first piezometer zone and the bottom of the
next piezometer zone can be backfilled with either cement grout or
cement/bentonite grout delivered by tremie method. The second piezometer
can then be constructed in the same general manner as described above.
11
Top off the borehole collar with grout and a protective steel collar casing once all
the drill casing has been removed from the hole.
5.5.2
Fully Grouted Method
The fully grouted method of piezometer installation involves the installation of the
vibrating wire piezometers directly within a cement-bentonite grout mixture. This
method has now become widely accepted based on the technical theory and on
extensive field testing and application. It provides a simple and accurate method to
obtain precision piezometric monitoring results. Refer to Mikkelson & Green (2003)
and Contreras et al. (2008) in Appendix F for more details on this method.
The general method described below was taken from the two above technical papers
and outlines the basic concepts and methodology of the Fully Grouted Method:
When using the fully grouted method, it is very important that proper filter saturation
is performed. This ensures that there are no air-filled voids in the filter and that
cement-bentonite grout will not be able to plug the filter stone. The best practice is to
install the piezometers upside down with the filter tips facing upwards which will
ensure that the water stays inside the filter stone. The piezometer can be inverted
and tied off to its own cable or it can be inverted and taped onto a PVC pipe which
can be used as either a downhole carrier pipe or as a tremie pipe for grout delivery.
The design of a bentonite-cement mixture is intended to approximate the strength
and deformation characteristics of the surrounding soil or rock (rather than the
surrounding permeability). The strength of the grout can be controlled by adjusting
the Water-Cement ratio which is easy to control in the field. The water and cement
are mixed first prior to adding any bentonite. This ensures that the water-cement
ratio stays fixed and the strength/modulus of the mix is more predictable. Any type of
bentonite drilling mud can be combined with Type I or II Portland Cement to make
the mix. The quantity of bentonite powder will vary depending on the grade of the
bentonite, the mixing agitation, the water pH, and the water temperature. As the
bentonite solids content increases, the mix density increases and the permeability
decreases.
The final mix point has to be carefully monitored to ensure that the completed grout
remains pumpable. Although the grout mix has a target bentonite content, it may be