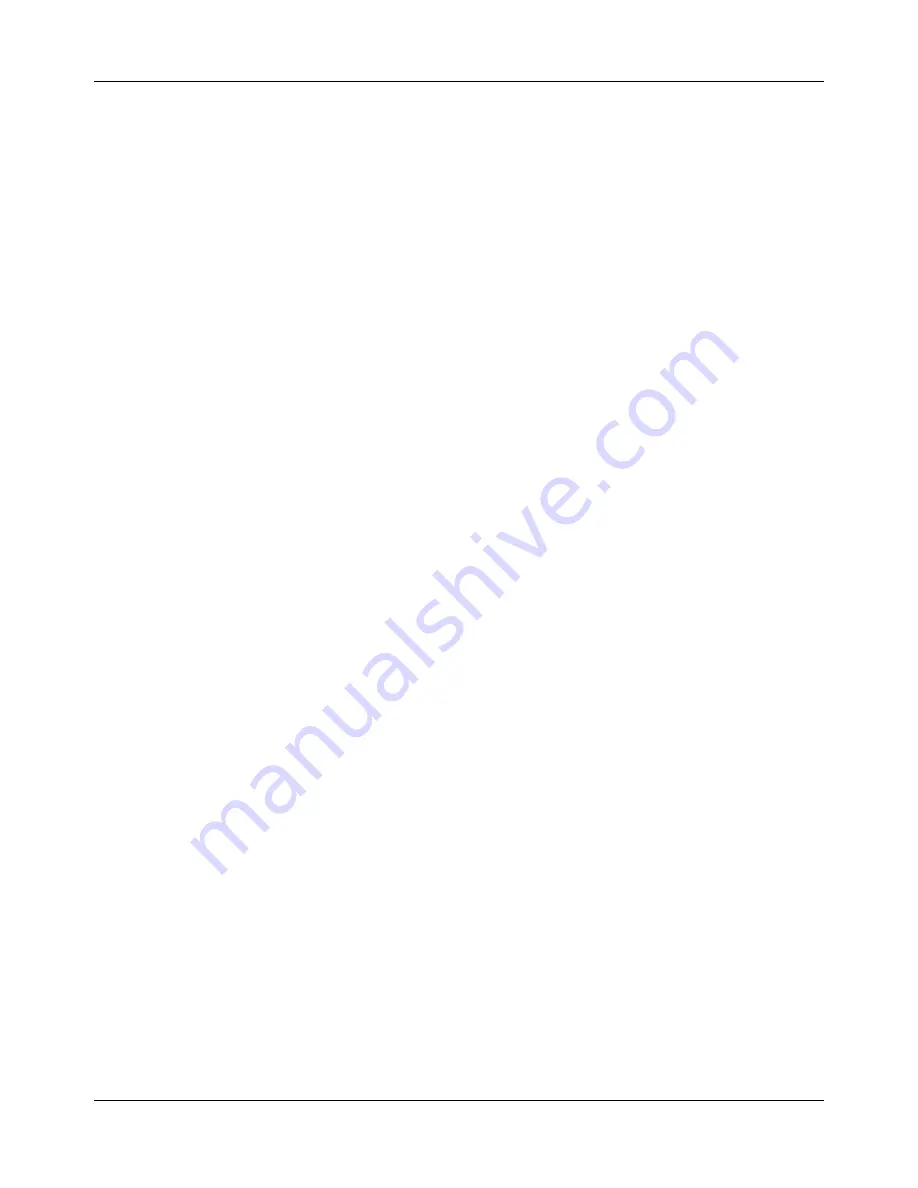
Design Guidelines
Transport System Design
QuickStick HT User Manual
73
Rockwell Automation Publication MMI-UM007F-EN-P - September 2020
Motor Drives
The motor drive for each QuickStick HT motor is located externally to the motor. Each QSHT
motor has one motor drive. When there are two consecutive 1/2 m motors, they can share a
drive. The motor drive is responsible for controlling the thrust that is applied to each vehicle
by the motor and reading the sensors in the motor to determine vehicle position.
Using QSMC Motor Controllers
Each QSMC motor controller can control one 1 m QSHT motor or one 1/2 m double-wide
QSHT motor. Each QSMC-2 motor controller can control two consecutive 1/2 m QSHT
motors on the same path. The QSMC motor controllers communicate with each other and a
node controller via RS-422 serial communication.
Using QuickStick HT 5700 Inverters
Each QSHT 5700 inverter can control one 1 m motor, or one or two consecutive 1/2 m motors
on the same path, or one 1/2 m double-wide motor. The QSHT 5700 inverters communicate
with each other and a node controller via Ethernet communication.
Electrical Wiring
Wiring QSHT Motors Using QSMC Controllers
The QSMC motor controllers are designed to operate at a n300–400V DC. However,
voltage drops in the power distribution system when delivering power to the motor controllers
and voltage increases during regeneration events cause fluctuations in the voltage that is seen
at the motor controller power terminals. The power supplies and wiring for the system must be
designed to minimize these fluctuations. A block diagram of a QSHT system schematic using
QSMC controllers is provided in
. Any part numbers that are shown are for refer-
ence only and are subject to change.
The acceptable voltage range for the QSMC motor controllers is b270V DC and
+430V DC, with a nominal voltage of +300–400V DC. Operation below or above this range
can result in the motor controller turning off or the motor controller being damaged. The
motor controller has protections in place to help prevent damage. The power supply system
must be designed so that the voltage limits are not exceeded during normal operating condi-
tions and provide protection to the power supply if these limits are exceeded. To supplement
any external power management schemes for the QSHT transport system, a means of inter-
nally consuming regenerated power within a QSHT motor is incorporated as a product feature
(see
The QSHT motor controllers are enabled when the internal propulsion bus rises above +270V
DC. Until this voltage is reached, the motor controller reports an undervoltage fault and the
motor controller does not allow vehicle motion to occur. Once this internal voltage is reached,
the motor can support vehicle motion and operate as intended. If the internal bus voltage drops
below +250V DC during operation, the motor controller reports an undervoltage fault and all