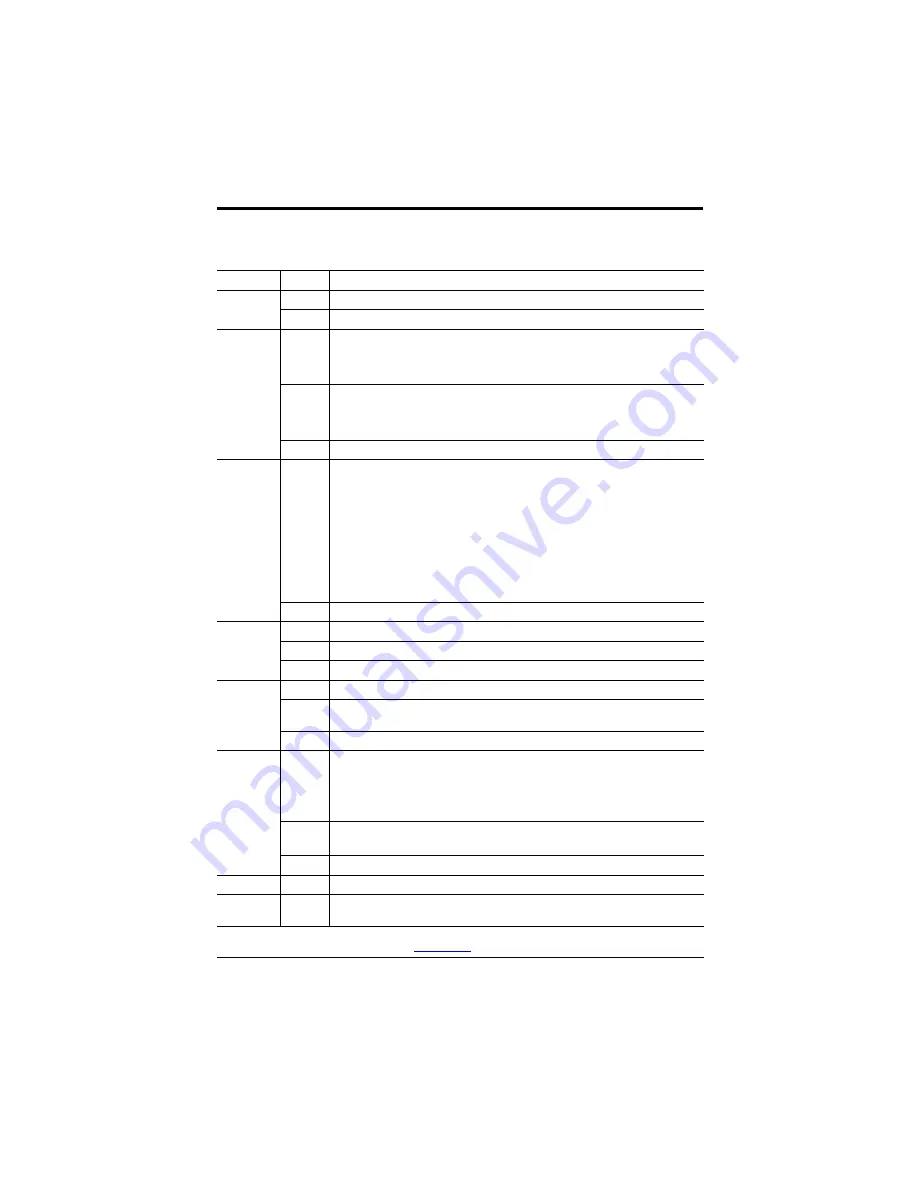
GuardPLC Digital Input/Output Module
13
Rockwell Automation Publication 1753-IN003C-EN-P - June 2010
Status Indicators
Indicator
State
Description
24V DC
On
24V DC operating voltage present.
Off
No operating voltage.
RUN
On
This is the normal status of the controller.
A routine, which has been loaded into the controller, is executed.
The controller processes input and output signals, carries out communication, and
performs hardware and software tests.
Flashing
The controller is in STOP mode and is not executing a routine.
All system outputs are reset.
STOP mode can be triggered by setting the
Emergency stop
system variable to TRUE
in the routine, or by direct command from the programming software.
Off
The controller is in ERROR_STOP mode (see ERROR).
ERROR
On
•
A hardware error has been detected by the controller. The controller goes to
ERROR_STOP mode and the execution of the routine is halted. Hardware errors
are errors in the controller, errors in one or more of the digital input and output
modules, or errors in the counters.
•
A software error in the operating system has been detected by the controller.
•
The watchdog has reported an error due to exceeded cycle time.
All system outputs will be reset and the controller ceases all hardware and
software tests. The controller can only be restarted by a command from the
programming software.
Off
No errors are detected.
PROGress
On
The upload of a new controller configuration is in progress.
Flashing
The upload of a new operating system into the nonvolatile ROM is in progress.
Off
No upload of controller configuration or operating system in progress.
FORCE
On
The controller is executing a routine (RUN) and FORCE mode is activated by the user.
Flashing
The controller is in STOP mode, but Forcing has been initiated and will be activated
when the controller is started.
Off
Forcing is OFF.
FAULT
On
•
The routine (logic) has caused an error.
•
The controller configuration is faulty.
•
The upload of a new operating system was not successful and the operating
system is corrupted.
Flashing
An error has occurred during a nonvolatile ROM write cycle.
One or more I/O errors have occurred.
Off
None of the above errors has occurred.
OSL
Flashing
Emergency
O
perating
S
ystem
L
oader is active.
BL
Flashing
B
oot
L
oader unable to load operating system or unable to start COMM operating
system loader.
Module status can be interrogated through the programming software. For more information, refer to the
GuardPLC System User Manual, publication