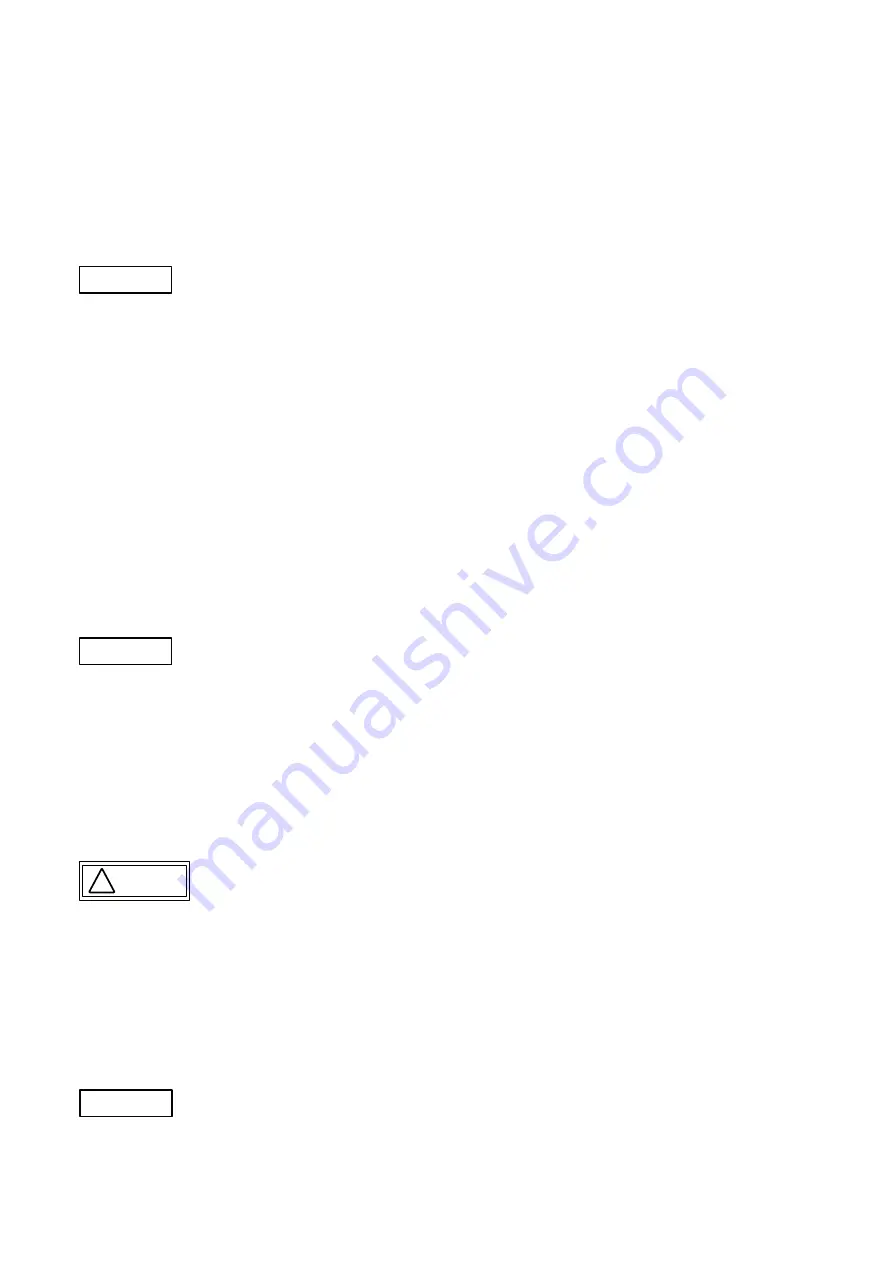
530.24 S.04
2.
Specific maintenance instructions
Under normal circumstances, maintenance jobs may be limited to the sealing elements of the drive shaft and actuator
(zero shut-off) and the threads of the spindle and mitre gear.
2.1 Disassembling and replacing seals
Use the electrical actuator to move the valve sleeve to the
UP
position. (Limit switch
UP
switches off.)
Remove screws/bolts (37) to dismount the rotary drive + cap (5).
Check the thread and feather key groove of spindle (23): Worn?
- The sides of the thread must be smooth – no score marks.
- The unit consisting of the s rotary drive must not show any axial play.
- The spindle must screw easily into the rotary drive.
- Lubricate the spindle (23), internal thread of the rotary drive (15), feather key (24) and key-feather
groove generously.
Mark the position of the drive shaft (3) with a view to actuator (16) and in relation to the feather key (2)
and position of plate (53). (Important during re-assembly.)
Caution
!
Note
•
•
•
•
•
•
•
•
•
•
•
•
Mark the position of spindle (23) with a view to bush 2 (26). (Important during re-assembly.)
Note
•
•
•
Turn drive shaft (3) to move the spindle (23) up and/or down all the way to the mark. The marks on the
shaft (3) and plate (53) must match.
Note
Loosen the cheese head screw in adjusting nut (4) and remove the nut.
Remove the cheese head screws (7).
Remove the plate (52) from housing (16) by screwing in two 2 M10 eye bolts.
After you removed the cheese head screws (56), pull bush (58) out of plate (53).
Replace the seal (54). Consider the proper position when fitting:
The coil spring must point in the direction of the pressure side.
Remove the device from the system and place it on its inlet flange. Remove the cheese head screws (29) and pull
out the outlet part (34) towards the top.
Discard the O rings (28 + 45) and put in new ones.
Loosen the cheese head screw in adjusting nut (41) and remove the nut. Remove the valve sleeve (40). Use two M8 eye bolts to
pull it out of the device .
Loosen screws/bolts (47) and remove ring segment (32). Discard seal elements (43 + 44) and place new ones.
Remove release sleeve (38). Use two M6 eye bolts to pull it out of the device . Discard the O ring (64), compensation ring (62),
guide-ring (61) and seal (63) cpl. w/support ring (60). Use new ones. Clean the grease chamber (48) and fill with new lubricant
(48).
Loosen the cheese head screws (25) in bush 2 (26), and pull out bush 2. Remove and clean the
feather key (24).
Screw out the cheese head screws (20) and pull out bush 1 (22). Remove the spindle (23).
2.2 Checking components, assembly
Clean ALL the components. Find and grease all components mentioned in lubricant table 2.4 before you put them back in.
Grease ALL bolts before you put them back in. Consult table 2.5 for tightening torques MA.
Insert spindle (23) into rotary drive (15). Screw down bush 1 (22) onto rotary drive. Place feather key (24) into the groove
on spindle (23). Place bush 2 (26) on top. Use the cheese head screws (25) and lock washers (27) to tighten everything.