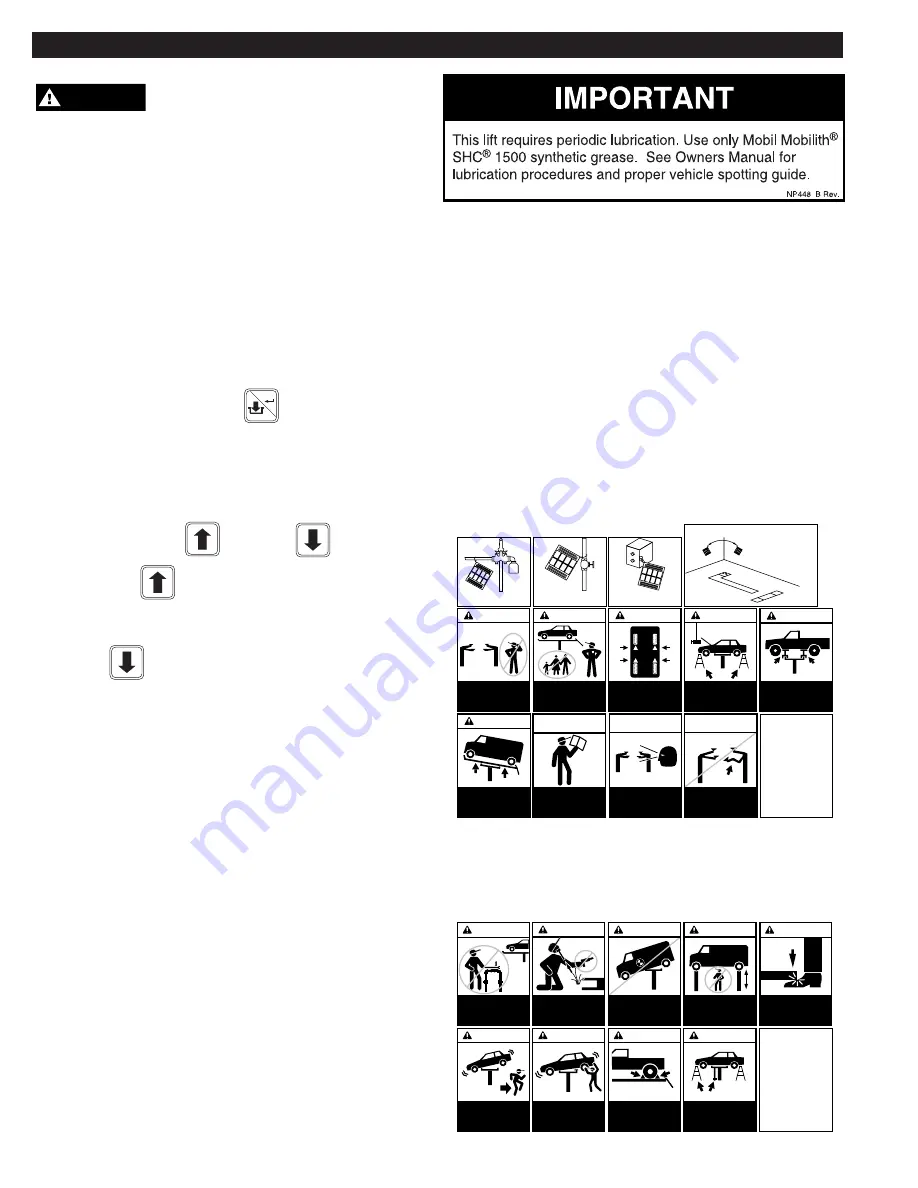
10
Safety Warning Labels
for Inground Lifts
Lift Owner/User Responsibilities:
A.
This Safety Warning placard, see below, SHALL be
displayed in a conspicuous location in the lift area.
B.
Use one of the mounting arrangements illustrated on
back of this placard.
C.
These Safety Warning labels supplement other docu-
ments supplied with the lift.
D.
Be certain all lift operators read and understand these
labels, operating instructions and other safety related
information supplied with the lift.
CAUTION
Lift to be used
by trained operator
only.
©
? ?
?
CAUTION
Authorized personnel
only in lift area.
©
CAUTION
Use vehicle
manufacturer’s
lift points.
©
CAUTION
Always use
safety stands when
removing or installing
heavy components.
©
Do not operate
a damaged lift.
©
SAFETY
INSTRUCTIONS
Read operating
and safety manuals
before using lift.
©
SAFETY
INSTRUCTIONS
The messages and pictographs
shown are generic in nature and
are meant to generally represent
hazards common to all automotive
lifts regardless of specific style.
Funding for the development and
validation of these labels was
provided by the Automotive Lift
Institute, PO Box 33116 Indialantic,
FL. 32903-3116.
They are protected by copyright.
Set of labels may be obtained from
ALI or its member companies.
ALI/WL500cs
1992 by ALI, Inc.
TYPICAL PLACARD LOCATIONS
STO
P
STAR
T
Air Supply To Lift
Push Button Controls on
Electric Powered Lifts
Wall Mounted Lift
Control
CAUTION
Use height extenders
when necessary
to ensure
good contact.
©
Proper maintenance
and inspection
is necessary
for safe operation.
©
SAFETY
INSTRUCTIONS
CAUTION
Auxiliary adapters
may reduce
load capacity.
©
In-floor Lift Controls:
Locate placard on wall or
column in lift area near lift
controls
WARNING
Do not override
self-closing
lift controls.
©
WARNING
DO NOT remove oil
fill plug before reading
manufacturer's
manuals.
©
WARNING
Position vehicle
center of gravity
over lift.
©
WARNING
Remain clear of lift
when raising or
lowering vehicle.
©
WARNING
Chock wheel
to prevent
vehicle movement.
©
WARNING
Clear area if vehicle
is in danger of falling.
©
WARNING
Avoid excessive
rocking of vehicle
while on lift.
©
The messages and pictographs
shown are generic in nature and
are meant to generally represent
hazards common to all automotive
lifts regardless of specific style.
Funding for the development and
validation of these labels was
provided by the Automotive Lift
Institute, PO Box 33116 Indialantic,
FL. 32903-3116.
They are protected by copyright.
Set of labels may be obtained from
ALI or its member companies.
ALI/WL500w
1992 by ALI, Inc.
SAFETY WARNING LABELS FOR INGROUND LIFTS
Lift Owner/User Responsibilities:
A.
This Safety Warning placard
SHALL
be displayed
in a conspicuous location in the lift area.
B.
Use one of the mounting arrangements illustrated
on back of this placard.
C.
These Safety Warning labels supplement other
documents supplied with the lift.
D.
Be certain all lift operators read and understand
these labels, operating instructions and other
safety related information supplied with the lift.
WARNING
Use lift locking device
or 4 stands
to support vehicle.
©
or
Keep feet
clear of lift
while lowering.
©
WARNING
WARNING
If you are not completely familiar with
automotive lift maintenance procedures
STOP
. Contact factory
for instructions. To avoid personal injury, permit only qualified
personnel to perform maintenance on this equipment.
Always
keep locking latch free and oiled.
Always
keep all bolts tight.
Always
keep superstructure clean. In salt belt or other corrosive
environments, the lift must be washed down weekly.
Always
make sure the perimeter of the guide barrel and center
cover are sealed with a good grade of silicone.
NOTE
Be sure plugs on superstructure's are in place.
Daily
inspect adapters for damage or excessive wear. Replace as
required with genuine Rotary parts.
Daily
check locking latch operation.
If locking latch is not heard when lift is raised:
A.
Lower loaded lift onto lock
SELECT
LOWER TO LOCKS
, to check if lock is
functioning. If lock is functioning, stop. If not, continue on to
"Step B".
B.
Remove center cover and raise unloaded lift to full rise.
C.
Check locking latch for damage or air line problem.
D.
Repair and lubricate locking latch pivot points.
E.
Raise lift off lock
. Lower lift
about half way.
Then raise lift
and watch locking latch operation.
F.
The air cylinder should allow locking latch to pivot in and
out of the latch bar.
G.
Push
to lower lift.
H.
Replace center cover and torque bolts to 60 ft-lbs.
I.
Seal around the perimeter of the guide barrel and center
cover with a good grade of silicone.
Monthly
lubricate lift guide barrels.
Guide Barrel Lubrication:
A.
Each guide barrel has a grease fitting on the top of the
guide barrel.
B.
While raising and lowering unloaded lift, give each guide
barrel 10-12 pumps with "hand" (manual) grease gun using
only Mobil Mobilith
®
SHC
®
1500 synthetic grease.
C.
For your nearest Mobil Mobilith
®
SHC
®
1500 synthetic
grease source, call 1-800-662-4525 or your local Rotary
distributor.
Semi-annually
check fluid level of lift power unit and re-fill if
required per installation instructions using Dexron III ATF or
ISOVG32 Hydraulic Fluid.
Replace
all caution, warning or safety related decals on the lift if
unable to read or missing. Reorder labels from Rotary Lift, see
Safety Warning Labels for Inground Lifts.
Replace
IMPORTANT
decal on outside of yokes if unable to
read or missing. Reorder labels from Rotary Lift, NP448.
MAINTENANCE INSTRUCTIONS