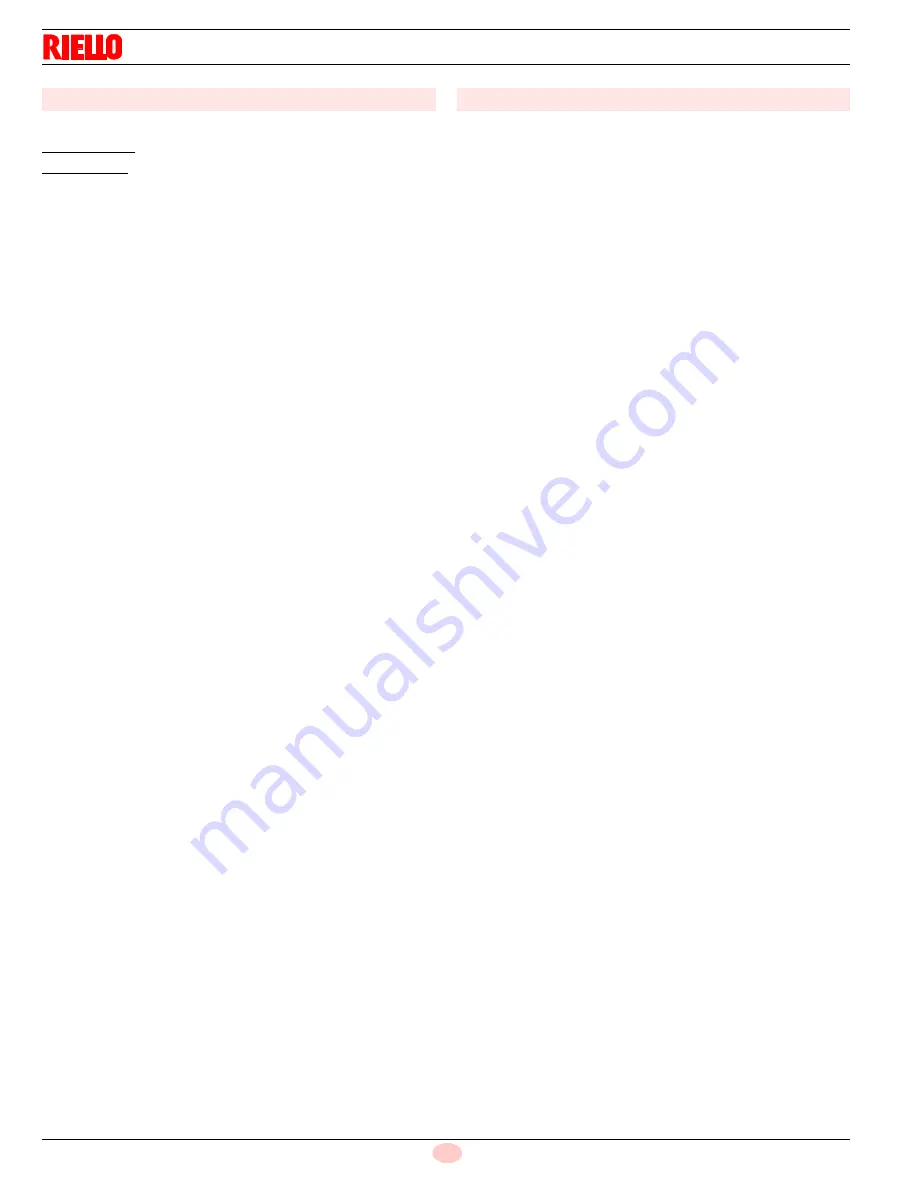
20059594
34
GB
Maintenance
Pump
The depression must be less than 0.45 bar
.
Unusual noise must not be evident during pump operation
.
If the pressure is found to be unstable or if the pump runs noisily,
the flexible hose must be detached from the line filter and the fuel
must be sucked from a tank located near the burner.
This measure permits the cause of the anomaly to be traced to ei-
ther the suction line or the pump.
If the problem lies in the suction line, check to make sure that the
filter is clean and that air is not entering the piping.
Filters
Check the filtering baskets on line and at nozzle present in the sys-
tem. Clean or replace if necessary.
If rust or other impurities are observed inside the pump, use a sep-
arate pump to lift any water and other impurities that may have de-
posited on the bottom of the tank.
Nozzles
It is advisable to replace nozzles every year during regular main-
tenance operations.
Do not clean the nozzle openings; do not even open them.
Flexible hoses
Check to make sure that the flexible hoses are still in good condi-
tion.
Fuel tank
Approximately every 5 years, or whenever necessary, suck any
water or other impurities present on the bottom of the tank using a
separate pump.
Combustion
In case the combustion values found at the beginning of the inter-
vention do not respect the standards in force or, in any case, do not
correspond to a proper combustion, contact the Technical Assis-
tant and have him carry out the necessary adjustments.
Gas leaks
Make sure that there are no gas leaks on the pipework between the
gas meter and the burner.
Gas filter
Change the gas filter when it is dirty.
Combustion
Adjust the burner if the combustion values found at the beginning
of the operation do not comply with the regulations in force, or do
not correspond to good combustion.
Combustion checks
CO
2
It is better to set the burner with CO
2
not higer than 10% (with nat-
ural gas). In this way avoiding a loss of calibration setting (for ex-
ample draft variation) that could cause combustion with little air and
the production of CO.
CO
It must be not higher than 400 PPM.
LIGHT OIL OPERATION
GAS OPERATION
Summary of Contents for RLS 28/E
Page 2: ......
Page 38: ...20059594 36 GB Appendix Spare parts A Appendix Spare parts...