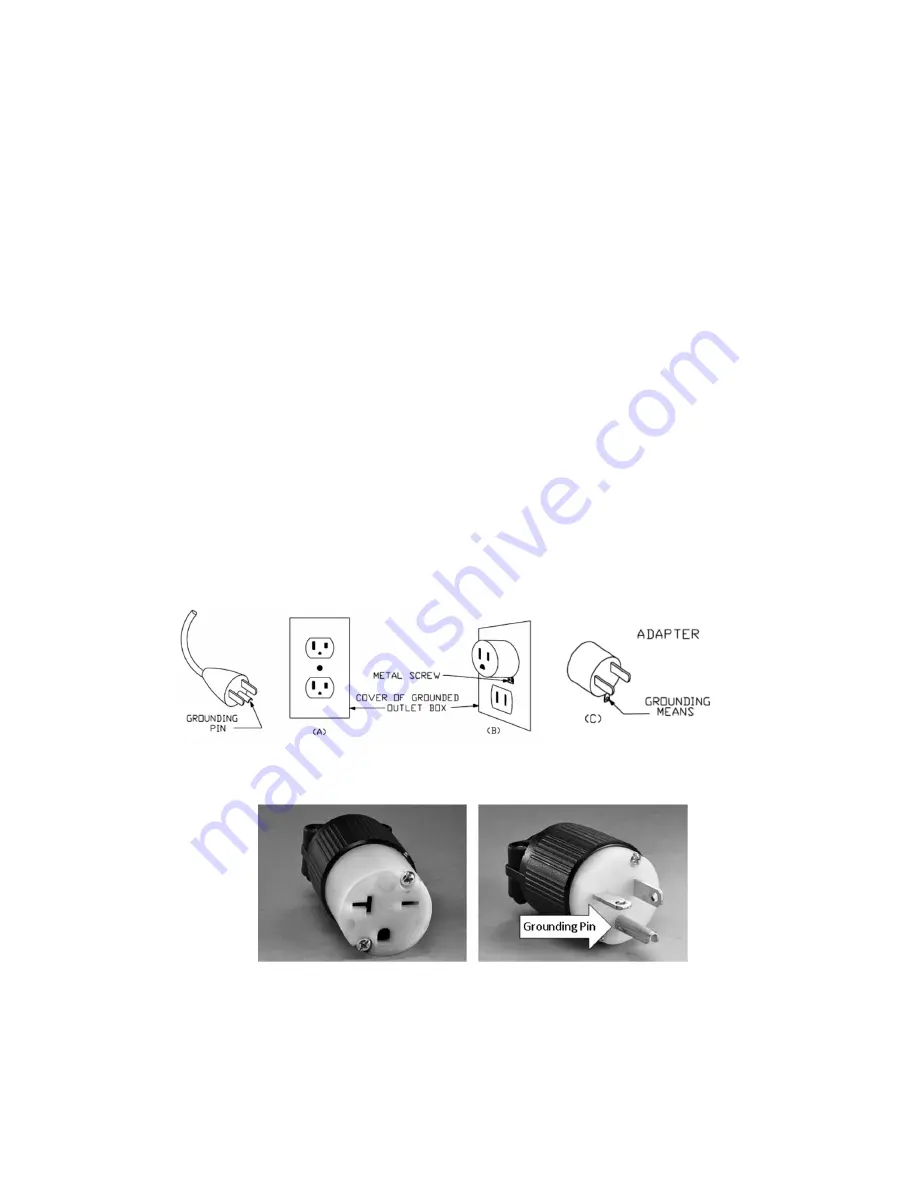
3
41.
GROUNDING INSTRUCTIONS:
In the event of a malfunction or breakdown, grounding provides a
path of least resistance for electric current to reduce the risk of electric shock. You lathe is
equipped with an electric cord having an equipment grounding conductor and a grounding plug.
The plug must be plugged into a matching outlet that is properly installed and grounded in
accordance with all local codes and ordinances.
Do not modify the plug provided – if it will not fit the outlet, have the proper outlet installed by a
qualified electrician. Improper connection of the equipment‐grounding conductor can result in a
risk of electric shock. The conductor with insulation having an outer surface that is green with or
without yellow stripes is the equipment‐grounding conductor. If repair or replacement of the
electric cord or plug is necessary, do not connect the equipment‐grounding conductor to a live
terminal. Check with a qualified electrician or service personnel if the grounding instructions are
not completely understood, or if in doubt as to whether the tool is properly grounded. Use only 3‐
wire extension cords that have 3‐prong grounding plugs and 3‐pole receptacles that accept the
tool’s plug. Repair or replace damaged or worn cord immediately.
Lathes wired to run on 110‐120 volt circuits are intended for use on a circuit that has an outlet
(NEMA 5‐15) that looks like the one illustrated in Sketch A in the figure below. The tool has a
grounding plug that looks like the plug also illustrated in the figure. A temporary adapter, which
looks like the adapter illustrated in Sketches B and C, may be used to connect this plug to a 2‐pole
receptacle as shown in Sketch B if a properly grounded outlet is not available. The temporary
adapter should be used only until a properly grounded outlet can be installed by a qualified
electrician. The green‐colored rigid ear, lug, and the like, extending from the adapter must be
connected to a permanent ground such as a properly grounded outlet box.
Lathes wired for operation on a 220‐240 volt circuit are intended for use on a circuit that has an
grounded outlet and plug that looks like those illustrated below (NEMA 6‐20).
*** SAVE THESE INSTRUCTIONS ***