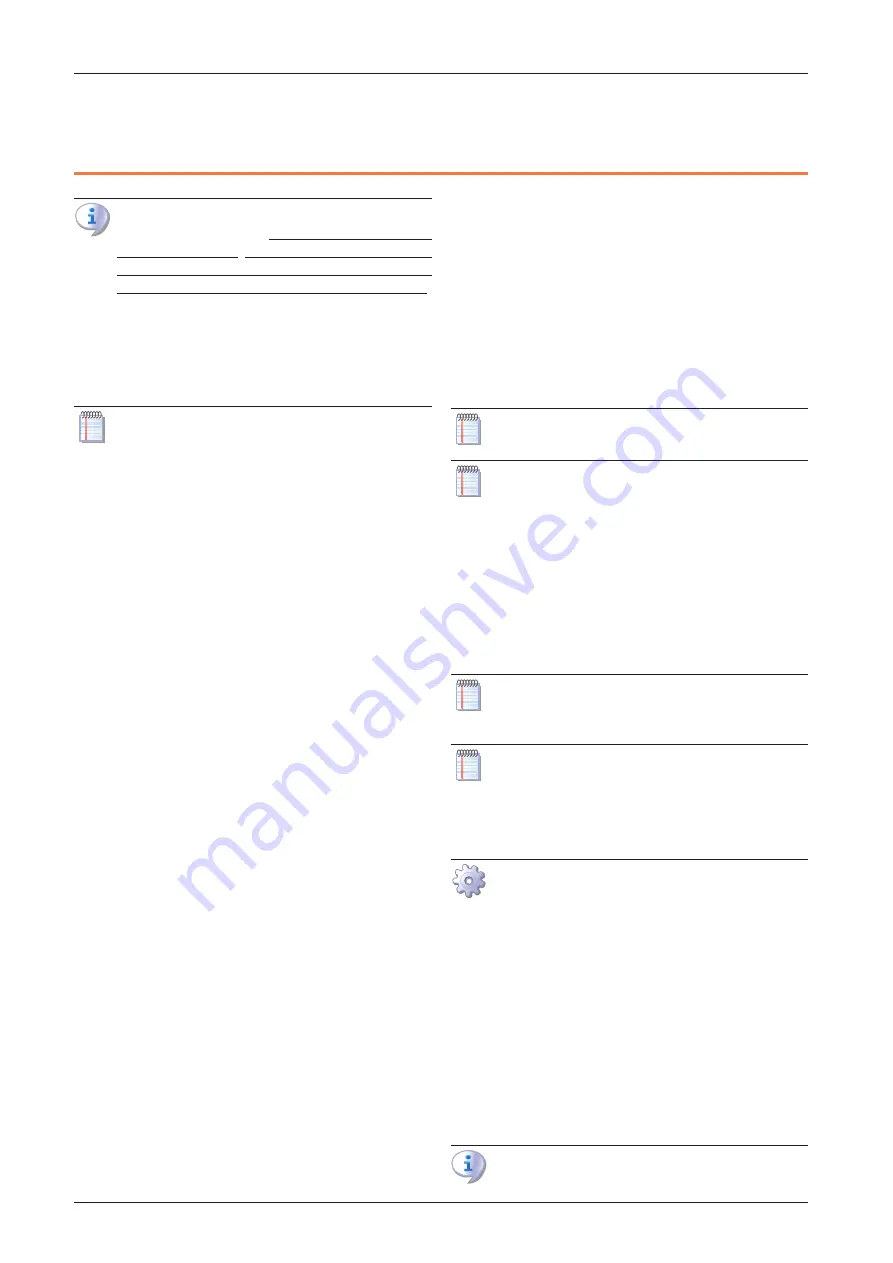
First start-up
Installation, use and maintenance manual – Supercromo
17
5
reversal of the polarity of the power supply.
5
FIRST START-UP
First start-up entails checking/setting up the com-
bustion parameters and may exclusively be carried
out by a Robur TAC. NEITHER the user NOR the in-
stallation technician is authorised to perform such
operations, under penalty of voiding the warranty.
The installer is obliged to carry out preliminary
checks described in Paragraph 5.1
5.1
PRELIMINARY CHECKS
Paragraph dedicated to the installer.
5.1.1
Preliminary checks for first start-up
Upon completing installation, before contacting the TAC
the installer must check:
▶
Electrical and gas systems suitable for the required ca-
pacities and equipped with all safety and control de-
vices required by the regulations in force.
▶
Absence of leaks in the gas system.
▶
Type of gas for which the appliance is designed (natu-
ral gas, LPG or other gas).
▶
Supply gas pressure complying with the values of
Table 3.1
p. 11, with max tolerance ±15%.
▶
Correct operation of the flue exhaust duct.
▶
Combustion air intake and flue gas exhaust correctly
carried out according to the regulations in force.
▶
Power supply mains complying with the appliance's
rating plate data.
▶
Appliance correctly installed, according to the manu-
facturer's provisions.
▶
System installed in a workmanlike manner, according
to national and local regulations.
5.1.2
Abnormal or hazardous installation
situations
Should any abnormal or hazardous installation situations
be found, the TAC shall not perform first start-up and the
appliance shall not be commissioned.
These situations may be:
▶
Failed compliance with minimum clearances.
▶
Insufficient distance from combustible materials.
▶
Conditions that do not warrant access and mainte-
nance in safety.
▶
Appliance defects or faults caused during transport or
installation.
▶
Gas smell.
▶
Non-compliant mains gas pressure.
▶
Non-compliant flue gas exhaust.
▶
All situations that may involve operation abnormali-
ties or are potentially hazardous.
5.1.3
Non-compliant system and corrective
actions
Should the TAC find any non conformities, the user/install-
er is bound to perform any corrective procedures required
by the TAC.
After performing the remedial actions (the installer's re-
sponsibility), if the TAC deems that safety and conformity
conditions are in place, first start-up may be effected.
5.2
CHECKING BURNER GAS PRESSURE
Paragraph reserved exclusively to TACs.
The gas supply circuit is equipped with a gas so-
lenoid valve with double safety shutter and pres-
sure regulator to control the gas flow. All models
are factory-set to operate with natural gas and can
be converted to LPG (see Paragraph 5.3
Each gas-fired convector is calibrated during fac-
tory testing for operation with natural gas. After
installation, check that the gas pressure at the
burner complies with indications in Paragraph
5.3.1
All adjustments must be made with the appliance
switched on and after removing the casing.
After completion of the gas pressure check at
the burner, the valve adjustment screws must be
sealed.
5.2.1
Natural gas supply
Figure 5.1
1. Remove the casing from the frame and disconnect the
casing grounding cable.
2. Connect a pressure gauge to the pressure intake A, af-
ter removing its sealing screw.
3. Switch on the appliance (Paragraph 6.3.1 p. 20).
4. Turn the thermostat to the highest heat demand.
5. Adjust the gas pressure at the burner to the required
value (Table 5.1
p. 18) by means of the pressure
regulator B. By turning clockwise the pressure increas-
es, counterclockwise it decreases. Use a hex key for
adjustment.
6. When the adjustment is complete, switch off the
appliance.
After the adjustment, stop and start the appliance
and check that burner pressure has stabilised. If
Summary of Contents for Supercromo
Page 27: ......