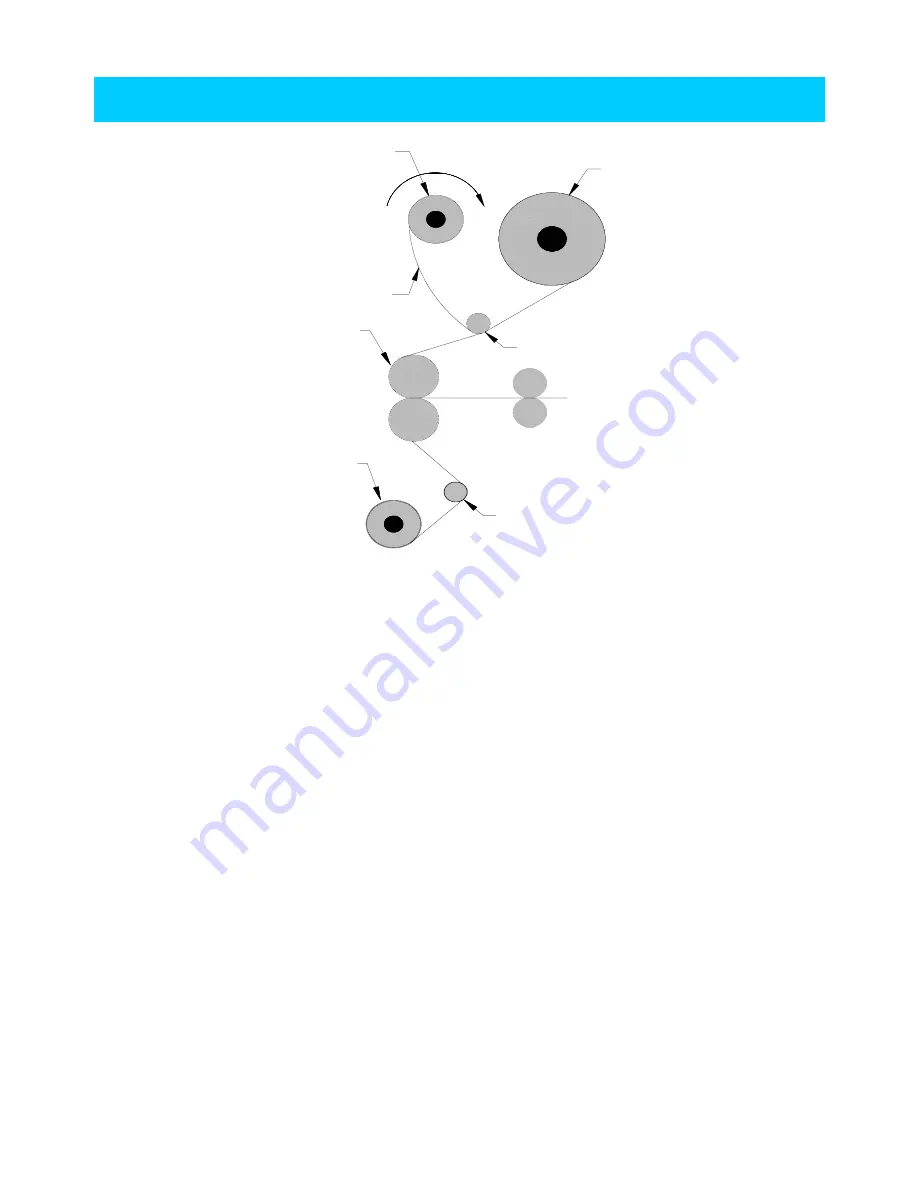
1. Set up cold film below the upper bar of the machine.
(Set the same as methord of the HOT film for protect paper of lower part)
2. Set the pressure lever to the 15mm, open mode.
3. Insert a piece of wide cardboard (guiding paper/carrier) between the rollers.
4. Pull the film from the upper roller passing over the upper idle bar to the upper roller and put it
on the upper roller.
5. Put the paper back of the film to the bobbin at take-up bar to rewind the paper back.
6. Allow some of the film with melted resin to stick to the Guiding Paper.
7. Place the film from lower shaft beneath the film from the upper roller which is already meiting.
and unwind films of both rollers 30~40cm(1~1.3ft) for loosing the tension.
8. Set the pressure lever to the 1mm.
9. Set speed at 1 and press the RUN button. The films will be fed into the machine and will come
out from the rear site of machine.
10. Check the status of lamination and place the pressure lever at lamination mode.
HANGING FILM
TAKE UP DEVICE
PAPER BACK
COLD FILM
UPPER IDLE BAR
LOWER IDLE BAR
HOT ROLLER
PAPER BACK
- 7 -