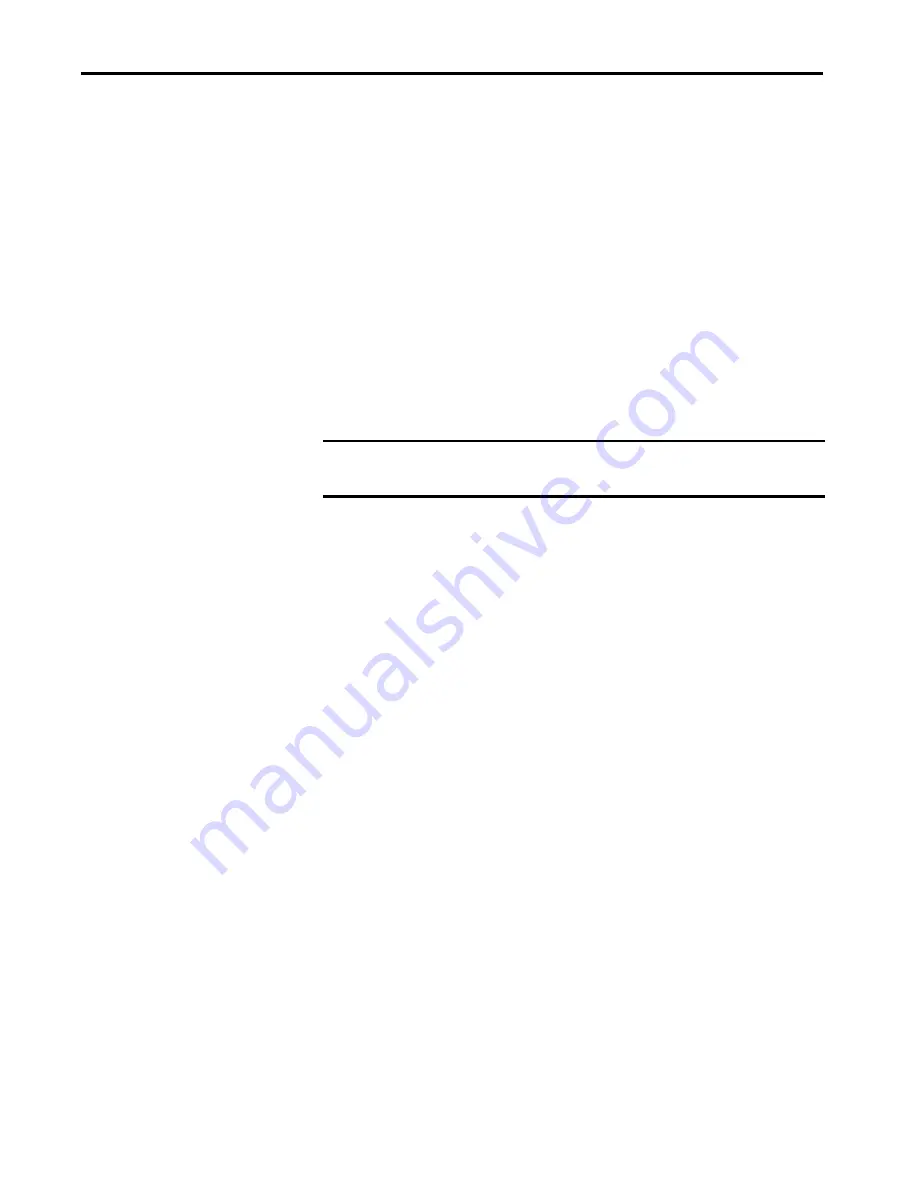
18
Rockwell Automation Publication 1715-RM001A-EN-P - June 2019
Chapter 2
Features of the ControlLogix SIL 2 System
To perform program verification, follow these steps in RSLogix 5000 software or
the Studio 5000 Logix Designer application.
1.
With the programming software closed rename the project.
2.
Start the programming software, upload the controller project, and save it.
3.
Open the compare tool and select both files.
4.
Start the compare operation.
5.
Review the compare output results and verify that everything matches
without error. (Project documentation differences can exist.)
6.
Save the compare results as part of the verification process.
7.
Delete the upload file.
8.
To maintain project documentation, rename the original project file
(change back) to the original project name.
HMI Precautions
You must exercise precautions and implement specific techniques on HMI
devices. These precautions include, but are not limited to the following:
• Limited access and security
• Specifications, testing, and validation
• Restrictions on data and access
• Limits on data and parameters
HMI- related functions consist of two primary activities: reading and writing
data.
Reading Data
Reading data is unrestricted because reading doesn't affect the operation or
behavior of the safety system. However, the number, frequency, and size of the
data being read can affect controller performance. To avoid safety-related
nuisance trips, use good communication practices to limit the impact of
communication processing on the controller. Do not set read rates to the fastest
rate possible.
IMPORTANT
Do not use memory cards to transfer the safety application automatically.
The AutoFlash firmware feature is not supported for SIL 2 safety applications.