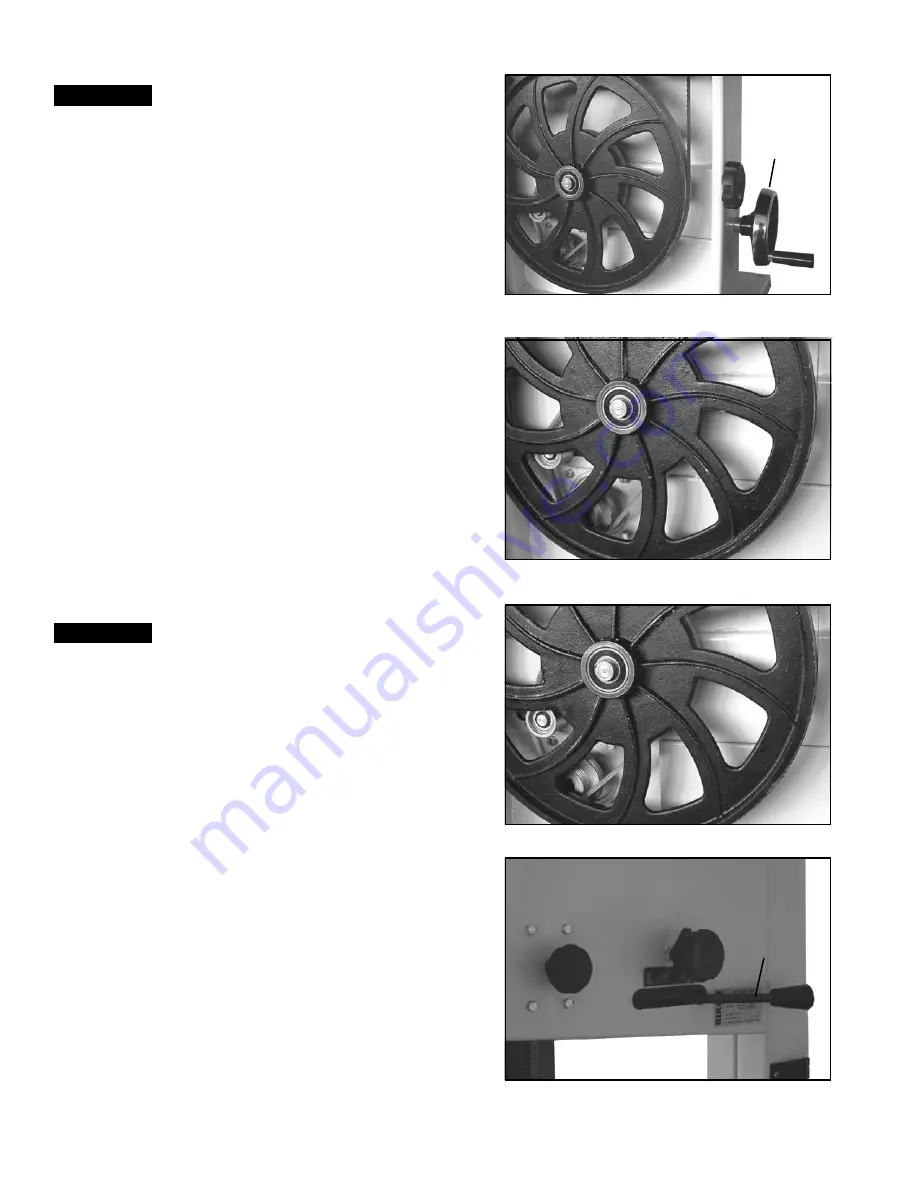
Changing the Blade Speed / Belt Tension
WARNING!
Before changing the speed, always
make sure the machine has been unplugged from
the electrical supply.
This Bandsaw has two blade speeds, low speed
(1445 ft/min) and high speed (2950 ft/min).
The lower wheel has two integral “multi-vee” form
pulleys, and the motor shaft has a twin multi-vee
form pulley. The “multi-vee” belt passes around
the wheel pulley and the motor pulley. The belt
tension is released and applied by using the
handwheel
(A-Fig.18).
For the high speed (2950 ft/min), the belt should
be installed on the rear pulley of both the motor
and the wheel, as shown in Fig.19.
For the low speed (1445 ft/min), the belt should
be installed on the front pulley of both the motor
and wheel, as shown in Fig.20.
To properly adjust belt tension, turn hand-wheel
(A-Fig. 18) until there is 1/2” deflection in the
“multi-vee” belt.
Replacing the Bandsaw Blade
WARNING!
Unplug the machine from the
electrical supply. This ensures that the Bandsaw
will not accidentally turn on if the ON/OFF switch
is bumped.
a) Open the top and bottom wheel doors by
turning the door locking knobs.
b) Release the blade tension by moving the
quick release lever (A-Fig.21) from right
to left. Open the hinged door on the blade
guard by loosening the hex screw.
(A-Fig. 22 on page 15)
c) Remove the saw blade by feeding it
through the slot in the table, upper and
lower blade guides and the slot in the
spine of the machine, being careful not to
cut yourself. Wear gloves for protection.
d) When installing the new blade, ensure
the blade teeth are pointing downwards
and towards you at the position where the
blade passes through the table.
14
Figure 20
Figure 21
Figure 19
Figure 18
A
A
WARNING!
WARNING!
Summary of Contents for 10-325
Page 19: ...Parts Diagram 19 ...
Page 20: ...20 Parts Diagram Cont ...
Page 21: ...Parts Diagram Cont 21 ...
Page 24: ...24 ...
Page 26: ...26 Notes ...
Page 27: ...27 Notes ...