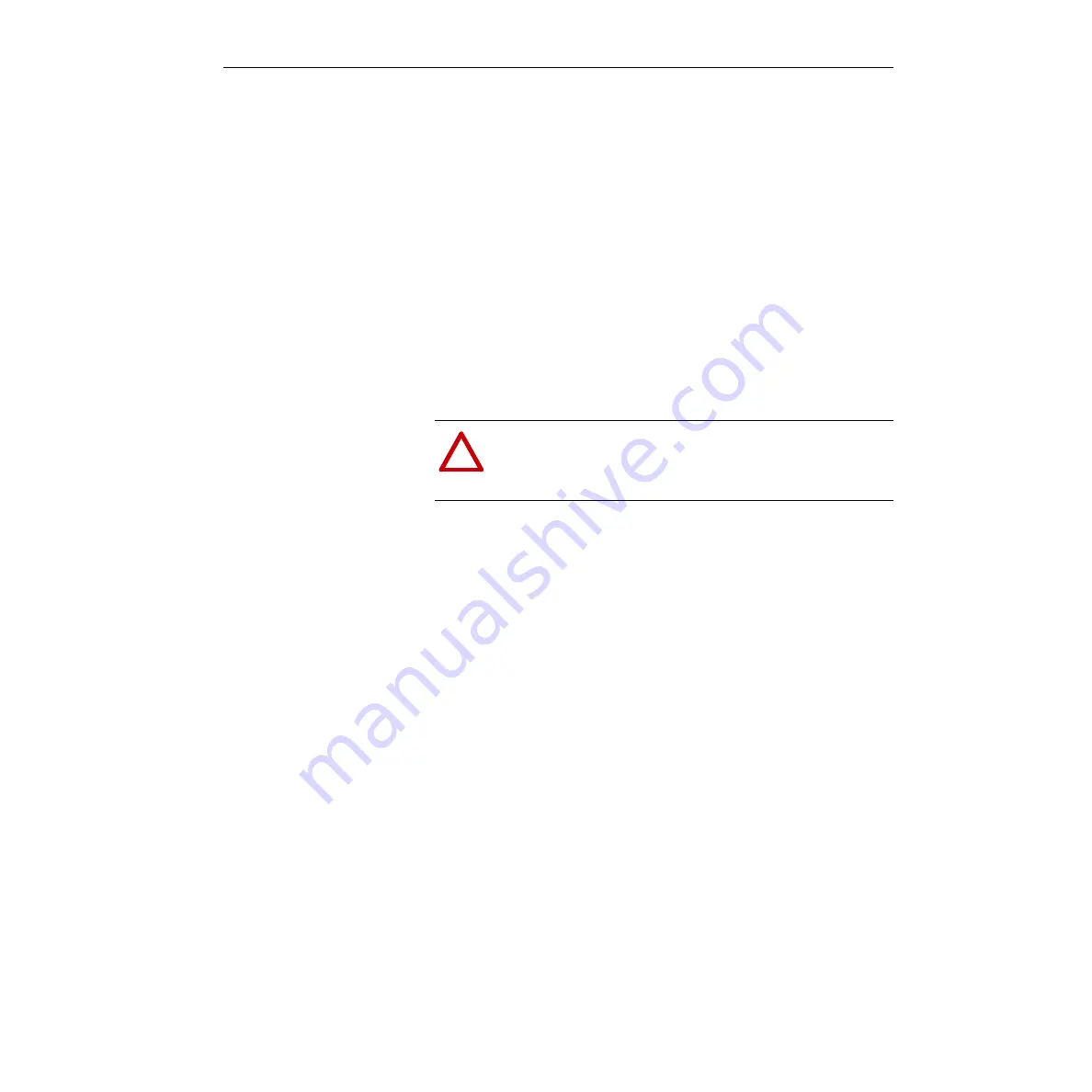
Small DC Motors
3
When mounting through a flexible coupling, verify that there is adequate
clearance between the driven equipment shaft, the coupling interface and
the motor shaft. Lack of clearance may result in binding of the shafting and
premature bearing failure.
Always slide the motor tenon into the mating flange to its full depth before
tightening the mounting bolts. Do not allow the motor to hang by the shaft
extension while assembling it to the driven equipment (i.e. quill input gear
case). This may bend or crease the shaft and damage any seals that are
present.
Only use the proper mounting bolts. These should be 3/8”-16 threads per
inch and sized for length such that engagement into the motor flange does
not exceed 9/16”. For example, a gear case with a 3/8” flange thickness
requires a bolt that is: 3/8” + 9/16” = 15/16” = Maximum Bolt Length
Since 15/16” is not a standard bolt length, a 7/8” bolt or a 1” bolt with a
lockwasher can be used.
Alignment
Shafts should be carefully aligned before tightening any couplings. Inspect
couplings and shaft for paint, dirt or burrs. If necessary, remove with
sandpaper for proper fit. Pulley or coupling should be carefully fitted. Do
not hammer on shaft, pulley or coupling.
Application
Permanent Magnet “PM” motors are not always designed for across the line
starting. This may cause loss of flux resulting in an increase in speed and
possibly instability. Wound field motors can be started across the line with
full applied voltage. However, for frequent starting or reversing, voltage
should be reduced for normal brush and commutator life.
Dynamic or regenerative braking methods should not be used unless
provisions are made to limit the maximum instantaneous current to a value
not greater than the maximum allowable peak amperes shown on the
nameplate. This also applies to plug reversing the PM motor.
Connections
All motors should be installed in accordance with the National Electric
Code and local requirements. Fuses, thermal cutouts and other protective
devices should be the proper size and rating to safely carry the load and to
interrupt the circuit on overloads.
!
ATTENTION: To guard against motor damage such as
premature failure and/or a loose assembly, use only mounting
bolts that are the correct length. A bolt that is too long may cause
damage to the motor.