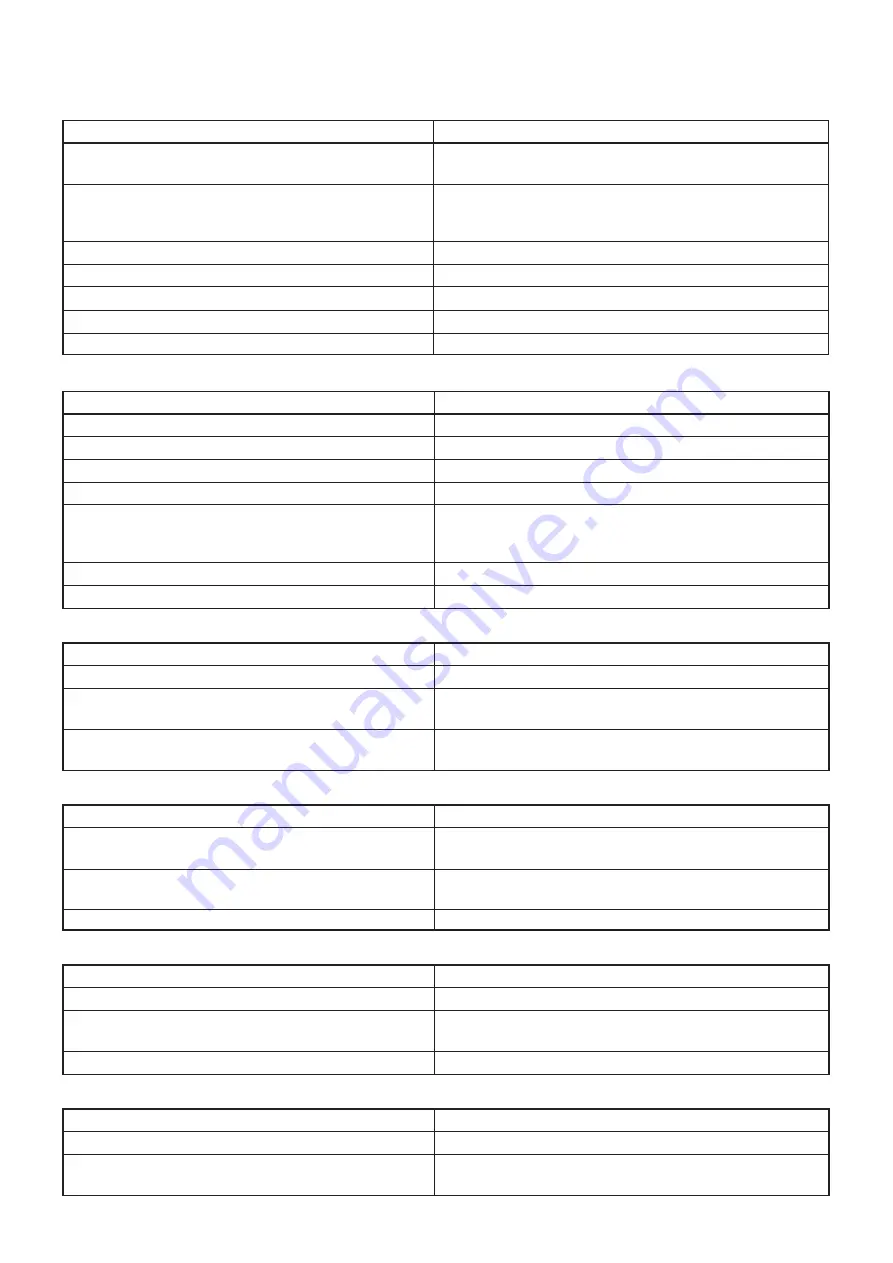
18
Possible Causes:
Grip Range of Rivet Nut is too long
Low Air Pressure
Insufficient Hydraulic Oil leads to Stroke decreased
Air bubbles in Hydraulic Oil
Oil Cylinder (15) leaks
Improper assembly of Valve Assembly (43AY)
Worn O-Rings in Valve Assembly (43AY)
Solutions:
Check suitable Grip Range of Rivet Nut to match work
piece’s thickness. It is nothing to do with Stroke of Tool
Check Compressed Air Supply System, adjust Air Pressure to in
specification, check Air Cylinder (30) leak and replace it if necessary,
clean Air Cylinder (30) inside, clean or replace O-Rings (53, 58, 60)
Refill Hydraulic Oil through Oil Refill Hole, see 11.5 solutions
Bleed Oil from Air Cylinder (30), and refill New Hydraulic Oil
See below 12.9 solutions
Reassemble Valve Assembly (43AY)
Replace all O-Rings (42, 44, 29, 47, 50)
12.7 MALFUNCTION: No operation after triggering (Stroke lost), or more than one operation of Trigger to
fasten Rivet Nut (Stroke decreased)
12.9 MALFUNCTION: Oil Cylinder (15) leaks Hydraulic Oil
Possible Causes:
Oil Cylinder (15) damaged
Improper assembly of O-Rings (13, 19, 27, 29) and Back-Up
Rings (14, 20, 28) in front & rear ends of Oil Cylinder (15)
Worn O-Rings (13, 19, 27, 29) and Back-Up Rings (14, 20,
28) in front & rear ends of Oil Cylinder (15)
Solutions:
Replace a new Oil Cylinder (15)
Reassemble O-Rings (13, 19, 27, 29) and Back-Up Rings
(14, 20, 28) in front & rear ends of Oil Cylinder (15)
Replace new O-Rings (13, 19, 27, 29) and Back-Up Rings
(14, 20, 28) in front & rear ends of Oil Cylinder (15)
12.11 MALFUNCTION: Valve Assembly (43AY) and Noise Silencer (33) leak Air
Possible Causes:
Improper assembly of Valve Assembly (43AY)
Worn O-Rings (42, 44, 29, 47, 50) in Valve Assembly (43AY)
Weak Springs (45, 49) in Valve Assembly (43AY)
Solutions:
Reassemble Valve Assembly (43AY)
Replace new O-Rings (42, 44, 29, 47, 50) in Valve
Assembly (43AY)
Replace new Springs (45, 49) In Valve Assembly (43AY)
12.12 MALFUNCTION: Air Inlet and Air Inlet Fitting leak Air
Possible Causes:
Wrong thread size of Air Inlet Fitting
Air Inlet thread damaged
Solutions:
Change correct thread size of Air Inlet Fitting
Tap thread and wrap Tape Seal around Air Inlet
Fitting’s male thread
12.10 MALFUNCTION: Air Cylinder (30) and Noise Silencer (33) leak Hydraulic Oil
Possible Causes:
Improper assembly of O-Rings (27, 29) and Back-Up Ring
(28) in lower end of Oil Cylinder (15)
Worn O-Rings (27, 29) and Back-Up Ring (28) in lower
end of Oil Cylinder (15)
Worn Lock Nut O-Ring (32A)
Solutions:
Reassemble O-Rings (27, 29) and Back-Up Ring (28) in
lower end of Oil Cylinder (15)
Replace new O-Rings (27, 29) and Back-Up Ring (28) in
lower end of Oil Cylinder (15)
Replace New Lock Nut O-Ring (32A)
12.8 MALFUNCTION: Slow operation or no operation of Air Piston Assembly (55AY) in Air Cylinder (30)
Possible Causes:
Improper assembly of Valve Assembly (43AY)
Worn O-Rings in Valve Assembly (43AY)
Improper assembly of Air Piston Assembly (55AY)
Worn Air Piston Ring (53) and Buffer Ring (52)
Low Air Pressure
Noise Silencer (33) blocks air exhaust
Weak or broken Return Springs (21 & 22)
Solutions:
Reassemble Valve Assembly (43AY)
Replace all O-Rings (42, 44, 29, 47, 50)
Reassemble Air Piston Assembly (55AY)
Replace Air Piston Ring (53) and Buffer Ring (52)
Check Compressed Air Supply System, adjust Air Pressure to in
specification, check Air Cylinder (30) leak and replace it if necessary,
clean Air Cylinder (30) inside, clean or replace O-Rings (53, 58, 60)
Clean or replace a new Noise Silencer (33)
Replace new Return Springs (21 & 22)
Summary of Contents for RNT 120
Page 1: ......
Page 6: ...5 7 DIMENSIONS 39 0 UNIT mm 240 3 303 4 91 0 121 4 115 2...