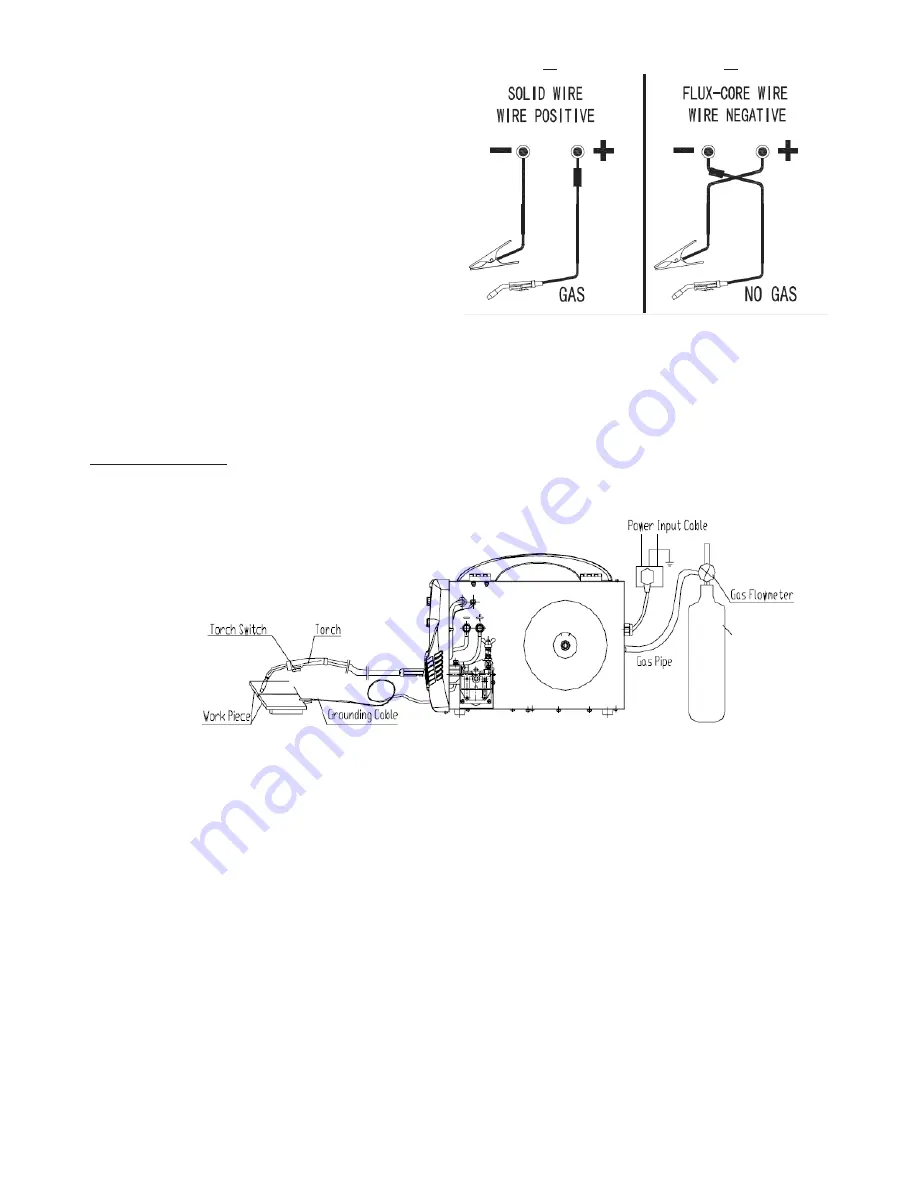
POLARITY SELECTION
The correct polarity must be set for the type of
welding used.
When using solid wire in conjunction with weld-
ing gas, connect the torch to the positive ter-
minal and the earth clamp to the negative. See
diagram A.
When using flux cored wire (gasless) connect the
negative terminal to the welding torch and the
earth clamp to the positive. see diagram B.
Note: The welder MUST be set to manual mode
for gasless welding using flux cored wire. (see [7] & [8]
CAUTION!
Check that terminals are tight before commencing to weld to prevent burning
A
B
MIG WELDING
Typical setup
LOADING THE WIRE
• Open the side cover of the unit
• Fit the wire spool onto the spool holder [B] so that the wire will exit the spool from the bottom. Check that
the spigot fits correctly into the reel.
• Note the reel holder suits 200 mm reels.
Adjust the back tension knob [C] as light as possible but sufficiently strong to prevent the wire roll from self
un-spooling)
• Fit the torch to the euro fitting and firmly tighten.
• Release the tension screw [G] and open the upper roller arm [E]
• Without letting the wire un-spool, cut the end of the wire of cleanly leaving no kinks the feed about 30cm of
the wire through the guide tube and into the wire liner by hand.
• The wire feed roller has two different size groves. Check that the wire is aligned with the correct size grove in
the wire feed roller for the type of wire and then careful close the upper roller and tension screw. If necessary
remove the wire feed roller and turn it over to access the other grove and refit.
• At the end of the torch
• Twist the nozzle clockwise and pull to remove
Welding Gas
PREPARING FOR MIG WELDING
Summary of Contents for RXT200EX
Page 2: ......
Page 19: ...NOTES...