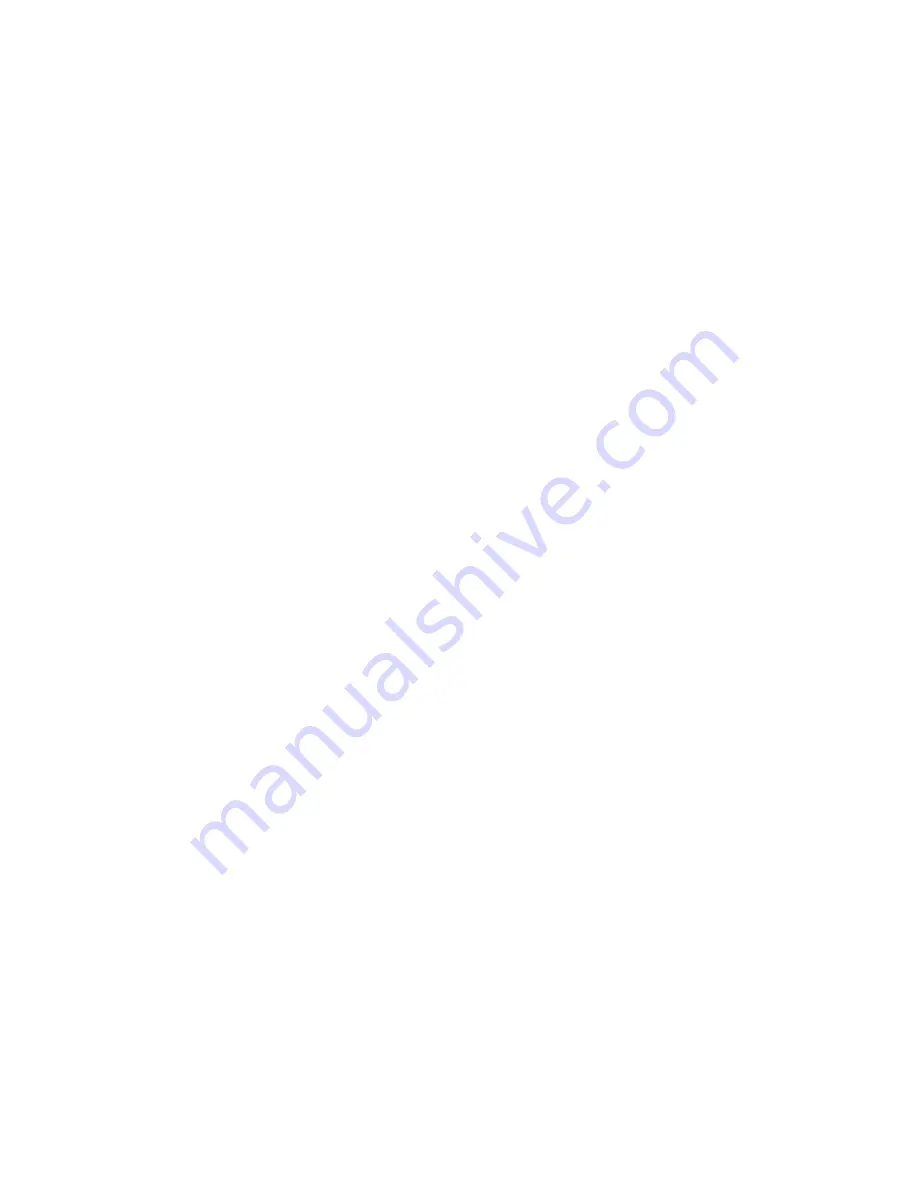
16
machined flat. On these units when re-fitting the
skeg a suitable jointing compound should be used.
Place the skeg (162) in position on the housing,
ensuring that the tabs on the thrust washers (211)
locate in their respective slots in the skeg. Secure
the skeg with the ten socket screws (163) and
sealing washers (129). Fit the rear seal housing
retaining circlip (217).
Fit the clutch operating lever pivot pin (155) and
washer (156) to the skeg, ensuring that it is
correctly located in the clutch operating lever (153).
Replace the zinc ring (218) in the boss surrounding
the propeller shaft and secure with two socket
screws (219).
Refit the distance piece, propeller, lock washer and
spinner nut. With the spinner effectively tightened,
secure with the locking washer tabs.
Refill the unit to the correct level with oil. Oil
capacity of the unit is 8'/z pints (4.8 litres). E.P. 90
gear oil should be used.
6. To Disassemble the Drive Body (Upper)
Remove the eight screws (171) securing the top
cover (167) to the housing and remove the top
cover and joint (170).
Remove the six socket screws (140) and spring
washers (179) which retain the bevel gear bearing
housing (177) to the body. Withdraw the bearing
housing and joint (178) from the body.
Using a suitable extractor, carefully remove the
bevel gear (192), roller bearing (165) and ball
bearing (166) from the bevel gear bearing housing
(177).
Remove the circlip (203) from the universal joint
and input shaft assembly (199). Using a suitable
press, remove the universal joint from its bearing
(22).
Remove the two circlips (23) from the housing and
press the universal joint shaft bearing (22) from the
housing.
Withdraw the vertical drive shaft bevel gear (192).
Before the bearings (165 and 166) can be
removed, the vertical drive shaft (194) and collar
(198) must be withdrawn. This can be
accomplished by dismantling the lower housing as
described in the earlier section. The vertical drive
shaft can be withdrawn and using a suitable
extractor, remove the vertical drive shaft bevel
gear (192), roller bearing (165), ball bearing (166)
and collar (198) from the housing.
If renewal of the centre swivel pin bushes (45) is
intended, press out in the normal manner.
Thoroughly clean and inspect all components for
wear, pitting and cracks, etc. Renew worn or
defective parts.
To Reassemble the Drive Housing (Upper)
If the centre swivel bushes (45) have been
removed for renewal, fit new bushes.
Fit the ball bearing (166) roller bearing (165) to the
housing, ensuring that the bearings are fitted to the
full extent of their recesses. Replace the vertical
drive shaft (194) and ensure that collar (198) is
correctly positioned and reassemble the lower
housings, as described in the earlier section. Re-fit
the vertical drive shaft bevel gear (192).
Fit the inner bearing circlip (23) to the housing and
fit in the universal joint shaft bearing (22). Fit the
second of the circlips (23).
Press
the universal joint and input shaft assembly
(199) into its bearing (23) and secure with the
circlip (203).
Fit the ball bearing (166), roller bearing (165) and
bevel gear (192) to the bevel gear housing (177)
ensuring that the races fit in to the full extent of
their recesses.
Fit the bevel gear bearing housing (177) to the
body (161) using a new joint (178) and secure with
the six socket screws (40) and spring washers
(179). With the aid of a feeler gauge, check the
backlash between the top bevel gear and the
vertical drive shaft bevel gear. Clearance between
these two gears should be within the limit of
0.008
in to 0.012
in. (0.20/0.30 mm). Adjustments to the
clearances is obtained by the addition of extra
joints (178) to the bevel gear housing (177).
Assemble the top cover (167), using a new joint
(170) to the housing and secure with the eight
screws (171).
Summary of Contents for Z-Drive 130
Page 1: ...1 ENFIELD Z DRIVE TRANSOM UNITS SERVICE MANUAL AND PARTS LIST LEICESTER ENGLAND ...
Page 9: ...9 ...
Page 20: ...20 ...
Page 22: ...22 Plate B Model 130H Assy ...
Page 26: ...26 ...
Page 27: ...27 ...