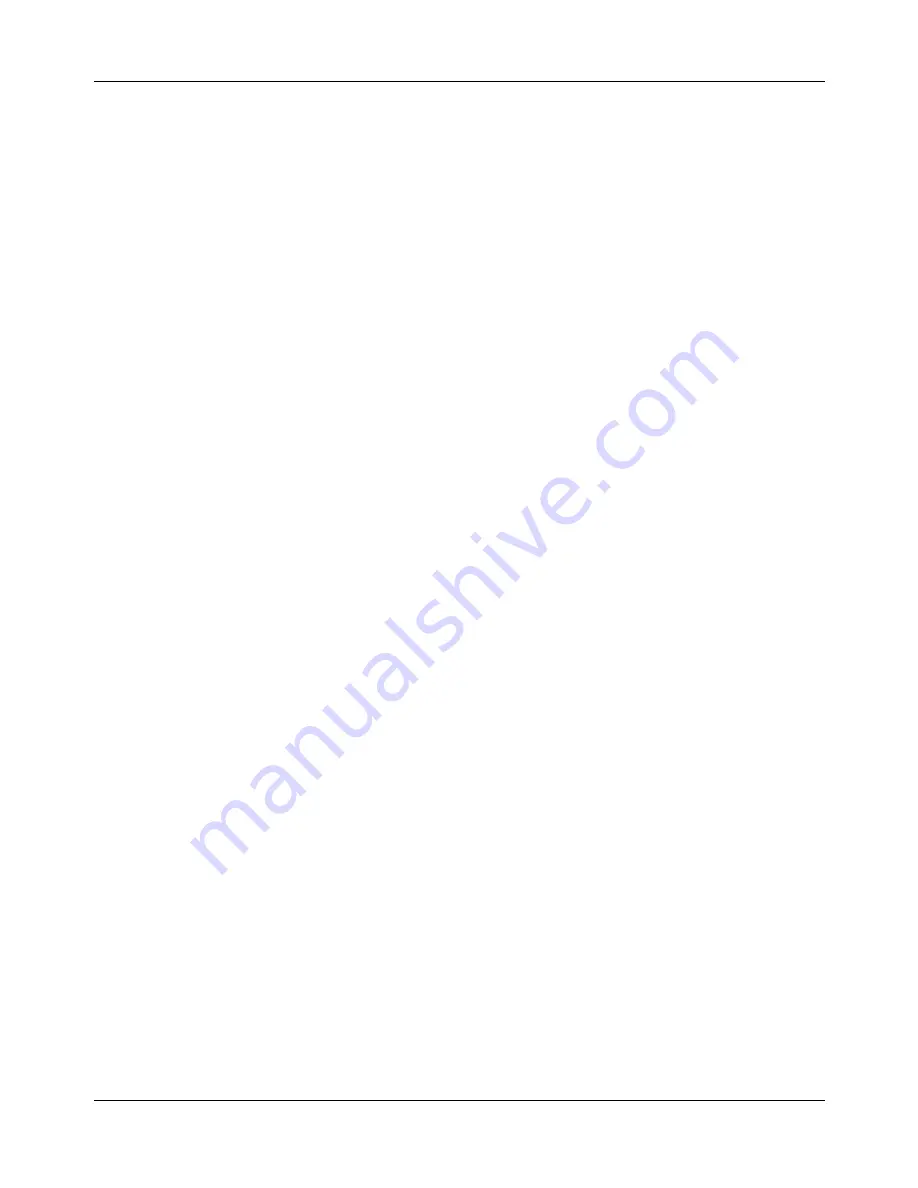
Design Guidelines
Transport System Design
74
MagneMotion
Rockwell Automation Publication MMI-UM007F-EN-P - September 2020
vehicle motion is suspended. Normal operation resumes once the internal propulsion bus rises
back up to +270V DC. If the internal bus voltage rises above +430V DC during operation, the
motor controller reports an overvoltage fault and all inverters within the controller are dis-
abled. Normal operation resumes once the internal propulsion bus falls below +420V DC.
Once the inverters are disabled, any vehicles in motion over the motor are no longer under
active control and as such their motion is undefined.
Wiring QSHT Motors Using QSHT 5700 Inverters
The QSHT inverters are designed to operate at a n458–757V DC. However, voltage
drops in the power distribution system when delivering power to the inverters and voltage
increases during regeneration events cause fluctuations in the voltage that is seen at the
inverter power terminals. The power supplies and wiring for the system must be designed to
minimize these fluctuations. A block diagram of a QSHT system schematic using QSHT 5700
inverters and 2198-Pxxx DC-bus power supplies is provided in
. Any part num-
bers that are shown are for reference only and are subject to change.
The acceptable voltage range for the QSHT inverters is b350V DC and +820V DC,
with a nominal voltage of +458–757V DC. Operation below or above this range can result in
the inverter turning off or the inverter being damaged. The inverter has protections in place to
help prevent damage. The power supply system must be designed so that the voltage limits are
not exceeded during normal operating conditions and provide protection to the power supply
if these limits are exceeded. To supplement any external power management schemes for the
QSHT transport system, a means of internally consuming regenerated power within a QSHT
motor is incorporated as a product feature (see
). Use of the
2198-Pxxx DC-bus power supplies is recommended.
The QSHT inverters are enabled when the internal propulsion bus rises above +350V DC.
Until this voltage is reached, the inverter reports an undervoltage fault and the inverter does
not allow vehicle motion to occur. Once this internal voltage is reached, the motor can support
vehicle motion and operate as intended. If the internal bus voltage drops below +350V DC
during operation, the inverter reports an undervoltage fault and all vehicle motion is sus-
pended. Normal operation resumes once the internal propulsion bus rises back up to +350V
DC. If the internal bus voltage rises above +820V DC during operation, the inverter reports an
overvoltage fault and the inverter is disabled. Normal operation resumes once the internal pro-
pulsion bus falls below +820V DC. Once the inverter is disabled, any vehicles in motion over
the motor are no longer under active control and as such their motion is undefined.
Power Wiring
All power wiring must be constructed such that there is minimal loss between the power sup-
plies and the motor drives (see
). Additionally, the power wiring
must be able to support power regeneration due to the active braking or deceleration of vehi-
cles. The preferred architecture for the power bus when using QSMC controllers is a number
of junction boxes (shown in
) connected in series to form a low-resistance power
bus with a tap to each drive. The preferred architecture for the power bus when using QSHT
inverters is a shared power bus (shown in
) connected to form a low-resistance
power bus with a tap to each drive.