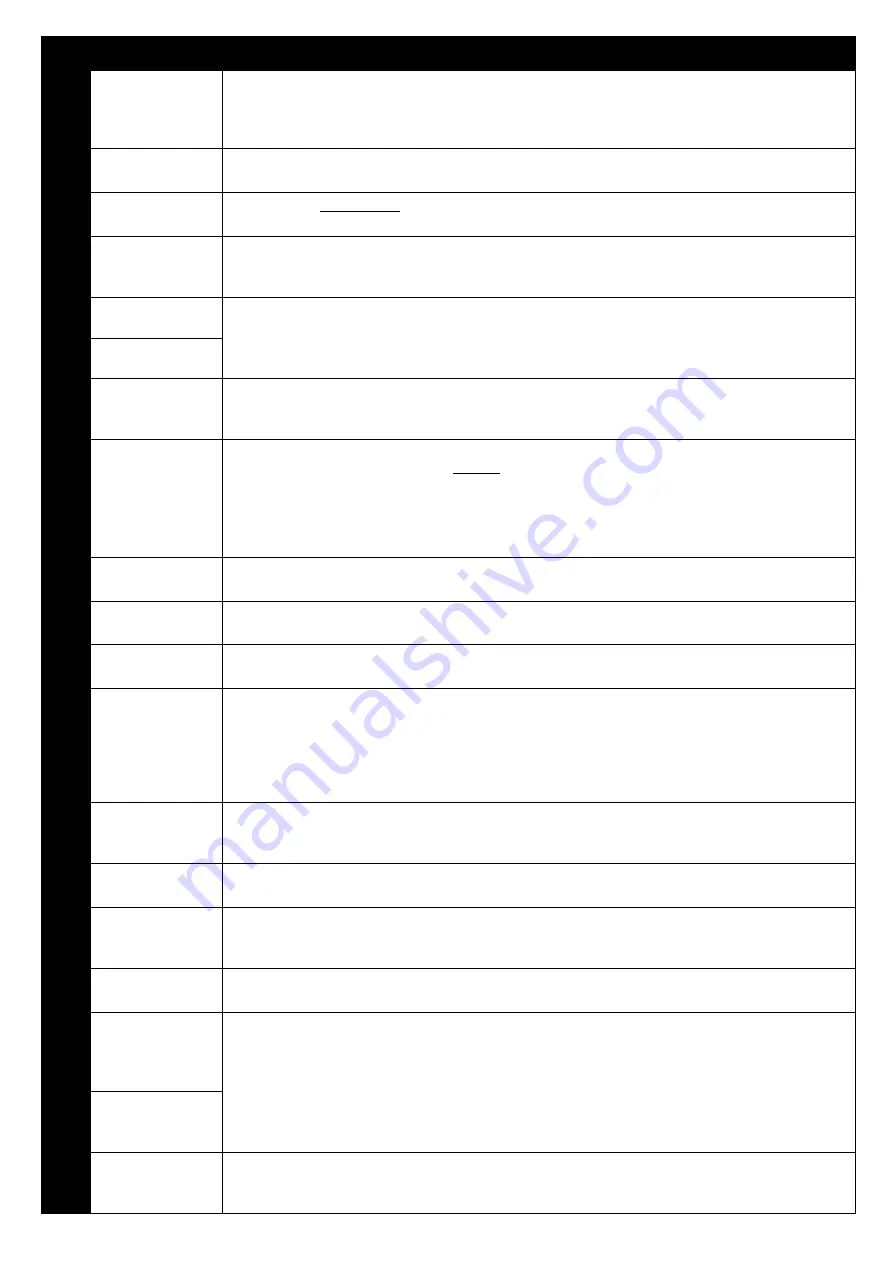
3
SECTION
No
TITLE
ASSEMBLY SYNOPSIS: IMPORTANT INFORMATION / CONSIDERATIONS
PARTS LIST
Identify and separate all like for like components prior to assembly. The ‘parts list’ also separates parts
into the various sections 1 - 12 shown below. Parts can also be identified by their profile pictures and
stated lengths etc..
B
BASE
Base dimensions and recommendations. Ensure that your base is level as this will make assembly of
the building, especially the glazing of the roof much more straight forward.
P
PREPARATION
Tools required. IMPORTANT: Use WD40 or similar in the glazing bar channels and insert the black glaz-
ing rubber prior to frame assembly.
1
SIDES
Take the side glazing bars ‘D609’ with the rubber inserted and the diagonal braces ‘D604’, use 10mm
bolts to join them to the gutter and 15mm bolts to the cills (note how the head of the bolt slides into each
glazing bar during construction).
2
FRONT
Again ensuring that the gable framework is rubbered-up follow the diagrams to assemble each end of
the building. Make sure that you have inserted the extra bolts utilised in sections 4, 5 and 10. On the
roof and side corner bars not every rubber channel will require rubber unless it is to be utilised in a parti-
tion (see separate manual and section P).
3
REAR
4
JOINING THE
FOUR SIDES
Take the two sides (1) and both gables (2 & 3) and join them together on your base. It is a good idea to
tie some ladders to the sides to support them if you do not have anyone to hold them for you.
5
ROOF
Attach the ridge and then the rubbered-up roof bars ensuring that they are fully butted up to the ridge
and down onto the gutter. If you have cresting then it is a good idea to fit it before glazing, see section
(15). Some tubular braces are supplied to add extra strength, they should be fitted with crop head bolts.
Purlings should also be attached using crop headed bolts along the mid-line of each roof side to add
extra strength ‘e.g.D113’ (please note that a 30mm segment will need to be notched out of the protrud-
ing angle where a purling meets an A-frame so that the purling can tuck in-between the roof bar and the
A-frame).
6a
VENT
Once the vent is glazed add silicone to the vent sides and top. Stand the vent/s on their hinge (vent top)
and then leave the silicone to set.
6b
VENT SLAM
The slam bar ‘D079’ can be moved up and down between the roof glazing bars so that it can be butted
down onto the pane of glass beneath, the autovent will be attached to it later on (9).
7
DOOR/S
Construct the door using the diagrams and then leave to one side ready for attachment in section (10).
8
GLAZING
Layout the bar cappings and covers around the building like a sundial checking that all is present and
correct. You can also place the roof cappings in the gutters so they are closer to hand. The glass in the
ends has to bevel on the black separator strip, this bevelling action allows the glass to tuck underneath
the roof corner canopy. Use the capping and the self tapping screws to then hold the glass in place. The
covers then enclose the screw heads giving a neat finish. It is a good idea to glaze two roof sections first
to ensure the building is square followed by two side sections to ensure the building isn't leaning,
9
VENT
ATTACHMENT
Take the assembled vent and slide the vent hinge ‘D866’ into the end of the ridge allowing the vent the
pivot open and closed. Vent stops go either side of the vent to stop any lateral movement (so insert
stop / vent / stop). Attachment of the Bayliss XL autovents.
10
DOOR
ATTACHMENT
Use the bolts inserted in section (2) to attach the upper door track. The lower door runner ’D861’ and
ramp threshold ‘D088’ push down and lock together.
11
ANCHORING
DOWN
Now that the greenhouse is finished and the door and vent/s are operating without interference then you
need to anchor the building down using 2” rawl plugs and screws. Use a 7mm masonry bit in a hammer
drill to create the holes.
12
OPTIONAL
LOUVRE
They attach to the building during the glazing process (8) like a piece of glass with a black separator
above and below them.
13
OPTIONAL
SHELVING
14
OPTIONAL
STAGING
15
FINISHING
TOUCHES
Now that the main body of the structure is complete you can add; ridge caps, downpipe fittings, eave
bungs. Images showing cresting and finial attachment, this is often easiest to do after section (5) rather
than using the vent apertures later on (i.e. before glazing).
Robinsons integral cantilever staging and shelving attaches to the inside of the greenhouse frame using
either square head bolts (insert four into each side glazing bar ’D609’ during construction of the sides
(1)) or rectangular ‘crop head’ bolts which can be fitted retrospectively (both sets of bolts accompany the
shelving/staging). This system allows the height of either the staging or the shelf to be set at an operator
specific height. Commonly the staging brackets are set 900mm from the cills though you can alter this to
suit the end user/s. The aluminium shelf / staging slats come in two lengths; (4’):1240mm ‘D2002’ and
(6’):1860mm ’D2003’. These slats can combine to create any length of staging required, i.e. 4’+6’ = 10’
etc...
Summary of Contents for Renown Dwarf
Page 9: ...9 D604 TRANSIT BOLT ON DIAGONALS 15mm D604 15mm D609 10mm D609...
Page 13: ...13 D655 D741L D670 D111 D742R D741L D741L D608 D626 D743 D608 D740 D174 D626 D656 D740...
Page 14: ...14 EQUAL...
Page 17: ...17 D862 D862 D863L 2 2 2 2 2 FLIP VIEW D119 CUT 6mm SILICONE...
Page 19: ...19 D889 GLASS D889 GLASS D1208 GLASS...
Page 24: ...24 D220 D220...
Page 25: ...25 D079 D862...
Page 27: ...27 D085 D865 D086 15 7 N A 7 D150 15 4 N A 4 D865 D845 D733...
Page 28: ...28 D861 1 D088 1 Part No Q D861 D088 D861 D088...
Page 30: ...30 O7mm...
Page 37: ...37...