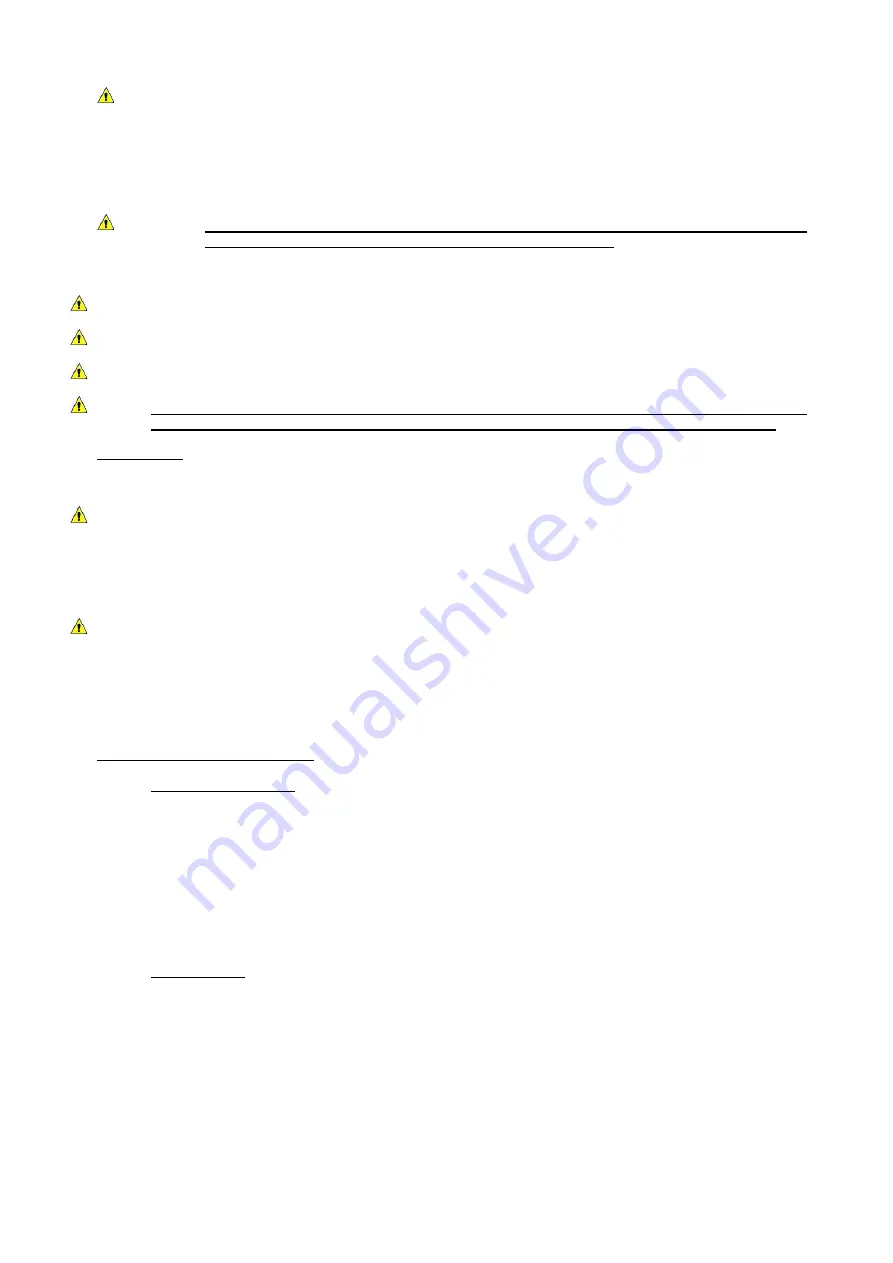
IM No. : IM/V/00063
Rev. 1 dtd. 23.05.2017
Page 3 of 5
j)
In case if the valve is used for dangerous fluid gas/liquid then, the user is hereby advised to maintain
during operation and maintenance of the valve below LEL or above UEL to avoid explosion due to
internal spark as the valves have not been assessed for the same.
k)
Inlet pressure does not exceed rated pressure.
l)
Hemp-
Filaments, ’Jute’ or even Teflon-Ribbons are normally not required, as the port connections of
ROTEX Valve is accurately machined.
m)
To avoid overlap of the Teflon ribbon or cuts generated while tightening, getting carried away into
the valve. Do not cover first two thread pitches with Teflon tape or sealant.
n)
For Solenoid Valve to be installed in European Union, check the applicability for ATEX. Refer
separate Instruction Manual for ATEX approved Solenoid Valve.
2.
The process fluid etc. : do not fall on the valve body.
3.
In case if the surrounding atmosphere has traces or some other substance other than Air, check its
compatibility with the Body material of the valve, Solenoid enclosure & other exposed parts.
4.
In case if the valve is installed in potentially Hazardous area, check for the temperature class of the Solenoid
to avoid explosion due to heated Solenoid / other components.
5.
Provide fuse of proper rating to avoid excess current passing through the Solenoid and thereby avoiding
overheating.
6.
It is not likely however the user is advised to protect the valve against lightening as the same is not assessed.
7.
Check internal components (wetted) parts for its compatibility with fluid passing through the valve.
8.
It is recommended to replace all the Rubber Parts including Plunger Assembly (Repair Kit
– Code 99)
in case if the valve is to be installed and put in service after 2 years from the date of manufacture.
ELECTRICAL
1.
Verify name plate affixed on the Solenoid.
2.
Connect the power supply according to the voltage rating of the Solenoid
3.
Ensure that the cover of Junction Box/Terminal Box is properly tightened wherever applicable.
4.
Install valve in such a way that the rain water / other process fluid dripping along the cable does not fall on the
SOV and has no possibility to run along the cable and enter into the Terminal area.
5.
Fill in the space between cable and gland entry with a proper sealant. If necessary, you may mount the valve
upside down or in any other direction.
6.
Ensure that the Solenoid enclosure meets process and local authority requirement.
7.
The Plug In, Terminal Box, FPJB, IS Solenoids are provided with test leads. Remove them before final
installation.
8.
Check for proper connections for the Solenoid which are polarity sensitive e.g. (a) Latched Solenoid (b) Ex ia
Solenoid.
9.
Ensure that the solenoid construction is selected properly meeting the environment in which the valve is
supposed to be installed e.g. use of Exd or Ex ia solenoid for valve to be installed in hazardous location or
Weatherproof Solenoid having IP 67 for outdoor installation.
10.
Refer separate manual for construction of the Solenoid and for specific instructions related to Solenoid e.g.
(a) Ex ia (b) Latched Solenoid (c) Ex d Solenoid IP 67.
MANUAL OVERRIDE OPERATION
(A) PUSH AND TURN (M6)
In normal position of the manual override, applied pressure at Inlet port # 2, a part of media pressure passed from
bleed hole of diaphragm to surrounding hole of Duse to tube hole to out let port # 1. thus, pressure released from top
of the diaphragm assembly and it is moves up. In this state, Inlet port # 2 and Outlet port # 1 is connected. Media
come from outlet.
To operate the manual override push and turn it clockwise, thus plunger assembly moves up and blocked the pilot
passage, now applied pressure at Inlet port # 2, media pressure act on the diaphragm assembly from bleed to keep
downwards. In this state, Inlet port # 2 and Outlet port # 1 is disconnected. Media cannot come out. To retail the valve
at home position push and turn anti clockwise.
(B) PUSH MA (M8)
In normal position of the manual override, applied pressure at Inlet port # 2, a part of media pressure passed from
bleed hole of diaphragm to surrounding hole of Duse to tube hole to out let port # 1. thus, pressure released from top
of the diaphragm assembly and it is moves up. In this state, Inlet port # 2 and Outlet port # 1 is connected. Media
come from outlet.
To operate the manual override push it, thus plunger assembly moves up and blocked the pilot passage, now applied
pressure at Inlet port # 2, media pressure act on the diaphragm assembly from bleed to keep downwards. In this state,
Inlet port # 2 and Outlet port # 1 is disconnected. Media cannot come out. To retail the valve at home position released
the manual override.