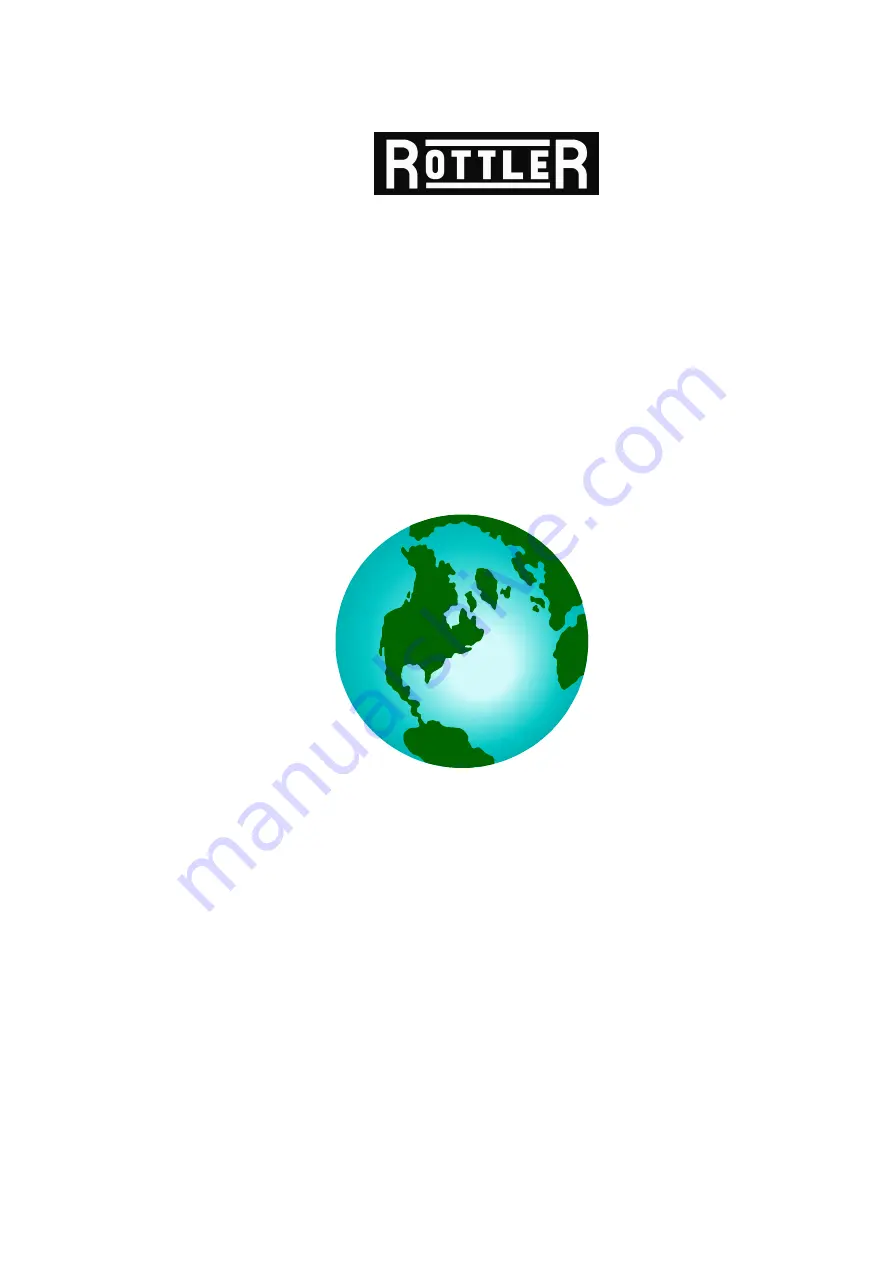
MANUFACTURING
SG9A
Automatic Seat and Guide Machine
Serial No.: _______________________
Company: _______________________
OPERATIONS AND MAINTENANCE
MANUAL
MANUFACTURED BY:
ROTTLER MANUFACTURING COMPANY
8029 South 200th Street
~ Kent, Washington
98032 USA
Phone:
(253) 872-7050
Fax:
(253) 395-0230
NOTE: WHEN ORDERING REPLACEMENT PARTS,
PLEASE GIVE THE MODEL AND SERIAL NUMBER.
ORDER BY PART NUMBER.
THERE IS A MINIMUM ORDER OF $25.00