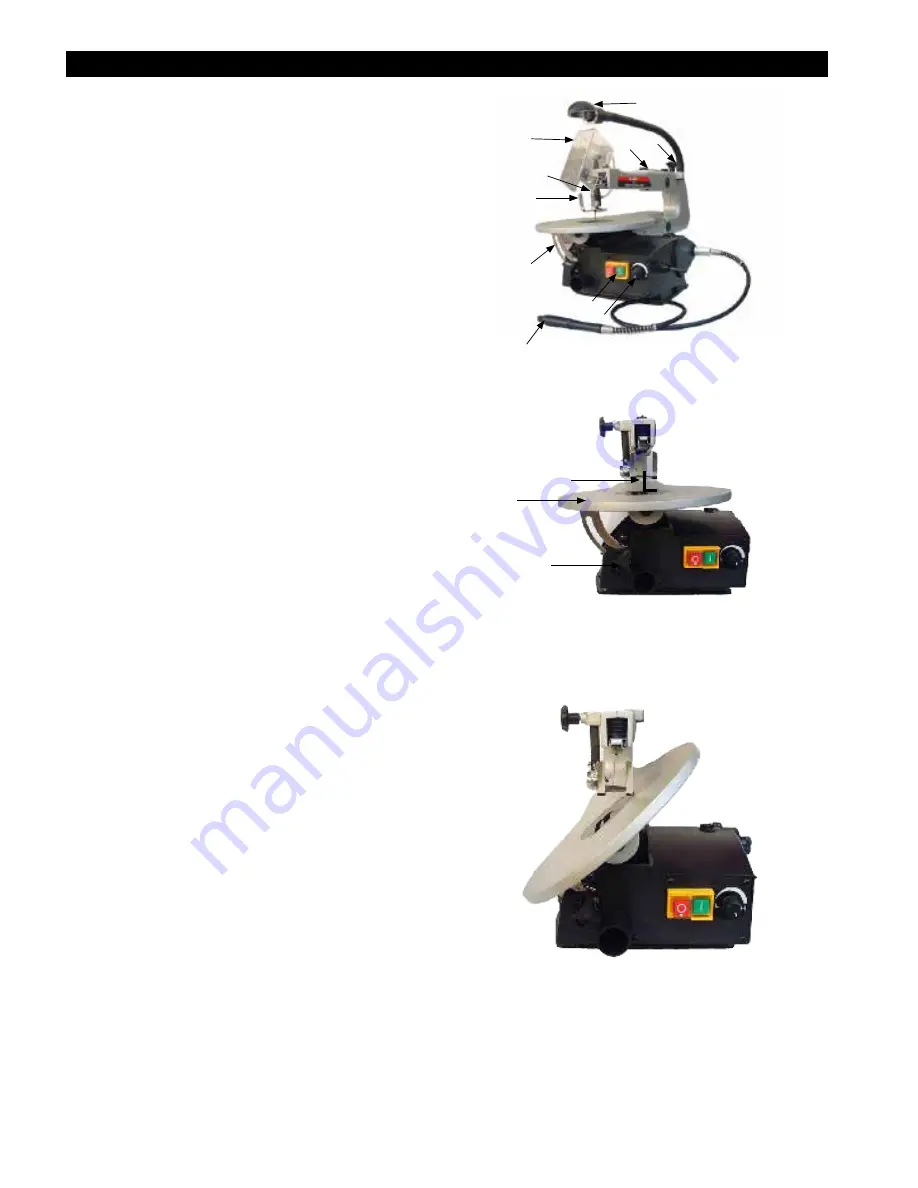
Fig. 01
Fig. 02
6
Assembly
SCROLL SAW DESIGN FEATURES
1. Clamping screw: for removing the saw blade.
2. Blade guard: protects your hands from injury.
3. Work piece holder
4. Shavings blower: keeps the work piece area free
from dust.
5. Variable speed switch
6. On/Off power switch
7. Angle scale: Scale shows the tilting angle of table.
8. Adjustable light
9. Flexible shaft with drill chuck
10. Setting gauge for saw blades without pin
INSTALLATION
Setting the saw bench
Setting the angle scale
• Release the star button (1) and bring the saw bench
(2) to a right angle (3) in relation to the saw blade.
• Use a 90° angle to measure the right angle between
the blade and the bench. The saw blade should be
90° to the angle.
• Close the star button again when the distance be
-
tween the blade and the 90° angle is at a minimum.
The bench should then be at 90° to the saw blade.
• Release the lock screw and bring the indicator to
the zero position. Fasten the screw. Please note: the
angle scale is a useful piece of supplementary equip-
ment, but should not be used for precision work. Use
scrap wood for saw tests, adjust the bench if neces-
sary. Note: The table should not be on the motor
block, this can cause
undesirable noise. Horizontal saw bench and diagonal
cuts
• The saw bench can be positioned into a 45 degree
diagonal position or be left in the horizontal position.
• You can read off the approximate degree of angle by
using the angle scale located under the work bench.
For more exact adjustment, use scrap wood for some
saw tests; adjust the bench if necessary.
Blade guard assembly
Install the blade guard to the holder as shown in the
diagram.
Secure the screws with a nut and washer.
• Lift the saw onto the frame and base and push
it onto the workbench.
• Familiarize yourself with the saw operating
elements and features.
Fig. 03
1
10
2
8
3
4
5
6
7
9
1
2
3