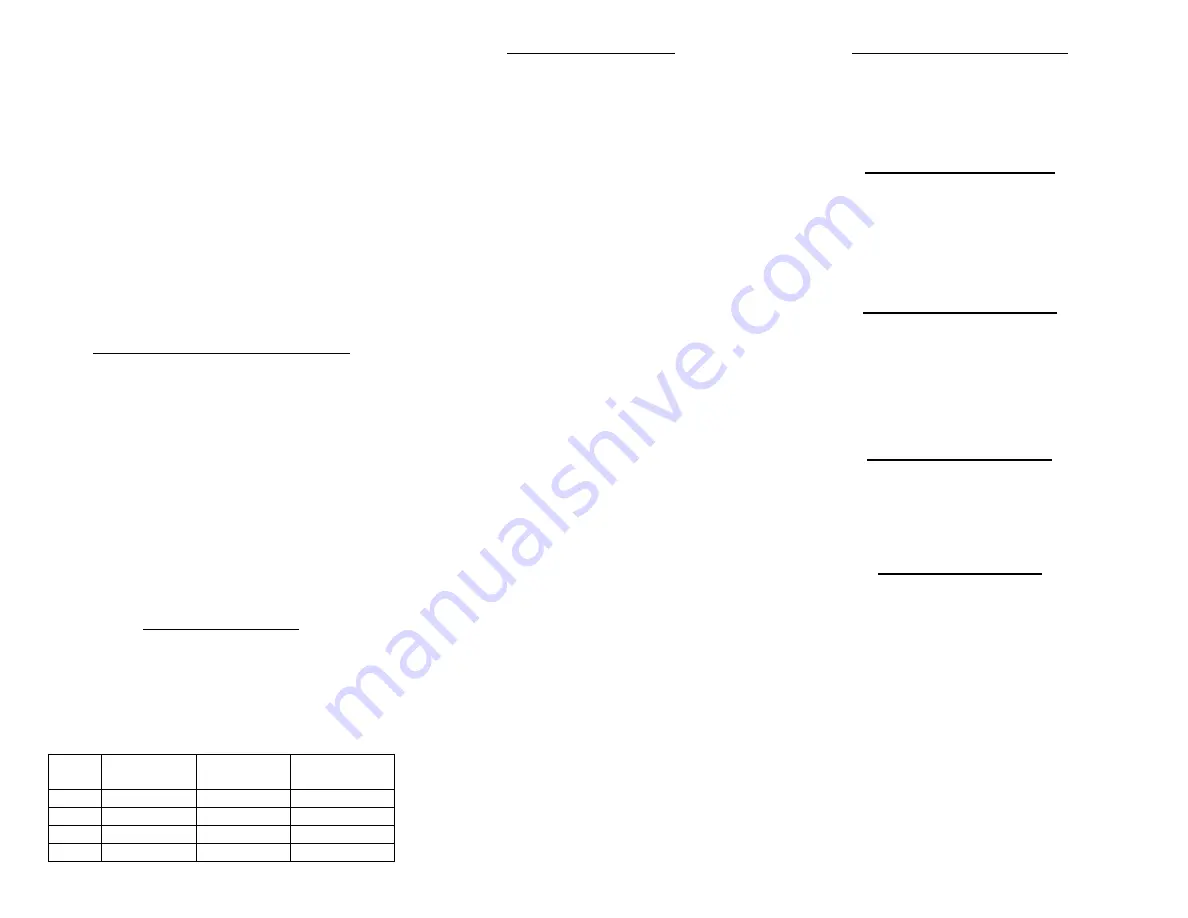
The Min Frequency adjustment specifies the
frequency used when the 0-10VDC input is at
0VDC. The Max Frequency adjustment can be
used to ignore the upper end of the 0-10VDC
signal.
C. 0-10VDC signal from a PLC can be used to
remotely vary the output of the control instead of
the keypad. The “Amplitude Source” setting must
be set to 0-10VDC to enable it. After the 0-10VDC
feature is selected, the control will automatically
turn ON whenever a signal is applied to the control
(TB2- “+0-10” & “-“). When the 0-10VDC signal
has been removed, the amplitude setting resets to
zero.
D. When it is desirable to ignore the external speed
control inputs, the “Manual” setting can be
selected.
12. CFR Positive and Negative Gain
The CFR Positive and Negative Gain settings control
the rate the feeder’s vibration level is corrected by the
control. When the vibration decreases below the set-
point, the “CFR Positive Gain” sets the rate at which
the output gets boosted to compensate for a vibration
decrease. When the vibration increases, the “CFR
Negative Gain” sets the rate at which the output gets
lowered to compensate for a vibration increase. If
either the CFR Positive or Negative gain is set too
low, it will take longer than desired to get back to the
original feed rate. If either gain is set too high, the
control may over-shoot beyond the original feed rate.
The CFR Positive and Negative Gain settings effect
the control’s operation when the CFR sensor is used,
and the “Amplitude Control” is set to “Auto Track.”
13. Current Limit Trip
The current limit comes preset to the maximum value
to protect the control from damage. The current limit
can be lowered to protect the feeder’s coil from
overheating. The load current can be viewed under
the diagnostic menu. If a fault occurs, Press the 1/0
button twice to clear the fault. Control current ratings
are below.
Rating with
120V input
Rating with
240V input
120V Rating
below 16Hz
VF3
3 Amps
2 Amps
2 Amps
VF9
9 Amps
7 Amps
7 Amps
VF12
12 Amps
9 Amps
8 Amps
VF18
18 Amps
12 Amps
12 Amps
14. Frequency Settings
The “Frequency” menu contains the portion of the
menu that controls the frequency settings. The
frequency can be adjusted from 5 to 140Hz (or 180Hz
on VF-3 and VF-9 controls). The spring/mass ratio
of the vibratory bowl determines the natural vibrating
(resonate) frequency of the bowl. The control’s
output frequency needs to be adjusted to match the
natural frequency of the bowl. The control can be
manually tuned or automatically tuned. The
frequency setting is displayed as “F= 120.0Hz.”
The “Frequency Mode” setting selects either manual
frequency adjustment or auto tracking frequency
adjustment.
A. Manually finding the resonate frequency of the
bowl is much like finding a station on the AM radio
band. Set the amplitude to about 30%. Then
adjust the frequency across its range. The bowl
should be expected to vibrate the parts at more
than one spot across the frequency range. The
resonate frequency is the frequency with the most
vibration. Once the best feeding frequency range
has been found, fine tune the frequency for the
best parts movement. To increase feeder stability
for parts load fluctuations, adjust the frequency
down by .2 or .3Hz so that the feeder becomes
slightly over-tuned.
B. “Auto Scan” scans to locate the bowl’s resonate
frequency. Once auto tracking has found the
resonate frequency, it can maintain the resonate
frequency and amplitude of the feeder as the parts
load changes. The CFR sensor is needed in order
for auto tracking to operate, and “Auto Tracking”
needs to be turned on under both “Amplitude
Source” and “Frequency Mode” menus.
To show when frequency “Auto Tracking is
enabled, the normal display menu will show a bold
“
F
.” When ”
=
” is shown in bold, the control is
locked onto the resonate frequency of the feeder.
C. The frequency can be adjusted with an analog 0-
10 volt input when the amplitude source setting is
set to 4-20mA.
The Minimum frequency limit can protect the feeder
from feeding at a low frequency if a spring or weld
breaks. The Min. or Max. frequency can block out
undesirable frequencies during Auto Scan.
To
avoid
coil damage and blown fuses
during an
Auto Tune scan, the Minimum frequency
should only
be adjusted below the 45Hz
default
when the
vibratory feeder has been specifically designed for
operation below 45Hz.
15. Resonate Threshold Level
The “Resonate Threshold Level” setting sets the
minimum level of vibration that the control considers
as a resonate condition during an Autoscan. The
setting should be reduced if a “Coarse Scan Error” is
given after two scan attempts. Adjustment is not
normally needed except for some inlines.
16. Auto Track Dead Band
The “Auto Track Dead Band” setting controls how far
the resonant frequency of the vibratory feeder can
deviate before the output frequency of the control is
adjusted to follow it. Decreasing the setting narrows
the range, and increasing the setting makes the dead
band range larger before a reaction takes place.
This setting normally doesn’t need to be changed.
17. Setting the Time Delays
The ON and OFF parts-sensor time-delays are set
independently for a period of 0-20 seconds. The time
delay settings can be adjusted to provide the best
individual response for the feeder. The time delays
can be found under the timer settings menu. The
flashing “=” blinks every quarter second to show when
either the ON or OFF delay timer is running.
18. Parts Sensor Settings
The “I/O Interface” menu contains the portion of the
menu that controls the parts sensor polarity.
The control comes preset to “inverted” sensor
polarity. Set the sensor polarity to either “Normal”
(through beam) or “Inverted” (proximity or retro-
reflective). The sensor input accepts a PNP sensor.
19. Run Mode Settings
The “I/O Interface” menu contains the menu portion
that controls the run mode and empty bowl logic.
A. The control comes preset for normal on/off parts
sensor operation. The following can be chosen:
1) The “Constant On” feature can be used to keep
the bowl running while the Aux output switches
power to a device (air valve, SSR, or relay).
2) The “2-Speed” feature allows the bowl to keep
some vibration going to either trickle parts for
weigh counting or to cut down the time to full
speed when a high feed rate is needed. The parts
sensor switches between high and low speed
settings. Low speed is set by “Min Amplitude.”
3) The “high/low” function maintains the parts
level between two parts sensors on the track. The
second sensor (PNP) gets installed in place of the
run jumper.
10/21/20 Page 6