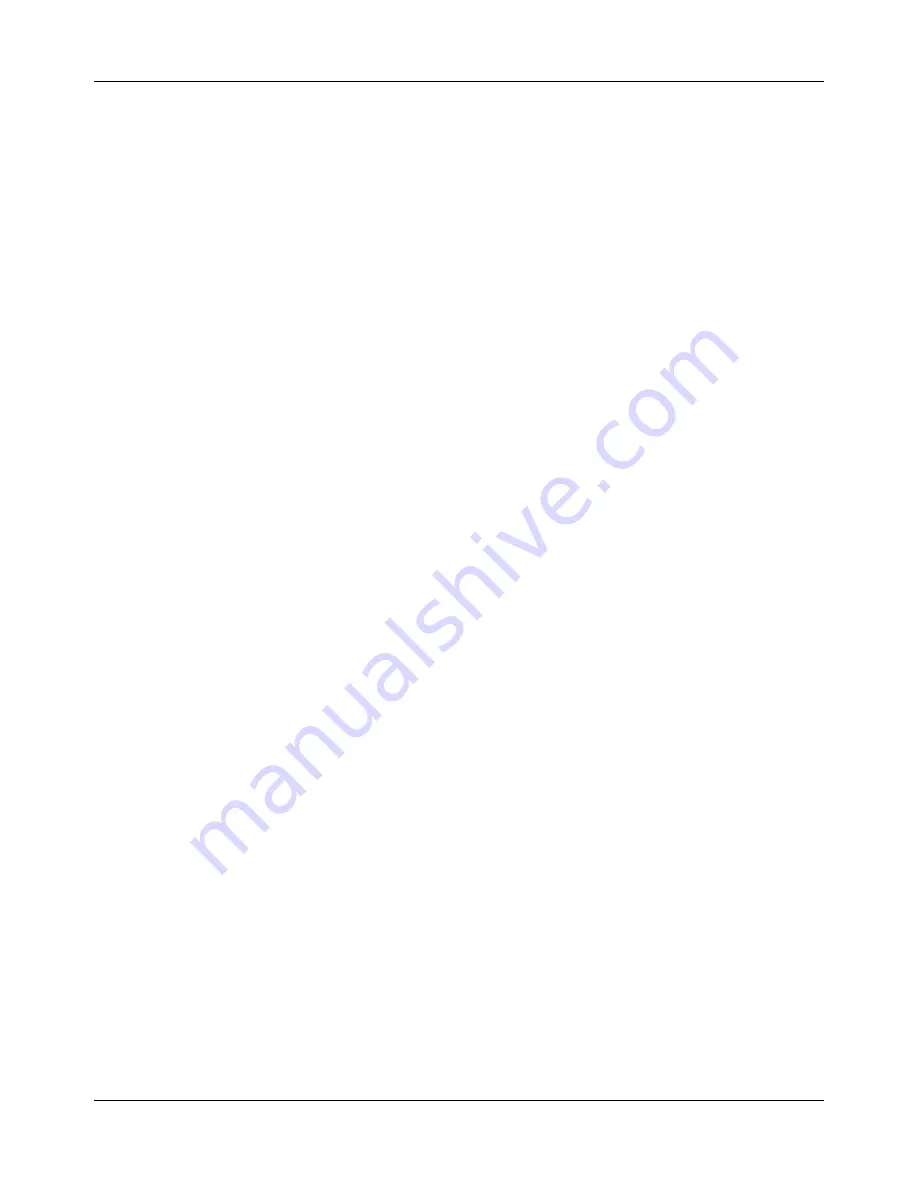
Operation
Theory of Operation
QuickStick HT User Manual
239
Rockwell Automation Publication MMI-UM007F-EN-P - September 2020
Electrical System
Voltage drops in the power distribution system when the motors consume power while mov-
ing vehicles and voltage increases during regeneration events lead to fluctuations in the volt-
age seen at the motor power terminals. Under normal operating conditions, these fluctuations
are minimal and can be ignored. The power supplies and wiring for the system must be
designed to minimize these fluctuations (see
).
Using QSMC Motor Controllers
The QSHT motors are designed to operate at a n300–400V DC. The inverters that
power the individual blocks within the motor are enabled when the internal propulsion bus for
the motor rises above +270V DC, which allows normal motor operation and are shut down if
the voltage falls below +250V DC. The inverters in the motor are also shut down when the
internal propulsion bus rises above +430V DC to help protect internal circuitry and are
enabled when the voltage falls below +420V DC. The logic circuits in the motor are designed
to operate at a n24V DC, but start to function once the logic bus rises above +20V
DC, which allows reporting of all motor warnings and faults.
Using QSHT 5700 Inverters
The QSHT motors are designed to operate at a n458–747V DC. The inverters that
power the individual blocks within the motor are enabled when the internal propulsion bus for
the motor rises above +350V DC, which allows normal motor operation and are shut down if
the voltage falls below +330V DC. The inverters in the motor are also shut down when the
internal propulsion bus rises above +830V DC to help protect internal circuitry and are
enabled when the voltage falls below +820V DC. The logic circuits in the motor are designed
to operate at a n24V DC, but start to function once the logic bus rises above
+21.6V DC, which allows reporting of all motor warnings and faults.
Power Regenerated by a Vehicle
When a vehicle slows to a stop, the mechanical energy of the vehicle is converted to electrical
energy, which is applied to the internal propulsion bus of the motor. This energy must then be
dissipated to avoid raising the voltage of the bus beyond the m
aximum recommended operating
voltage
.
Power is provided to the motor to slow down the vehicle actively so the net effective regener-
ation power is lower than the power required to accelerate the vehicle. The reduction is based
on a number of factors, but a conservative estimate is that the net effective regeneration power
is about 75% of the acceleration power. As the vehicle slows down under constant decelera-
tion, the regeneration power drops linearly with speed.
Power Management Within the Motor
To supplement any external power management schemes that are applied to a QuickStick HT
transport system, several means of internally consuming regenerated power within a QSHT