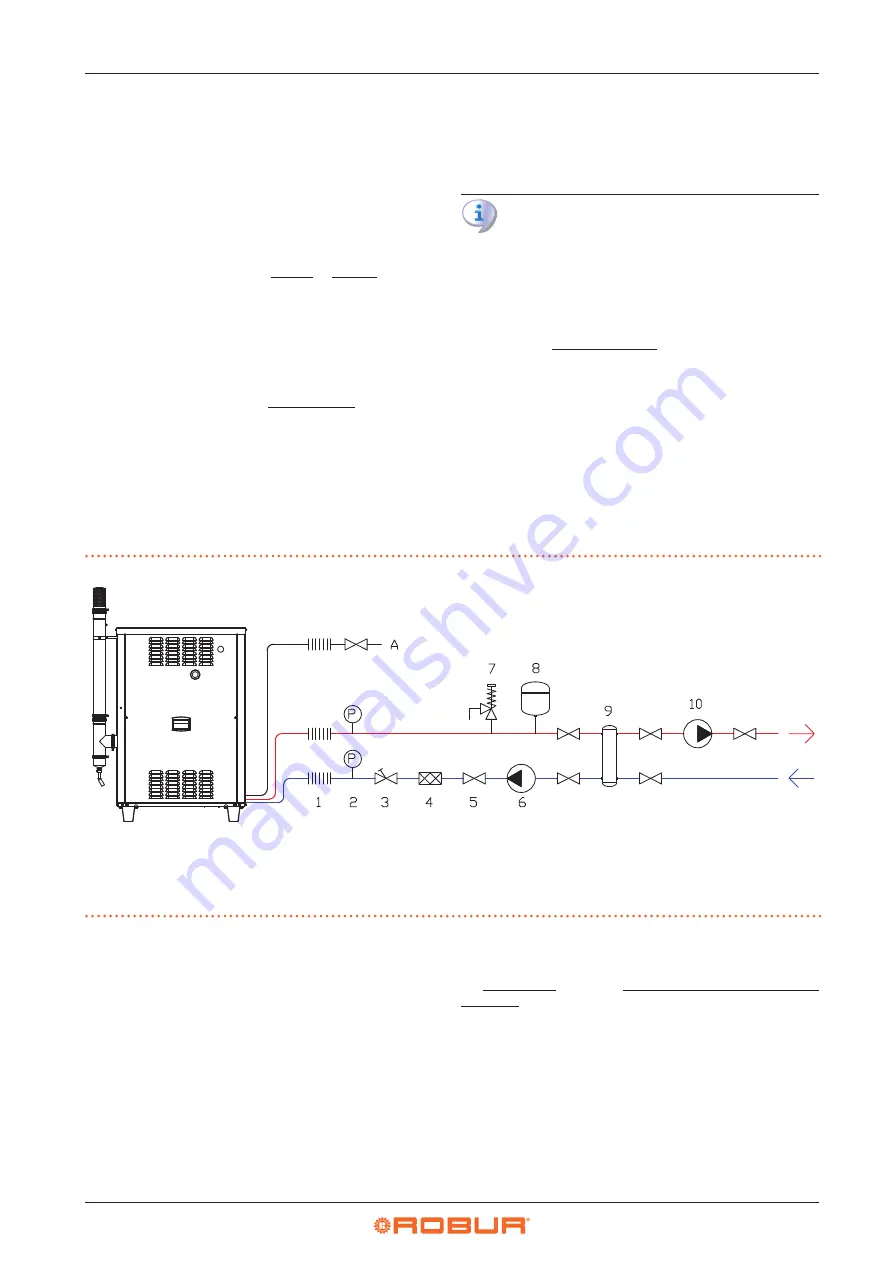
Heating engineer
20
3
3.2
HYDRAULIC SYSTEM
3.2.1
Primary and secondary circuit
▶
In many cases it is advisable to divide the hydraulic system
into two parts, primary and secondary circuit, uncoupled by
a hydraulic separator, or possibly by a tank that also acts as
inertial tank/buffer.
3.2.2
Constant ot variable water flow
The GAHP A unit may work with costant or variable water flow,
regardless of the ON/OFF or modulating operative mode.
System and components must be designed and installed
consistently.
3.2.3
Minimum water content
High thermal inertia is conducive to efficient appliance opera-
tion. Very short ON/OFF cycles are to be avoided.
▶
If necessary, provide for an inertial volume, to be suitably
sized (see design manual).
3.3
HYDRAULIC CONNECTIONS
3.3.1
Hydraulic connections
on the right, at the bottom, connection plate (Figure 1.1
p. 7).
▶
A (= out) 1 1/4" F - WATER OUTLET (m = outlet to the system)
▶
B (= in) 1 1/4" F - WATER INLET (r = return from the system)
3.3.2
Hydraulic pipes, materials and features
▶
Use pipes for heating/cooling systems, protected from
weathering and freezing, insulated for thermal dispersion.
Pipe cleaning
Before connecting the appliance,accurately wash the
water and gas piping and any other system component,
removing any residue.
3.3.3
Minimum components of primary plumbing
circuit
Always provide, near the appliance:
▶
on water piping, both output and input
2 antivibration joints on water fittings
2 pressure gauges
2 isolation ball valves
▶
on the inlet water piping
1 separator filter
1 flow regulation valve, if the circulation pump is with
constant flow
1 water circulation pump, towards the appliance
▶
on the output water piping
1 safety valve (3 bar)
1 expansion tank of the individual unit
Figure 3.1
Hydraulic plan
The flow regulator valve must only be used when
the primary circuit circulation pump is constant
flow type
A
Gas connection
1
Anti-vibration connection
2
Pressure gauge
3
Flow regulator valve
4
Water filter
5
Shut-off valves
6
Water pump (primary circuit)
7
Safety valve (3 bar)
8
Expansion tank
9
Hydraulic separator / inertial tank with 4 fittings
10 Water pump (secondary circuit)
3.4
WATER PUMP
The circulation pump (flow and head) must be selected and
installed based on pressure drops of plumbing/primary circuit
( comp exchange ter appliance).
For the appliance pressure drops refer to Table 1.1
Design Manual.
3.4.1
(1) Constant flow circulation pump
The primary circulation pump must be obligatorily controlled
by the appliance's electronic board (S61) (see Paragraph
1.5
p. 13).
3.4.2
(2) Variable flow circulation pump
For variable flow operation, use of a Wilo Stratos Para pump is
obligatory, supplied as accessory on demand, to be connected
to the Mod10 electronic board (see Paragraph 1.5
p. 13). Any
other type of pump will give constant flow.
Refer to the Design Manual for the features of the Wilo Stratos
Para pump.
3.5
ANTIFREEZE FUNCTION
3.5.1
Active antifreeze self-protection
The appliance is equipped with an active antifreeze self-pro-
tection system to prevent freezing. The antifreeze function
Summary of Contents for GAHP A indoor
Page 39: ......