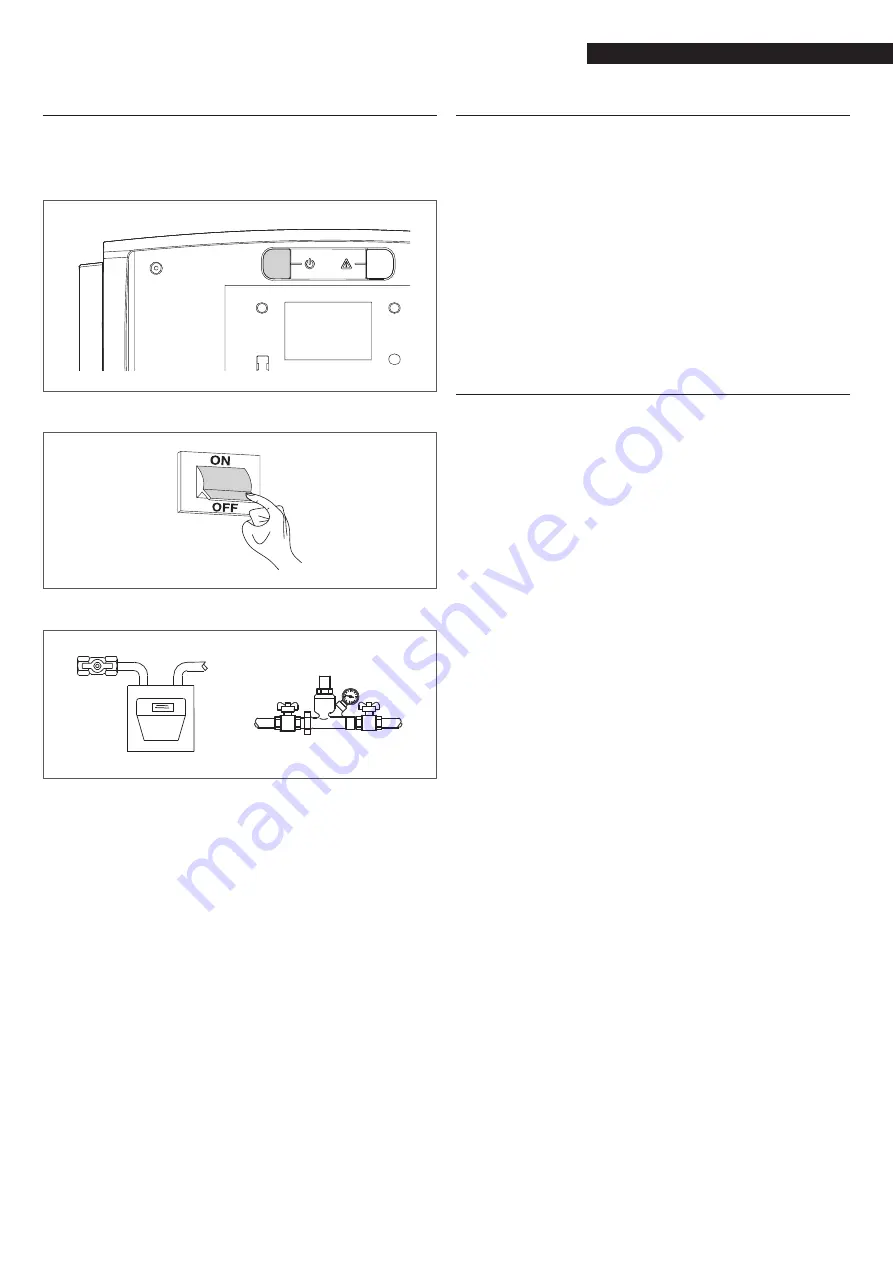
15
SYSTEM MANAGER
SYSTEM MANAGER
2.2
Preparing for extended periods of disuse
If the boiler is not going to be used for an extended period of
time, perform the following operations:
− Turn the control panel power switch OFF and make sure
that the green power indicator goes out
− Turn the main system switch "off"
− Close the fuel cock and heating circuit water cock
− Drain the central heating circuit if there is any risk of
freezing.
9
Contact your local
R
Technical Assistance Service if you
encounter any problems in completing the above proce-
dure.
2.3
Cleaning
Use a cloth damped in soapy water to clean the boiler’s external
casing.
To remove stubborn marks, use a cloth damped in a 50% mix
of water and denatured alcohol or a suitable cleaning product.
Carefully dry after cleaning.
0
Do not use abrasive cleaning pads or powder detergents.
0
Never clean the boiler without first disconnecting it from the
mains electricity supply by turning the mains power switch
and the control panel switch OFF.
9
The combustion chamber and flue pipes must be cleaned
periodically by the manufacturer’s Technical Assistance Ser-
vice or by a qualified heating engineer.
2.4
Maintenance
Please remember that THE PERSON RESPONSIBLE FOR SYSTEM MAN-
AGEMENT MUST ENSURE THAT PROFESSIONALLY QUALIFIED HEATING
ENGINEERS UNDERTAKE PERIODIC MAINTENANCE AND COMBUSTION
EFFICIENCY MEASUREMENTS.
R
’s Technical Assistance Service is qualified to satisfy these
legal requirements and can also provide useful information on
MAINTENANCE PROGRAMMES designed to guarantee:
− Greater safety
− Compliance with applicable legislation
− Freedom from the risk of fines in the event of spot checks.
Regular maintenance is essential for the safety, efficiency and
durability of the boiler.
Servicing is a legal requirement and must be performed at least
once a year by a professionally qualified heating engineer.