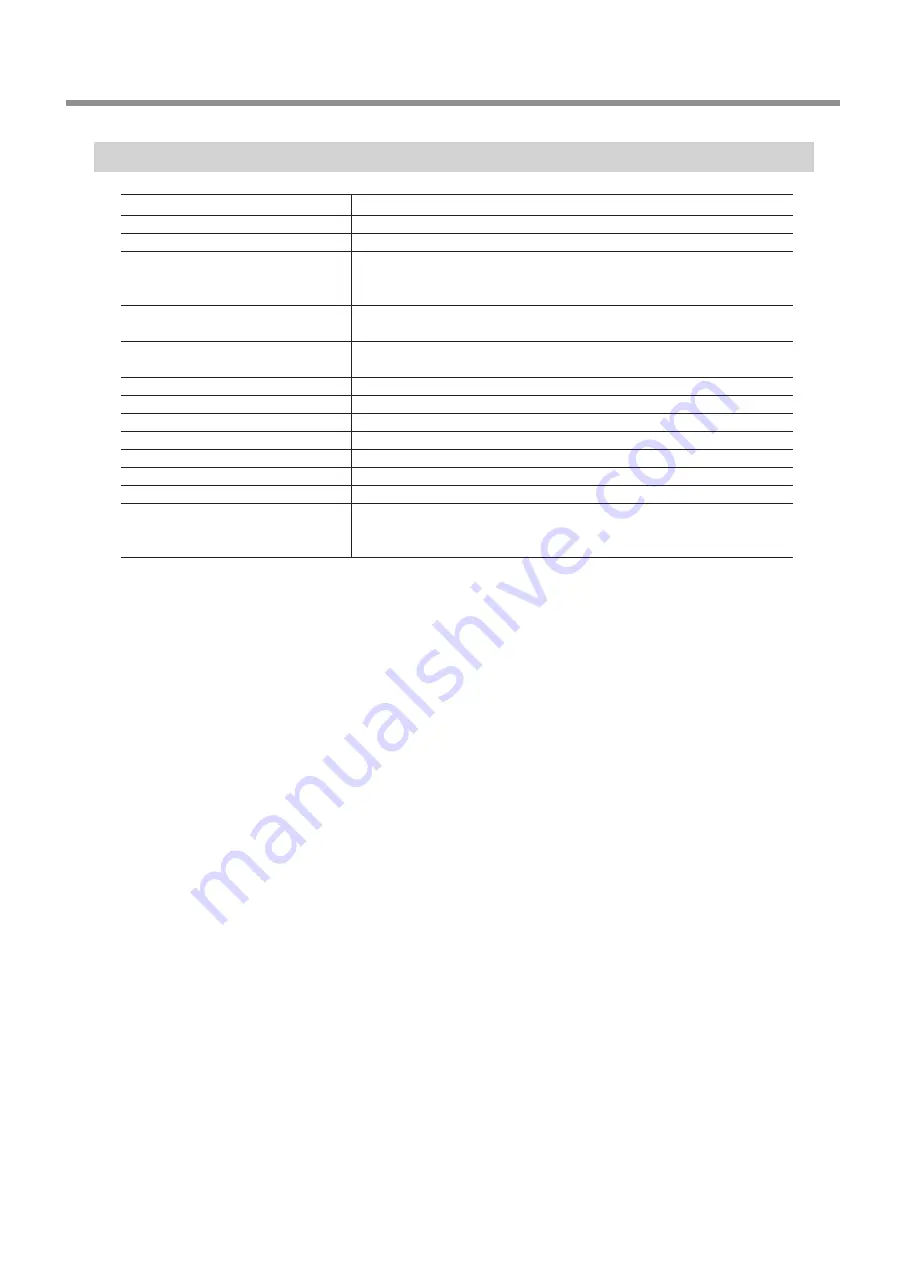
7-4 Unit Specifications
74
Chapter 7 Appendix
Main Specifications
ZCL-540
Supported workpiece
Resin (metal not supported)
Maximum angle of rotation
±2,147,483.647˚ (±5,965.23 turns)
Loadable workpiece size (*)
Items within the range of a 90 mm (3.5 in.) radius from the center of the
rotary
axis by long 371 mm (14.6 in.)
The actual cuttable range is smaller than this.
Workpiece thickness holdable
by workpiece chuck
15 to 100 mm (0.6 to 3.9 in.)
Loadable workpiece weight
Maximum 5 kg (11 lb.), maximum moment of inertia: 0.02 kgm
2
Center drill used: Maximum 1.5 kg (3.3 lb.)
Control method
Simultaneous 4-axis control
Feed rate
Maximum 20 rpm
Software resolution
RML-1 mode: 0.1˚, NC-code mode: 0.01˚
Mechanical resolution
0.002˚
Static precision
Backlash: 0.05˚, Eccentricity: 0.3 mm (0.012 in.) or less
Dimensions
Width x depth x height: 720 x 100 x 195 mm (28.3 x 3.9 x 7.7 in.)
Weight
6.5 kg (14.5 lb.) (total weight including drive unit, tailstock, base plates, etc.)
Included items
Drive unit, tailstock, base plates, live center, center drill, Y-origin sensor, Z-
origin sensor, spacer, origin-detection pin, cap screws, plastic screws, T-slot
nuts, hexagonal wrenches, retaining band, User's Manual
* When the T-slot table is installed, length is 297 mm (11.7 in.).
When this unit is installed, the X-axis travels of the MDX-540S and MDX-540 are as follows.
Standard table, no ATC unit: 285 mm (11.2 in.)/325 mm (12.7 in.) (with expanded X-axis travel)
Standard table, ATC unit present: 270 mm (10.6 in.)/325 mm (12.7 in.) (with expanded X-axis travel)
T-slot table, no ATC unit: 218 mm (8.5 in.)/258 mm (10.1 in.) (with expanded X-axis travel)
T-slot table, ATC unit present: 203 mm (7.9 in.)/258 mm (10.1 in.) (with expanded X-axis travel)
Summary of Contents for MODELA Pro II ZCL-540
Page 2: ......
Page 11: ...9 ...
Page 18: ...16 ...
Page 20: ...18 ...
Page 21: ...19 Chapter 1 Introduction ...
Page 24: ...22 ...
Page 25: ...23 Chapter 2 Installation ...
Page 33: ...31 Chapter 3 Basic Operation ...
Page 42: ...40 ...
Page 43: ...41 Chapter 4 Setting the Origins ...
Page 56: ...54 ...
Page 57: ...55 Chapter 5 Getting Ready for and Performing Cutting ...
Page 62: ...60 ...
Page 63: ...61 Chapter 6 Handy Panel ...
Page 67: ...65 Chapter 7 Appendix ...
Page 77: ...75 ...
Page 78: ...76 ...
Page 80: ...R5 120906 ...