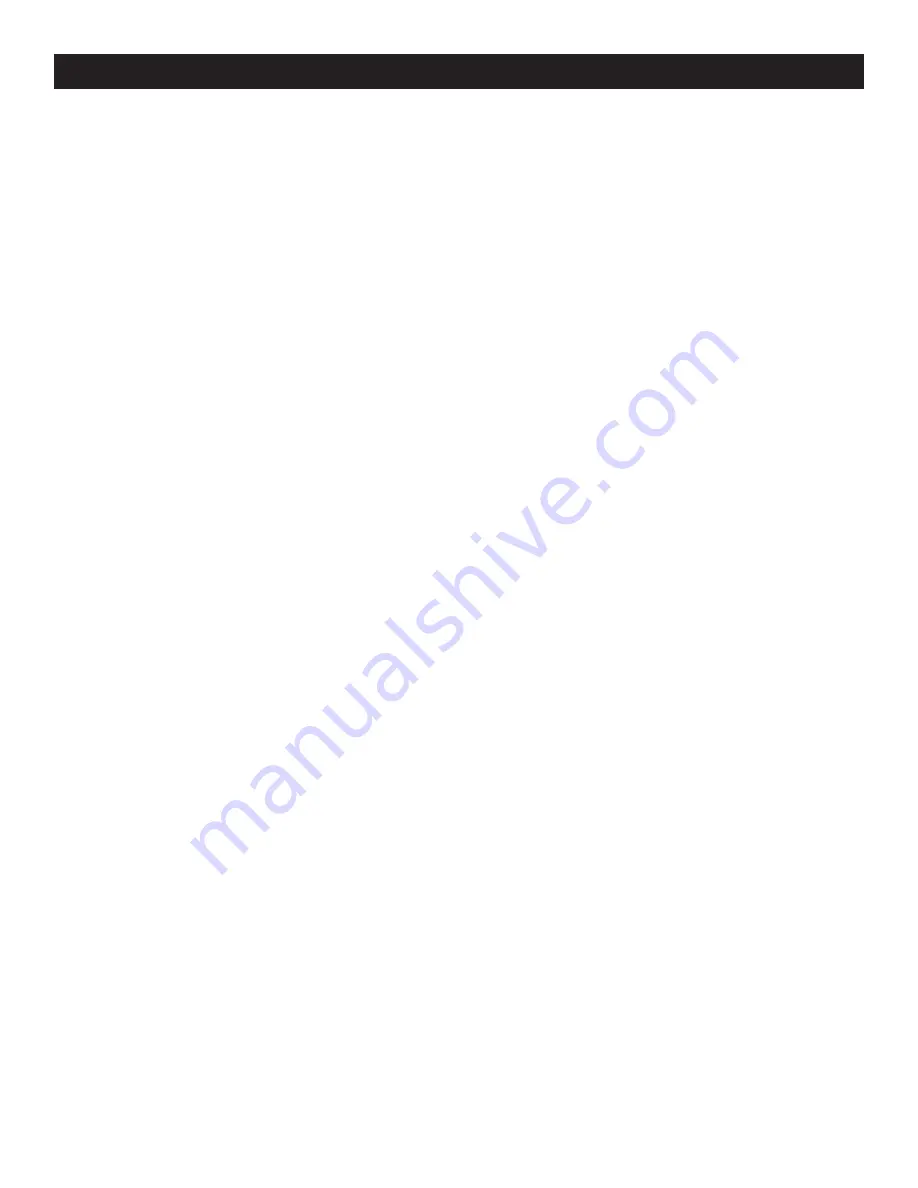
Adjusting the Upper Blade Guide Bearings Parallel to the Blade
(Refer to page 19 parts diagram)
This step may not be necessary, it is factory preset. If adjustment is needed follow the steps
below.
First slightly loosen part #162 (4 each) cap screw on rear of upper Bandsaw housing (see page 19
in parts diagram). This will allow you to adjust the micro adjustment screws on part #164 (Guide
Bracket).
Next place a 3mm “L” wrench through one of the holes in part #169 (Guide Bracket Cover).
Turning clockwise on the left two holes will adjust the left bearings to the right. Turning clockwise
on the right two holes will adjust the right bearings to the left. Check bearings for parallel.
Lastly tighten parts #162 (4) on back of Bandsaw. Repeat steps if the bearings are still not
parallel.
Adjust Upper Bearings Which Will Not Track Close to the Blade
(Refer to page 19 parts diagram)
If the right or left upper bearings do not adjust to within 1/32” of the blade, the guide post (part
#157) may need adjustment.
First slightly loosen parts #162 (4) on the back of the upper Bandsaw cabinet.
Next slide the upper guide post right or left until bearings are properly spaced on each side of
blade. Tighten part #162 (4) on the back of the upper Bandsaw cabinet.
Changing Bandsaw Tire
Use a putty knife to get underneath the tire and pull it up and away from the wheel. Work the putty
knife all the way around the wheel to loosen the tire. Then, use the putty knife as leverage to flip the
tire over and off of the wheel. Clean the inside of the groove, removing any dirt, debris or cement with
lacquer thinner.
Soak the replacement tire in warm water to make it more flexible. Let tire dry and lay on top of wheel.
Start by setting the tire into the wheel groove at the top of the wheel. Using a putty knife, work the
new tire around the wheel, making sure not to slice the tire. If rubber cement is to be used, make sure
16
Loosen slightly the two hex head screws (part#212) which hold the fence rail to the fence body.
Raise or lower the four micro-adjusting screws (part#125) located on the fence body accordingly.
Adjusting Fence 90 Degrees to Table
(Refer to page 18 parts diagram)
Troubleshooting
Summary of Contents for 10-345
Page 6: ...6 List of loose parts in the box marked G Loose Parts List...
Page 17: ...17 Parts Diagram...
Page 18: ...18 Parts Diagram...
Page 19: ...19 Parts Diagram...
Page 22: ...22...