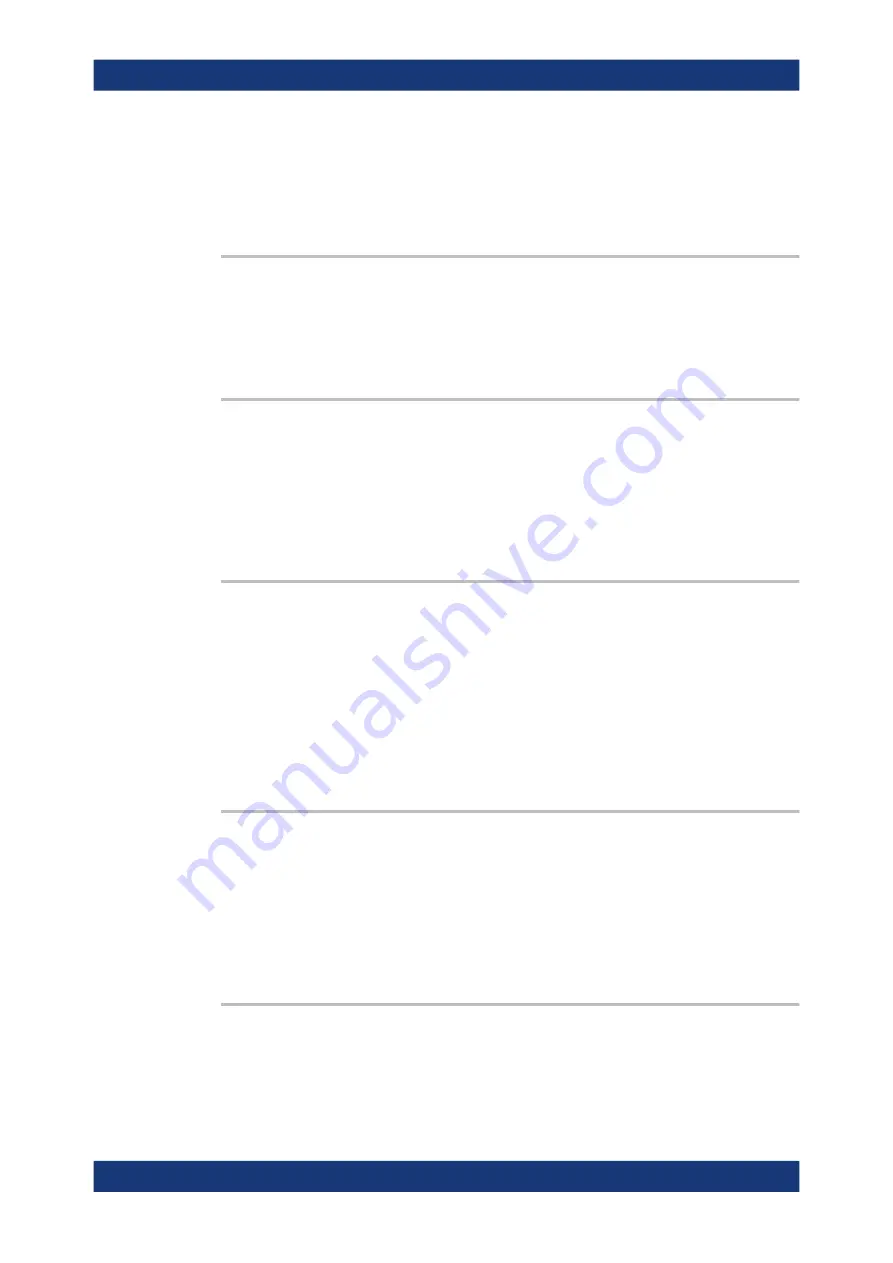
Remote control commands
R&S
®
NRPxxTWG
36
User Manual 1178.8371.02 ─ 08
*OPC?
basically functions like
, but also returns a response. The response is an
advantage, because you can query the execution of commands from a controller pro-
gram before sending new commands. Thus preventing overflow of the input queue
when too many commands are sent that cannot be executed.
*OPT?
Option identification
Returns a comma-separated list of installed options.
Usage:
Query only
*PRE
<register>
Parallel poll register enable
Sets the parallel poll enable register to the specified value or queries the current value.
Parameters:
<register>
Range:
0 to 255
*RST:
0
*RCL
<number>
Recall
Calls the device state which has been stored with the
fied number.
Setting parameters:
<number>
Range:
0 to 9
*RST:
0
Usage:
Setting only
*RST
Reset
Sets the instrument to a defined default status. The default settings are indicated in the
description of commands.
The command corresponds to the
Usage:
Event
*SAV
<number>
Save
Stores the current device state under the specified number.
Common commands